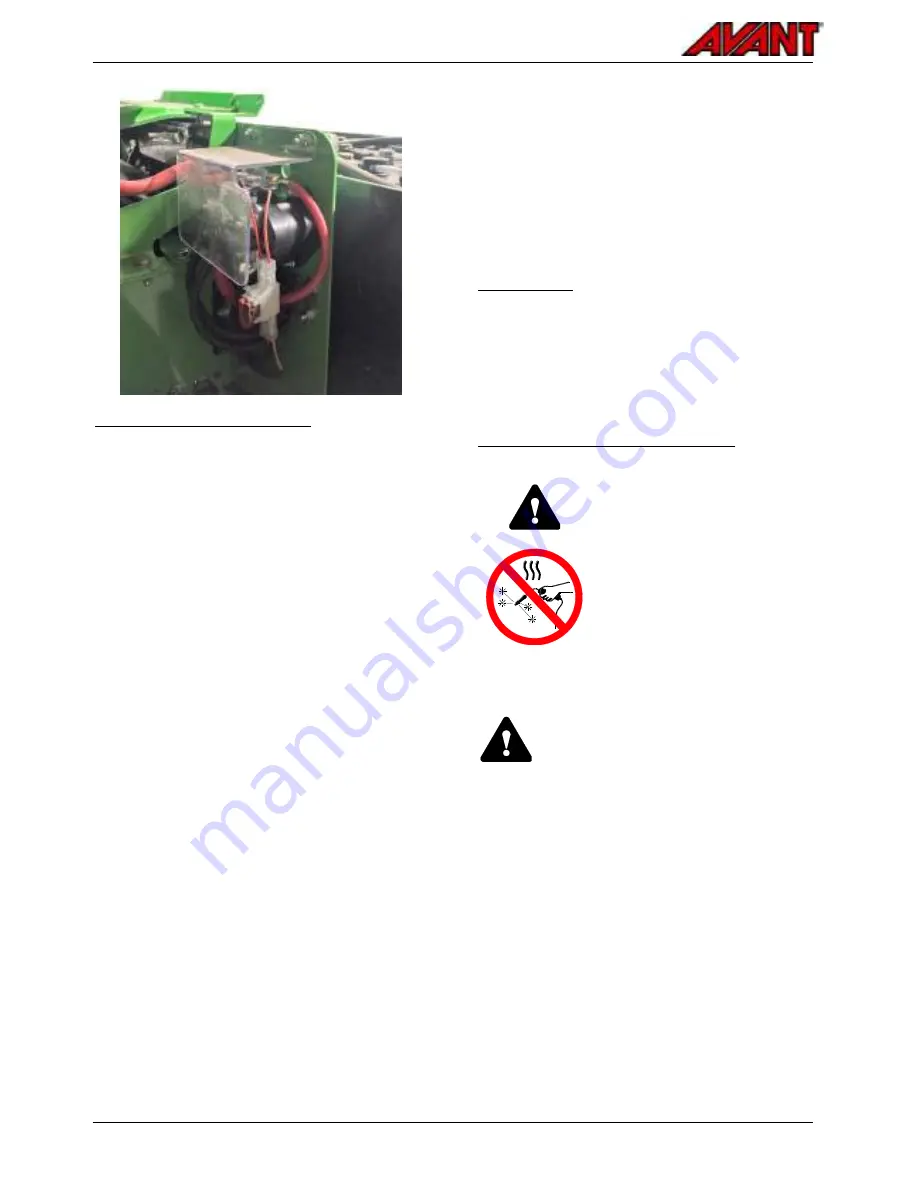
Avant e5
86
Inverter diagnostic codes
The loader is controlled via CAN bus system. The
two electric motor controllers check the electric motor
related systems during start-up of the loader.
In case the inverter that controls the auxiliary
hydraulics pump has detected a fault requiring
service, the multi function display will show a fault
code. The multi function display can display fault
codes stored by the electric motor controller of the
auxiliary hydraulics pump. Any fault code related to
the inverter of the drive pump will by displayed with
LED lights on the side of the inverter.
The electric system may go into to fault mode, which
will reduce power output to protect the battery and
electric systems. If necessary, the loader can be
driven to a safe location, but must not be loaded or
used more than absolutely necessary. The loader
must be checked and serviced by authorised service
before continuing use.
Diagnostics fault codes
Fault codes may help diagnosing a problem when
communicating with authorised service. If you see an
error code message displayed on the multi-function
display, for more information, contact your local
Avant service. Detailed iInterpretation of fault codes
and MIL reset require contact with service.
Codes start with the letter F and six numbers after it,
such as F_ _ _ _ _ _. The first number indicates the
severity of the error type:
F1 _ _ _ _ _ is an information code, that warns
about low battery or similar faults with low
severity.
F2 _ _ _ _ _ and F3 _ _ _ _ _ warn about
functional faults, such as sensor errors or if a
wrong sequence of controls is used. Restart of
the loader may solve the issue.
F4 _ _ _ _ _ indicates a severe fault that must be
repaired before continuing the use of the loader.
If there are multiple fault codes stored, the code for
the most severe fault will appear on the display.
Light bulbs
1.
Front lights
LED unit
2.
Work lights
LED unit
3
Road traffic headlights:
H7
Metal structures of the loader
Contact Avant service in case the
steel structure of the loader gets
damaged. A faulty reparation, or
wrong methods and materials used
for
reparation,
can
cause
hazardous
failures
or
further
damage the loader.
In case the ROPS safety frame or the FOPS
canopy of the machine gets damaged, the
machine must be taken to Avant service for
checking. It is not allowed to repair the
ROPS and FOPS.
https://tractormanualz.com