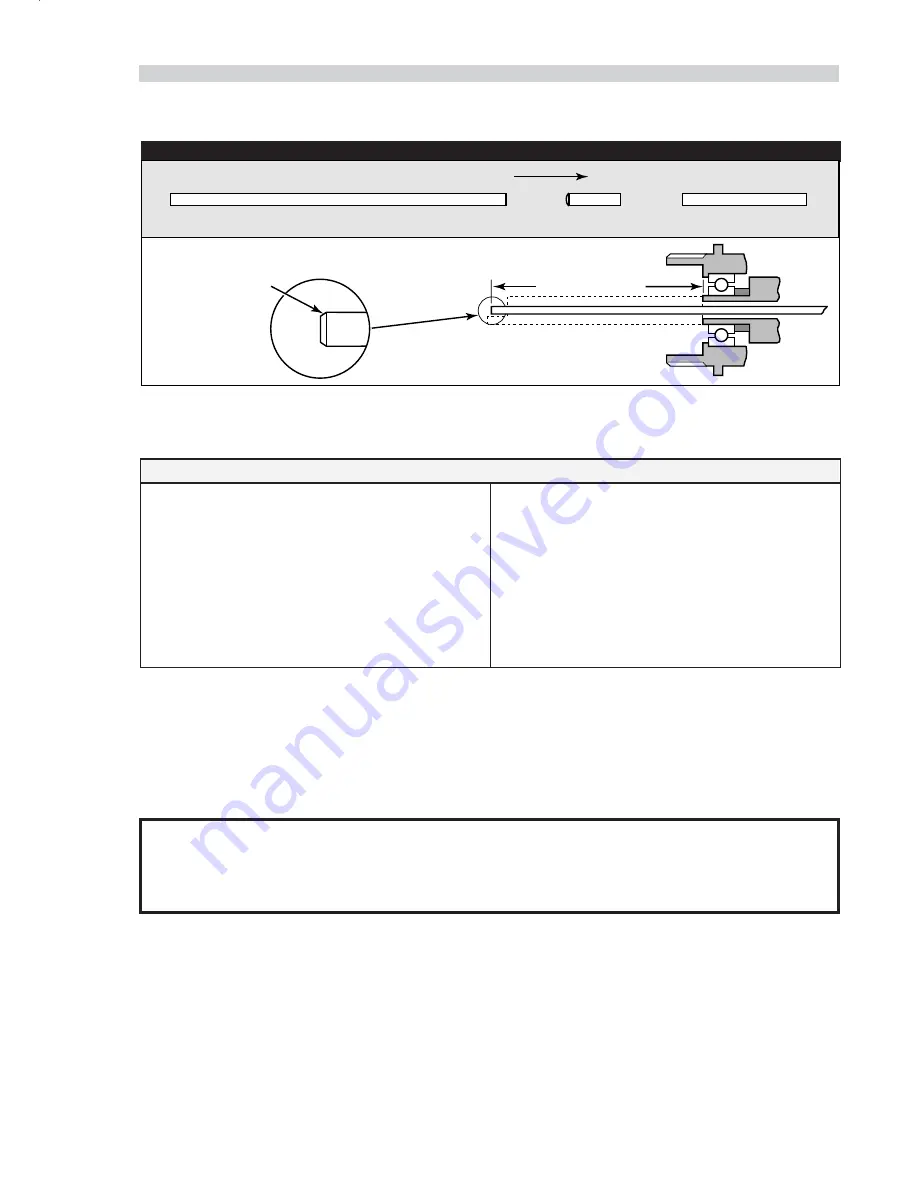
11
M A I N T E N A N C E
Every 200000 cycles the tool should be completely dismantled and components replaced where worn, damaged or when
recommended. All ‘O’ rings and seals should be replaced with new ones and lubricated with Moly Lithium grease EP 3753
before assembling.
I M P O R T A N T
Safety Instructions appear on pages 2 & 3.
The employer is responsible for ensuring that tool maintenance instructions are given to the appropriate personnel. The
operator should not be involved in maintenance or repair of the tool unless properly trained.
The airline must be disconnected before any servicing or dismantling is attempted, unless specifically instructed not to.
It is recommended that any dismantling operation be carried out in clean conditions.
Item
numbers in bold
refer to the General Assembly drawing and parts list (pages 14 and 15).
Prior to dismantling the tool it is nesessary to remove the nose assembly. For simple removal instructions see the nose assemblies section,
page 8 and 9.
For total tool servicing we advise that you proceed with dismantling the sub-assemblies in the order shown on pages 12 and 13.
LONG PUSH ROD
SHORT PUSH ROD
REAR OF TOOL
37.85mm/38.1mm
(1.49”)/(1.5”)
0.4mm(.015’) RAD
OR 45
°
CHAMFER
NEEDLE ROLLER
FITTING NEW REVERSE CONTROL RODS
FIRST AID
SKIN: As the grease is completely water resistant it is best
removed with an approved emulsifying skin cleaner.
INGESTION: Make the individual drink 30ml Milk of
Magnesia, preferably in a cup of milk.
EYES: Irritant but not harmful. Irrigate with water and
seek medical attention.
ENVIRONMENT
Scrape up for burning or disposal on approved site.
M O L Y L I T H I U M G R E A S E E P 3 7 5 3
S A F E T Y D A T A
FIRE
FLASH POINT: Above 220
°
C.
Not classified as flammable.
Suitable extinguishing media: CO
2
, Halon or water spray
if applied by an experienced operator.
HANDLING
Use barrier cream or oil resistant gloves
STORAGE
Away from heat and oxidising agent.
For lubricating internal tool parts other than those described previously, use Moly Lithium Grease EP3753 (part number 07992-00020)