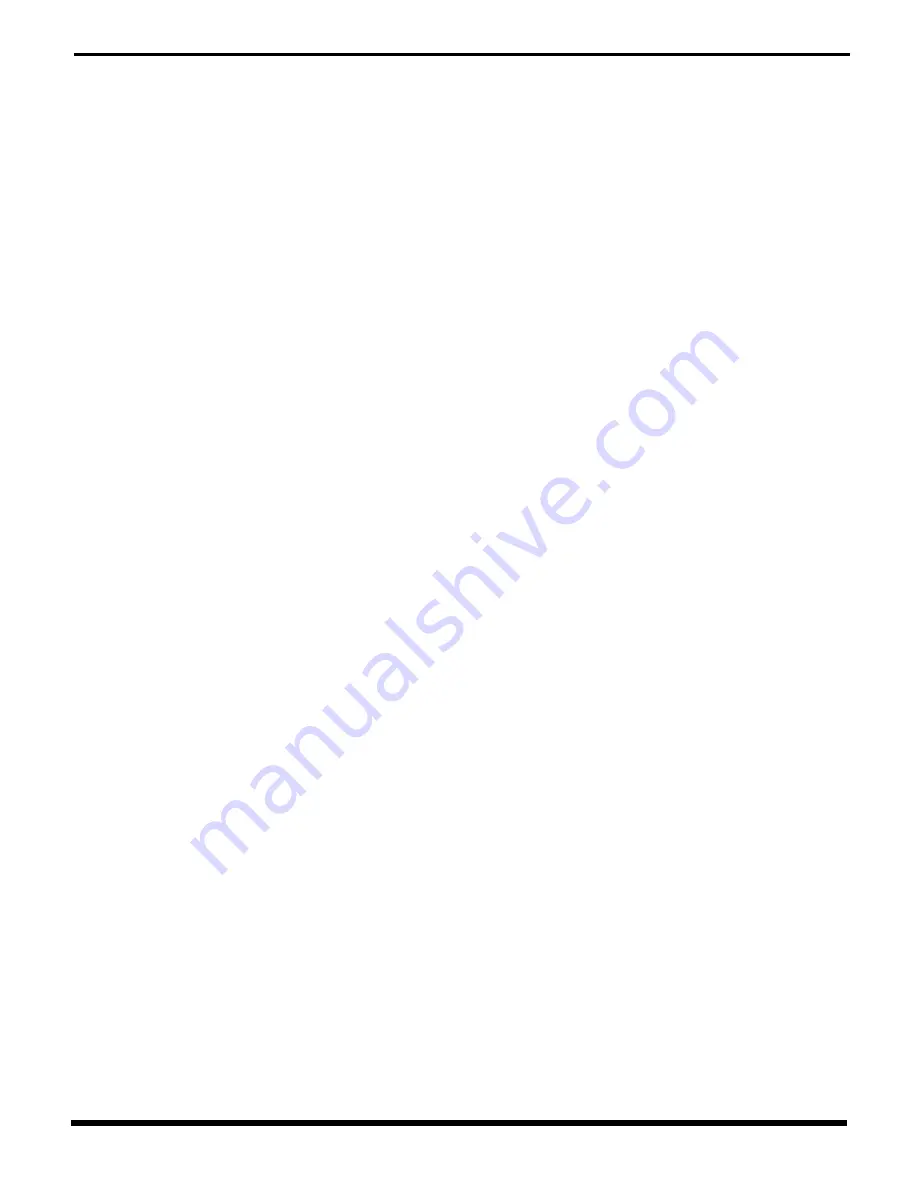
Page 9
Repair and Maintenance Instructions
Repair and Maintenance Instructions
When it has been determined that the Controlair®
Valve requires repairs, the following general
instructions are recommended.
Disassembly, Cleaning and Lubrication
Completely disassemble the Controlair valve. Wash
all metal parts in a non-flammable solvent. Rinse
each part thoroughly and blow dry with low
pressure air.
Inspect and clean the inlet filter Item #17 and both
gaskets Item #18. Be sure all passages in the body
and pipe bracket and sensing port orifice in top of
the diaphragm chamber are clean and unrestricted.
Examine all parts carefully. Replace all rubber parts
and all worn or damaged parts.
The use of repair
kits is recommended.
Reassemble
Refer to exploded Parts and Assembly Views.
Valves should always be reassembled using new
rubber parts.
Lubricate all metal to metal wear surfaces with
Lubriplate 107 Grease. Lubricate all the rubber
parts,
except the diaphragm
with Dow Corning
No. 55 Pneumatic Grease.
The exhaust valve and seat if not replaced should
be polished for minimum leakage using a 600 grit
lapping compound. Be sure to clean these parts
prior to installing in the valve.
Installing the knob (Item #33a), seat the knob on
the shaft, Item #25 before installing the set screw,
Item #33b.
Do not over torque the set screw.
Adjustments
There is one adjustment that can be made to the H-
4 Controlair Valves. This is the adjusting screw item
#1, that varies the output pressure.
Graduated Output Pressure Adjustments
Adjusting screw Item #1 varies the maximum
pressure setting. Turning the adjusting screw “in”
raises the
maximum
pressure. Turning the screw
“out” decreases the
maximum
pressure. The
maximum control pressure adjustment should not
exceed the maximum control pressure shown in the
Identity Schedule for that part number. (Control
Springs are color coded).
The maximum output pressure rating can be
changed by changing the control spring Item #5.
With air supplied to the valve, move handle from
start to full travel position. Adjust graduating valve
screw Item #1 to obtain the maximum control
pressure per Identity schedule. Move handle back
to neutral position and
note
delivery line is
exhausted to zero.
Special Preload Setting
This setting calls for a predetermined delivery
pressure.