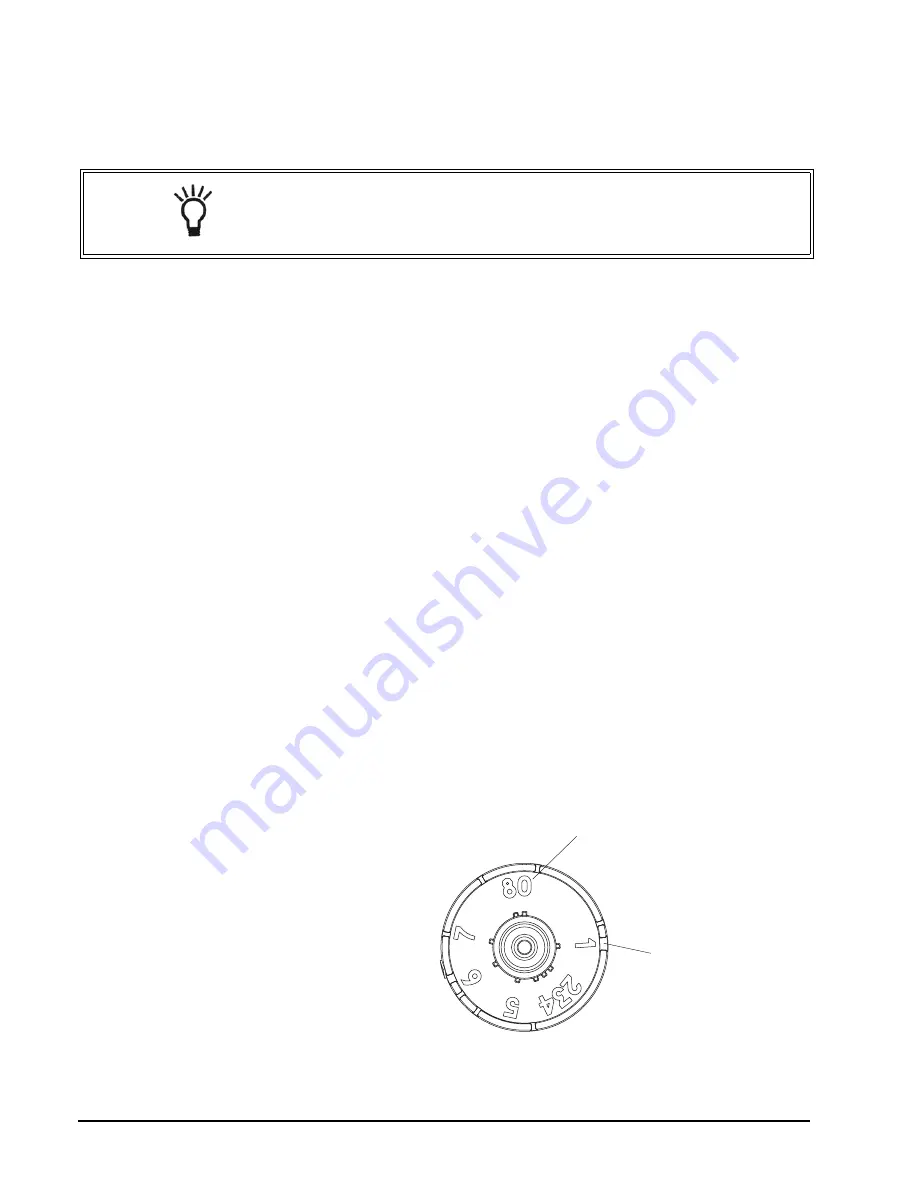
22
EQUIPMENT INSTALLATION
Rev A
100 VAC, 120 VAC and 230 VAC AC Adapters:
Make sure power source matches the rating printed on the AC adapter.
The 700 Series controller is available in two power configurations. The
North American controller operates on 60 Hz. If the incoming power is 50
Hz, the "North American" controller will not function. The error code
"ERR 2" will show on the display.
The "World" controller will sense the input power as 50 or 60 Hz and
operate accordingly.
Controller Location
The 700 Series controllers are designed to be mounted on the valve or
attached to a flat surface. Installations that do not provide easy access to
the valve can have the controller mounted for remote operation.
A remote mount connection, P/N 1256257, is available for the 700 Series
controller.
Valve Camshaft
The front end of the camshaft has an indicator cup. The cup has slots in
the outer periphery and numbers on the inside face (Figure 13).
The numbers can be seen with the cover off, from the front over the top of
the controller. The number at the top indicates which regeneration cycle is
currently in progress.
Figure 13
Camshaft Front End for 255, 263, and 268 valve bodies
The corresponding slot for the number is positioned at the optical sensor
which is approximately 90 degrees out of phase.
NOTE:
The power source should be constant. Be certain the AC adapter is not
on a switched outlet. Power interruptions longer than 8 hours may cause the
controller to lose the time and day settings. When power is restored, the day
and time settings must then be re-entered.
Treated Water Slot
Treated Water Indicator
(normal operation)