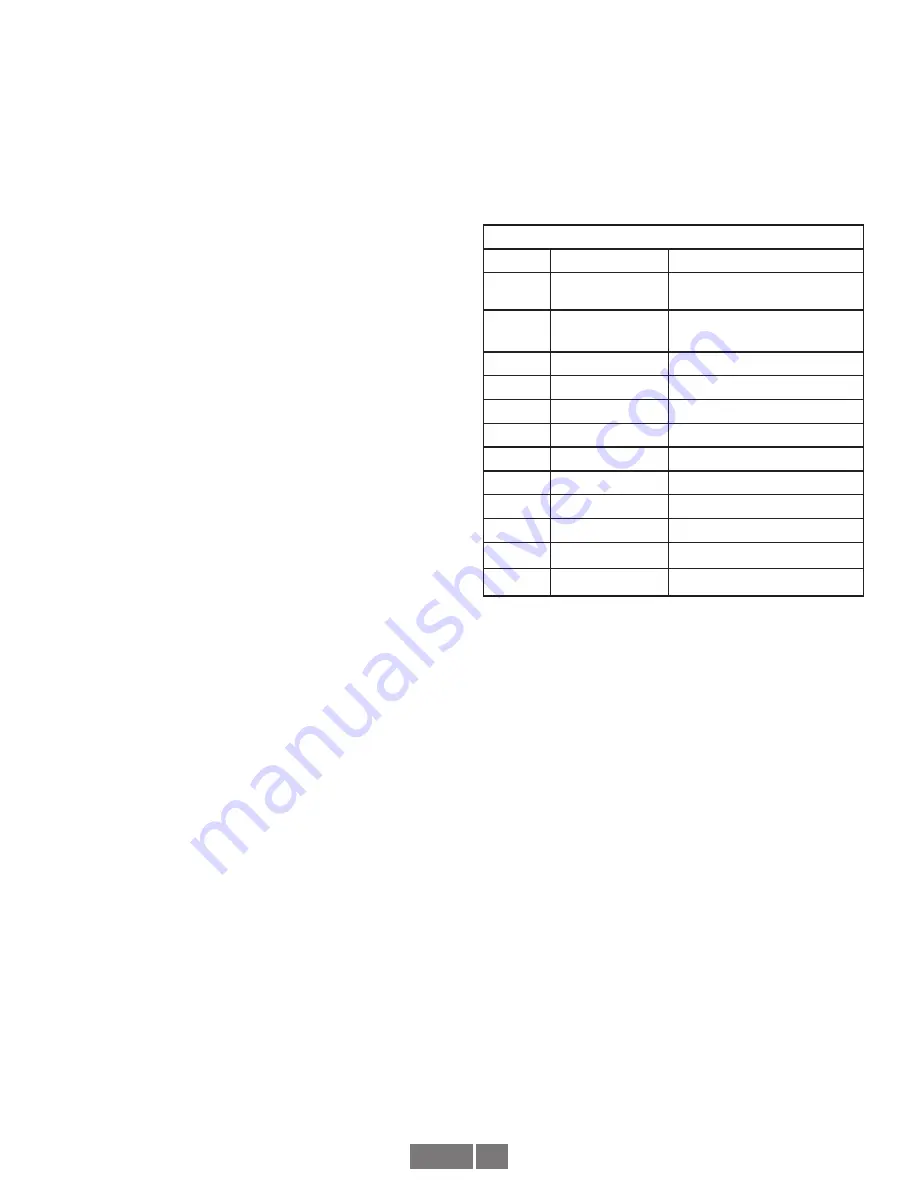
AV6A
6
Note that only devices at each end of the bus should have
termination resistors enabled--if the master/scanner is at one of the
bus, then only one encoder (at the opposite bus end) will require a
termination resistor.
Saving Changes (Required):
To save baud rate/node/resistor changes, write 0x55 0xAA 0xAA
0x55 to SDO object 0x2300
Example, encoder at node 20, store changes
ID: 0x620 0x22 0x00 0x23 0x00 0x55 0xAA 0xAA 0x55
Cycle power after saving changes.
Measuring Position, Speed, and Acceleration
To read position and speed feedback into your device (Acceleration
measurement is not supported.): Following the instructions for your
master/scanner module for the CANOpen network, load the encoder
EDS file into your configuration. Assign it to the correct node
number. Store the configuration to the scanner module.
All of the position data and other parameters will be read by
the scanner module and placed in registers identified in the
configuration package.
Reading data without using the EDS file:
To read position: read SDO object 0x2000 (32 bit unsigned) or SDO
object 0x6004.
Speed measurement is deactivated by default.
To enable speed measurement: write 0x01 to SDO object 0x3010,
subindex 1, and write the speed modulus to subindex 2.
To read the speed after activation: read SDO object 0x3011 (8 bit
unsigned) or SDO object 0x6030.
Acceleration measurement is not supported. SDO object 0x3021
and 0x6040h are reserved for future use but do not indicate
acceleration at this time.
Setting Polling, Cyclic and Sync Mode
Polling, cycling and sync mode are supported by the encoder; use
the parameters supplied in the EDS file to set the appropriate mode.
Store the resulting configuration into the scanner module.
Storing/Saving Encoder Parameters
To store the current encoder operating parameters into non-volatile
memory:
Write 0x55 0xAA 0xAA 0x55 to SDO object 0x2300
Example, encoder at node 20, store changes
ID: 0x620 0x22 0x00 0x23 0x00 0x55 0xAA 0xAA 0x55
No reset is triggered.
Cycle power after saving changes to parameters.
Other Parameters
Contact Nidec Avtron for additional parameters, diagnostic registers,
cam and programmable limit switch functionality and other
advanced features.
CANOPEN TROUBLESHOOTING
For CANOpen: disconnect the power connection, then ensure there
are no short circuits between any of the signal or power wires or
shield.
Viewing on oscilliscope: for CANOpen the transmit and receive
signal pairs should change state rapidly as the controller transmits
messages to the encoder and the encoder replies. Transmission
rates vary, but these messages can be extremely short and typically
require scope triggering to spot them.
For CANOpen, ensure termination resistors are in place (or switched
on) at each end of the cabling system, and that no termination
resistors are in placed or activated in the middle of the system.
Remove the connections to the master controller and all devices,
or power down all devices. Measure the resistance between the
communication wires [Example CANOpen-measure between CAN_L
and CAN_H]. The value should be ~1/2 of the termination resistor
value on the network. For CANOpen, this value should be >50 ohms,
<65 ohms. If the resistance is greater than the limit, a termination
resistor is missing from the network. If the resistance is less than
the limit, there are incorrect termination resistors switched on or
connected to the system.
CANOpen Diagnostic LEDs
LED
Status
Meaning
Run
ERR
Green
Off
Power OK, Operational, CAN
Controller on
Run
ERR
Flickering Green
Flickering Red
LSS or auto-baud detection
active
Run
Blinking Green
Encoder in preoperational state
1X Flash Green
Encoder is stopped
3X Flash Green
Software download in progress
Off
No Power
ERR
Blinking Red
Configuration error
1X Flash Red
CAN Error frames
2X Flash Red
Guard event or heartbeat error
3X Flash Red
Sync message timeout
4X Flash Red
PDO timeout
On (Red)
CAN controller off