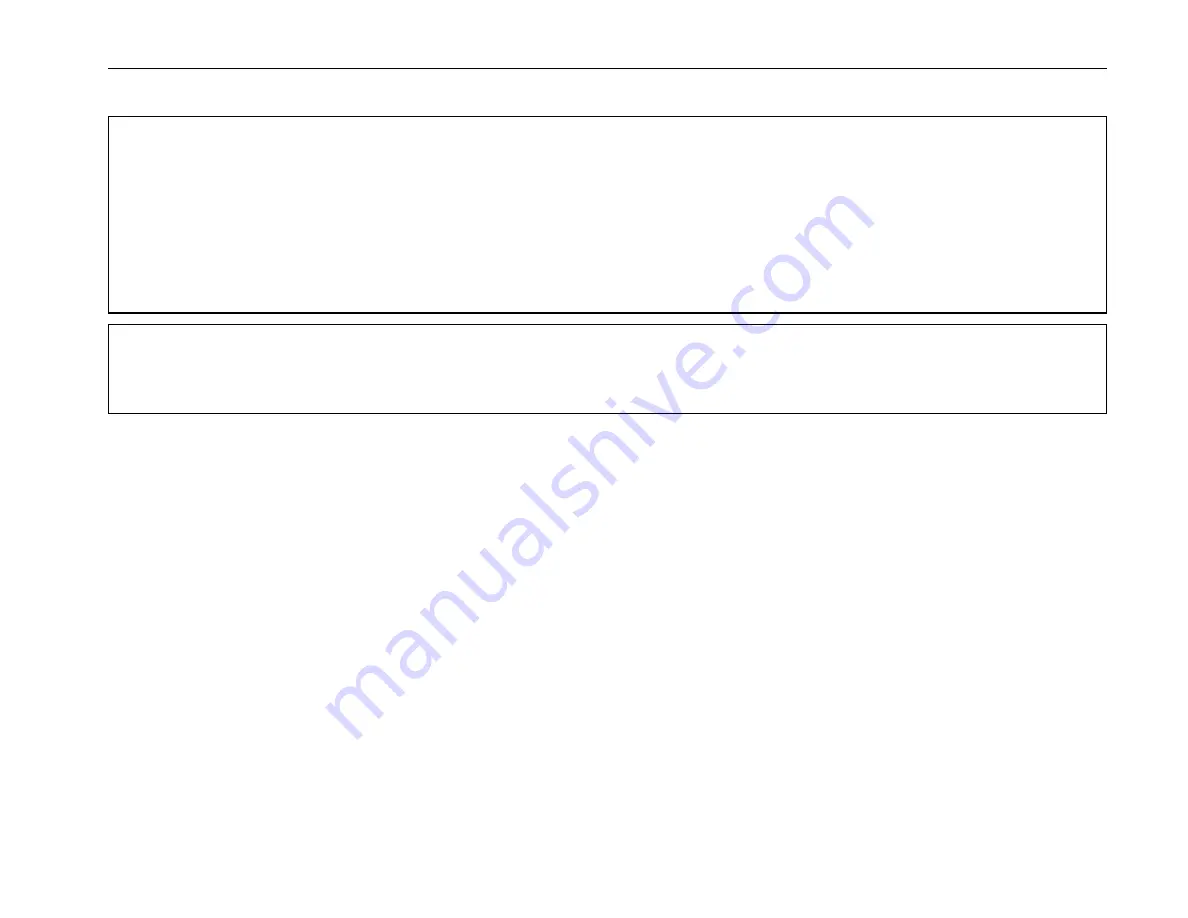
Page 9-3
PROBLEM
REASON
SOLUTION
a.) Lifting large number of harnesses.
b.) Harness or treadle cables routed
improperly.
a.) Lubricate loom.
Reduce spring lever tension if possible.
b.) Check routing of cables.
Make sure all cables are on pulleys.
9.)
Treadles difficult to operate
.
10.)
Large warp build up alters shed
size
.
a.) Folding legs need adjustment.
a.) Adjust folding legs so that they are
being held in the outer or center slots
on the support arms (see Figure 3).