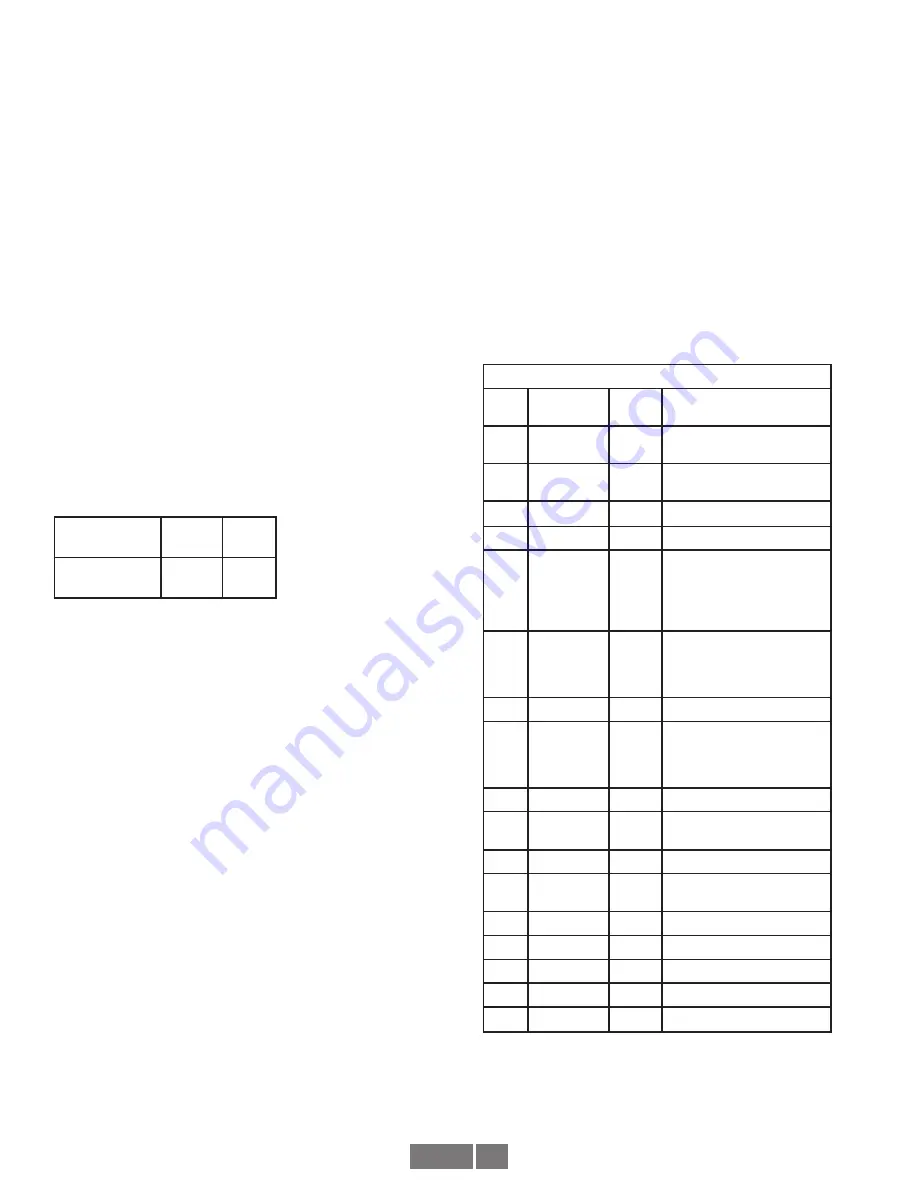
AV6A 14
Profinet IO “N”
Profinet IO is typically a master/slave network-the master/scanner
device gathers data from each (slave) device on the bus. Avtron
encoders are Profinet IO slave devices. Profinet IO commands
include a subset of Profidrive commands-these commands are also
supported by Avtron encoders. Avtron encoders support RT (real
time) and IRT (isochronous real time) functions.
Profinet IO may be wired in several different configurations, but
the best known is a “star” configuration where each device has a
“home-run” network cable that connects to a central switch or hub.
To reduce the cabling requirements, Avtron encoders support
“daisy-chain” configurations. The master device must be at one end
of the bus or connected to a hub or switch. The input signal from
the master or switch is repeated by each encoder to its output port
(labelled “Port 2”), which can in turn be connected to an input Port
1 of another encoder. No external or switched termination resistors
are required for Profinet IO. Power is carried to the device via a
separate set of wires. A maximum of (7) encoders can be daisy-
chained together to a single EtherNet/IP master/scanner or switch
port.
Preferred cable: Nidec Avtron recommends structured Ethernet
wiring systems, available from a broad range of vendors as well as
Avtron.
For more details on Profinet, consult the Profibus Users Association
(PI):
http://www.profibus.com/
Number of
Nodes
1-7
Units
Max. Overall
Cable Length*
330
[100]
ft
[m]
*Using Ethernet standard cable, CAT6 or CAT5e required
Setting Station/Node, Baud Rate, Duplex
NOTE: There is no hardware method to set the Station/Node number
(IP address) for Avtron EtherNet/IP address.
Setting IP Address via STEP7 (Siemens) software:
Begin with a factory-default encoder. Make a physical Ethernet
connection between a PC and the encoder. Run the STEP7
software. Under menu item PLC->Ethernet->Edit Ethernet Mode-
>Browse. STEP7 will produce a list of all encoders via MAC-
address. Optional: use the flash LED button to cause the LED
to flash to verify communication with the encoder. Select menu
item Use IP Parameters, enter the IP address then->Assign IP
Configuration. Enter the device name. Any IP address from 0.0.0.0
to 223.255.255.255 (excluding 127.x.x.x) is permitted.
Cycle power.
The encoder should now operate at the assigned IP address,
which can be validated using the ping command from the PC. The
assigned name can be used throughout STEP7 software to address
the encoder.
Note that if more than one encoder is to be used on the same
Profinet IO network, each encoder must be assigned a unique name,
and individual encoders must be connected one-by-one to assign
names using STEP7 software during setup.
Ethernet baud rate and duplex are auto-detected by the encoder, no
settings are required. 100mBit and 10mBit are supported, Gigabit
Ethernet is not supported at the encoder level but may be utilized at
the switch backbone level. Consult Nidec Avtron if manual forcing of
duplex is required.
Measuring Position, Speed, and Acceleration
Avtron encoders support three modes of operation:
Standard
Profile (Profidrive) 4.0 (supports DP-V2 commands)
Profile (Profidrive) 4.1 (supports DP-V2 commands)
Profile 4.0 and 4.1 require a special GSDML file, contact factory.
To read position and speed into your device (acceleration
measurement is not supported directly):
Following the instructions for your master/scanner module for
the Profinet IO network, load the encoder GSDML file into your
configuration. Assign it to the correct IP address node number.
Store the configuration to the scanner module.
All of the position data and other parameters will be read by
the scanner module and placed in registers identified in the
configuration package.
Cyclic Data
ID
(dec)
Function
Type
Notes
3
Master
heartbeat
UINT
4
Slave
heartbeat
UINT
6
Velocity
INT
8
Velocity
DINT
9
Ctl Word
UINT
bit 11=preset/zero
bit 12=capture position
bit 13=enable cyclic xmit
bit 14=disable error xmit
bit 15=clear errors
10
Status
UINT
Bit 12=ack capture position
Bit 13=ack cyclic xmit req
Bit 14=ack disable error
Bit 15=encoder error
11
Position 1*
DINT
12
Position 2*
DINT
If encoder error (bit 15,
ID10), error message output
to Position 2 instead of
position.
39
Position 3
DINTx2 right-aligned
19
Vel. Update
EUINT
0=1sec, 1=0.1s, 2=0.01s,
3=RPM
29
Status
BYTE
2A
Units per
span
UDINT
read only, set w/0x10
2B
# Spans
UINT
# revolutions
33
Offset
DINT
Poffset
64
Device Type DINT
0x22 = Encoder
65
Rollover
DINT
0=off, 1=on, 2=auto
66
Vel’cty Filter DINT
0=low pass, 1=mid, 2=off
* Depending on the mode of operation selected, the position data is
aligned differently, but always presented little-Endian (right most bit
is least significant):
Standard Profile: data is right-justified: Single-turn data/data within