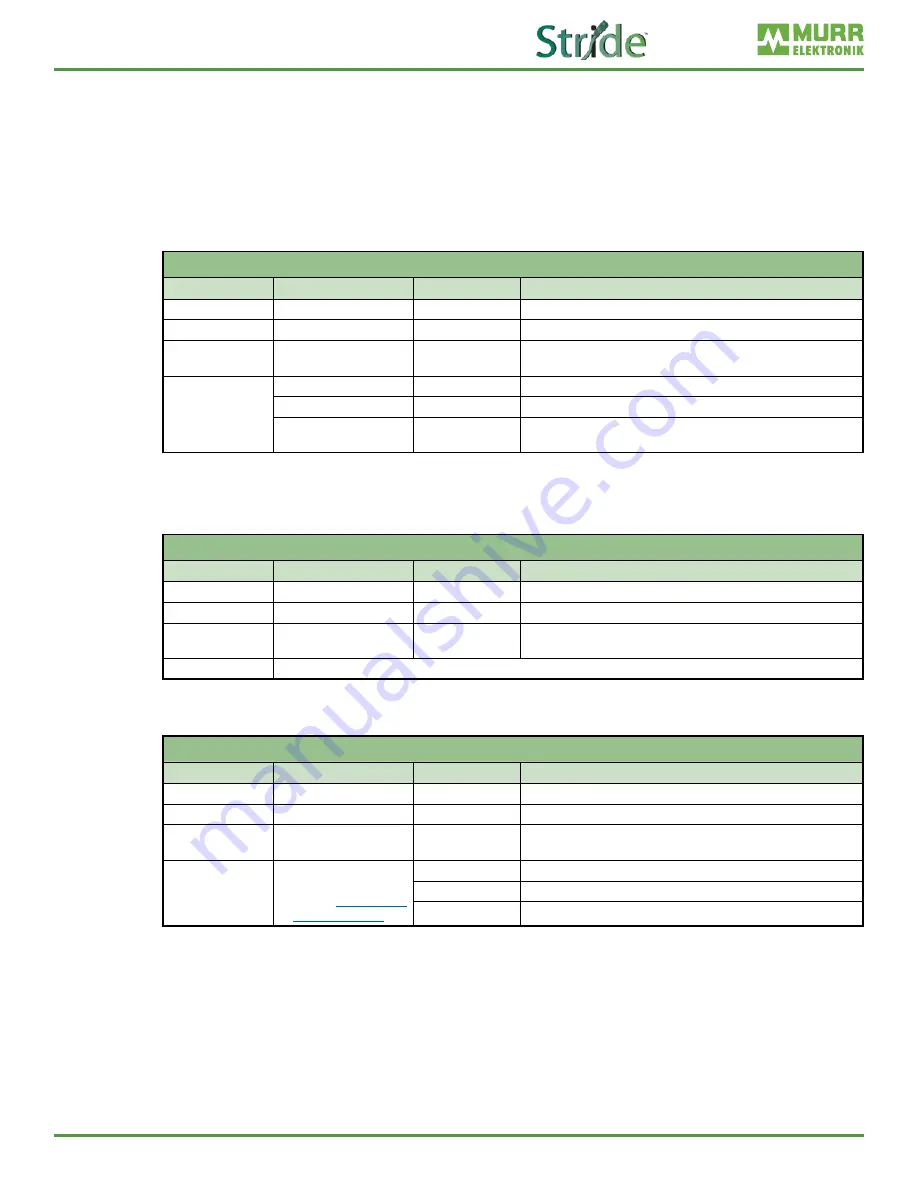
SIOL-EI8B-USER-M
65
Operation
Powered by
Version 1, May 2022
9.3.2. Writing an IO-Link device index
Write ISDU Request
Writing an IO-Link device index
➔
To write to the index of a connected IO-Link device, use the EtherNet/IP service Write_ISDU 76 (0x4C).
➔
Send the service to the correct attribute of the IO-Link device parameter object (class code 0x83).
➔
An attribute represents the IO-Link port to which the IO-Link device is connected.
Structure of a write ISDU service request
Structure Of A Write ISDU Service Request
Name
Value
Type
Description
CIP Service
76 (0x4C)
-
ISDU write service
CIP Class
131 (0x83)
-
IO-Link Device Parameter Object
CIP Instance
1 ... Number of
available IO-Link Ports
-
Addresses the IO-Link Port to which the IO-Link device is connected.
CIP Data
Index
UINT
IO-Link ISDU object index
Subindex
USINT
IO-Link ISDU object subindex
Data
ARRAY of BYTE Data that shall be written to IO-Link device.
Maximum number of bytes: 232
Write ISDU Response
Positive Response (CIP Status in service response == 0)
The positive response to this service does not hold any CIP data.
Positive Response (CIP Status In Service Response == 0)
Name
Value
Type
Description
CIP Service
76 (0x4C)
-
ISDU write service
CIP Class
131 (0x83)
-
IO-Link Device Parameter Object
CIP Instance
1 ... Number of
available IO-Link Ports
-
Addresses the IO-Link Port to which the IO-Link device is connected.
CIP Data
The positive response to this service does not hold any CIP Data (Number of bytes: 0).
Negative Response (CIP Status in service response != 0)
Negative Response (CIP Status In Service Response != 0)
Name
Value
Type
Description
CIP Service
76 (0x4C)
-
ISDU read service
CIP Class
131 (0x83)
-
IO-Link Device Parameter Object
CIP Instance
1 ... Number of
available IO-Link Ports
-
Addresses the IO-Link Port to which the IO-Link device is connected.
CIP Data
The structure of the
error codes can be
found in Section 9.3.3,
UINT
IO-Link Master Error
USINT
IO-Link Device Error
USINT
IO-Link Device Additional Error Code