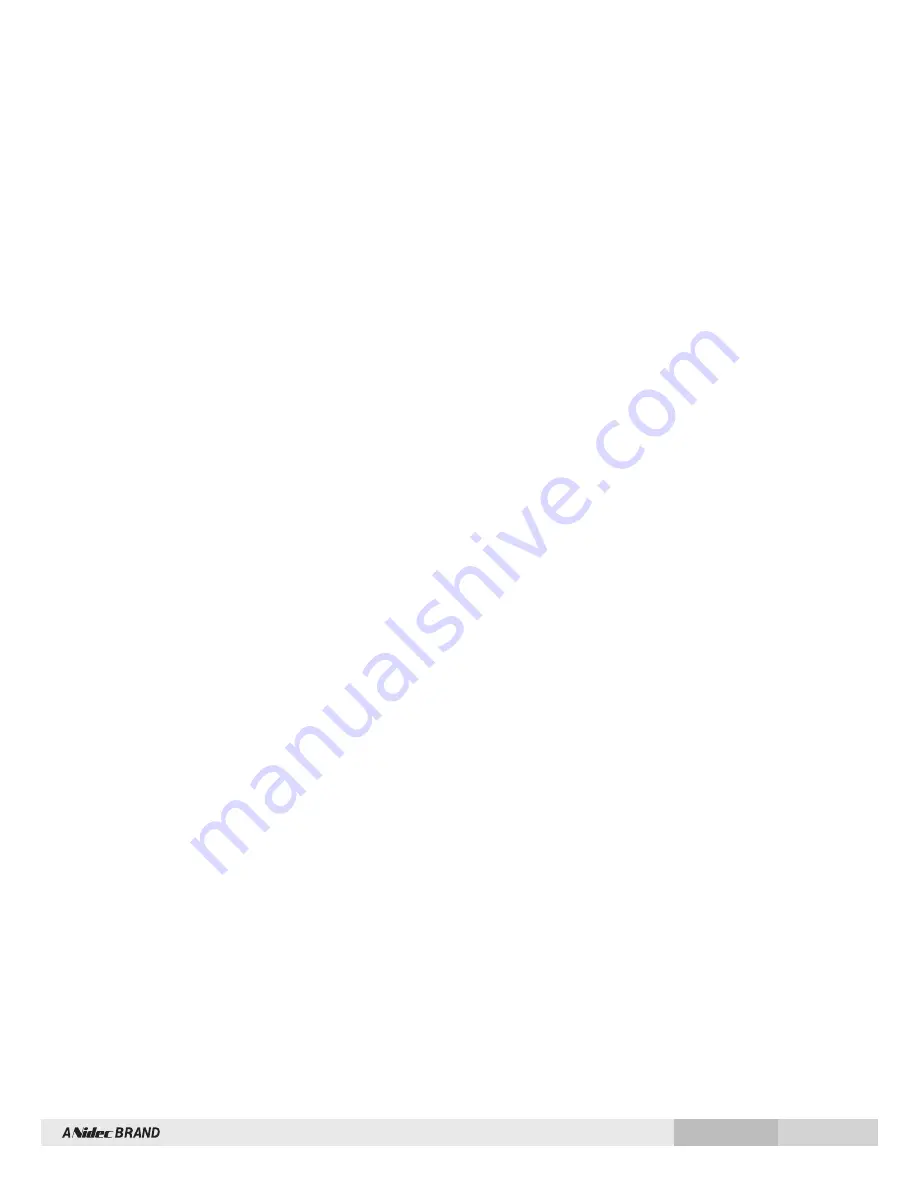
XR56 SMARTSafe
TM
2
Rev: 09-15-2020
In preparation for installing the Model XR56 encoder, it is first necessary
to clean both the accessory motor shaft and the mounting face. These
surfaces must be inspected and any paint, burrs, or other surface
imperfections removed.
Installation procedures should be performed only by qualified personnel.
Safety precautions must be taken to ensure machinery cannot rotate and
all sources of power are removed during installation.
ROTOR INSTALLATION
The motor shaft must project at least 0.66” from the motor face. For set
screw rotors only: Apply anti-seize compound to the motor shaft. For all
rotors: Slide the rotor onto the shaft with the marking “Motor side” facing
in, (toward the motor face). The rotor centerline must match the sensor
centerline. To accomplish this, use the rotor locating gauge (A28503) and
slide the rotor onto the shaft until it is in the proper position as shown
in Figure 1. If a gauge is not available, use the stator housing alignment
grooves as shown in Figure 3.
STANDARD CAM SCREW ROTOR INSTALLATION
Turn the cam screws of the rotor in the directions shown on the rotor to
engage the cams. Tighten to 50-60 in-lb [5.6 - 6.8 N-m] (Fig 2) using the
3mm hex wrench. Total cam screw rotation will be less than one turn.
CAUTION
Do not adjust the cam screws before motor shaft
mounting; bottoming out the screws, or backing them
out excessively, can lead to insufficient shaft holding
force. Thread locker is pre-applied on the cam screws.
LARGE BORE SET SCREW ROTOR INSTALLATION
Apply thread lock er to the rotor set screw holes, preferably from the inside
of the rotor bore before mounting. Tighten the rotor set screws to 15 in-lb
[2 N-m] using the 2mm T-handle hex wrench.
CAUTION
Use only a T-handle or torque hex wrench to tighten set
screws; using a right angle wrench will not provide
enough holding force, and the rotor may slip.
STATOR HOUSING INSTALLATION
The stator housing is attached to the motor using four socket head cap
screws (4) 3/8”-16 x 1.25”, locating on a 5.88” bolt circle. Longer bolts
(not included), are required for sandwich installation between a motor and
a brake. Install the four mounting bolts using thread locker and torque to
approximately 20-30 ft lbs [27 to 40 N-m] using the 5/16” T-handle hex
wrench.
VERIFY ROTOR LOCATION
To ensure the rotor is properly located on the shaft: remove the back cover
if factory-preinstalled, and verify that the outer face of the rotor is at the
same depth as the alignment grooves, using a straight edge tool. (Fig 3)
CAUTION
Do not use silicone sealants or caulk of any kind on the
motor or encoder face; these can cause misalignment
or sensor scraping damage. The XR56 electronics are
fully sealed; water may enter and leave the rotor area as
needed. A drain hole option is available if frequent
moisture buildup is expected.
COVER INSTALLATION
Covers must not interfere with the motor shaft or rotor. The longest shaft
that can be used without interfering is 0.72” [18.3mm] with a standard
flat cover (Cover Style option “F”) and 2.55” [64.8mm] with an extended
“pie pan” cover (Cover Style option “E”). Through shaft covers are avail-
able for other applications (Cover Style option “T”).
EXTENDED COVER MOUNT
(Cover Style option “E”)
The extended cover mounts to the encoder housing using quantity 4 #6-
32 x 0.31” screws, lock washers, and thread locker.
THRU SHAFT AND FLAT COVER INSTALLATION
(Cover Style option “T” and “F”)
The housing has a machined step in the outboard face to accept the cover
and a recessed groove for the retaining ring. Insert the cover, line up ears
on cover, smooth side facing out, fully into the machined step until it seats
against shoulder. Using a spiral assembly method, install the retaining
ring by first inserting the squared off end into the machined groove. Flex
the ring and insert it into the groove walking it around the perimeter (A
flat blade screwdriver can be used). Final position should have the ring
fully seated into groove. Remove the cover by reversing above procedure,
starting with the tang end.
WIRING
Refer to the attached installation drawings referenced above for wiring
diagrams. Use the drawing appropriate for the encoder’s installation
location. Information on specific connector pin-outs and phasing can
be found on labels on the encoders and in the tables included in these
instructions.
The XR56 can be wired for single phase or two phase, either with
or without complements, with or without markers. For bidirectional
operation, Phase A channel typically leads phase B channel for clockwise
shaft rotation as viewed from the anti-drive or accessory end of the
motor (XR56 mounting end). Refer to the pinout and phasing tables for
exceptions.
NOTE
Wiring option “G” provides a pinout compatible with
Northstar
TM
encoders, with a cable shield connection
on pin 10. Note that this option does not ground the
shield.
CORRECTIVE ACTION FOR PHASE REVERSAL
1) Remove Power.
2) Exchange wires on cable, either at encoder cable end,
or at speed controller end (but not both).
a)
Single Ended 2 Phase Wiring
(see wiring diagram)
Exchange A with B.
b)
Differential 2 Phase Wiring
(see wiring diagram)
Exchange either A with A– in the phase A pair OR
B with B– in the phase B pair but NOT both.
3) Apply Power.
4) Verify encoder feedback is correct, using hand rotation
of shaft, or jog mode of the speed controller.
Interconnection cables specified in the wire selection chart are based on
typical applications. Cable must be selected and installed in accordance
with regional standards. Typical interconnection cable is 4 twisted pair
+ overall shield. Recommended cable is Avtron B37178. Alternates
are Belden P/N 1064A or Rockbestos 04P-18 I/S-OS. Actual cables
should be picked based on specific application requirements such as
abrasion, temperature, tensile strength, solvents, etc. General electrical
requirements are: stranded copper, 20 through 16 AWG, twisted wire pairs,
braid or foil individual shields or over-all shield with drain wire, .03uF of
maximum total mutual or direct capacitance and outer sheath insulator. 20
AWG wire should not be used for DC power to the encoder for runs greater
than 200 feet and 22AWG should not be used for runs greater than 100
ft. This is to minimize voltage drop between the encoder and the XRB3
isolator. The smaller conductors are acceptable for the signal lines.