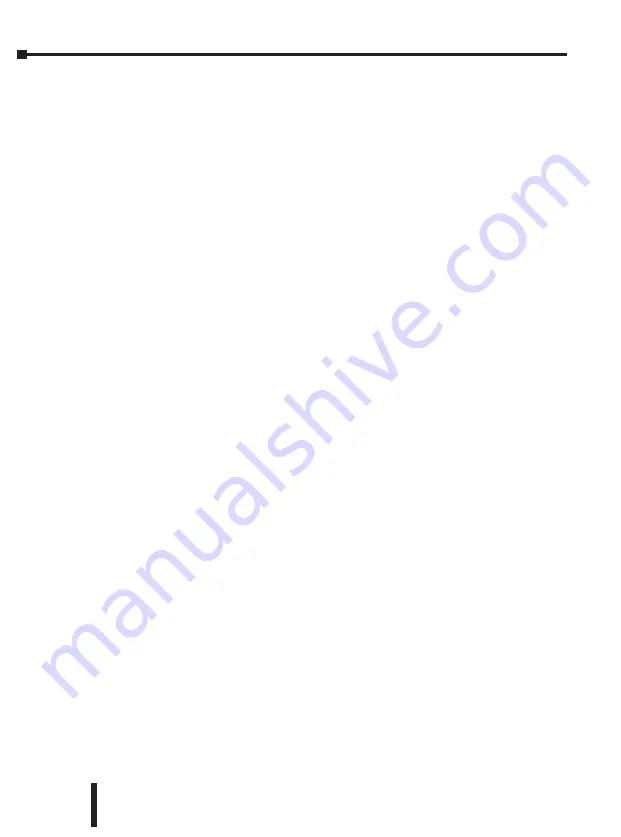
Chapter 3: Applications
3.3 – Concepts and Principles of Fixed-Speed Induction
Motor Starting and Control
Since its invention one hundred years ago, the standard three-phase induction motor has become
one of the most familiar items of industrial equipment ever known. Due to its simplicity of
construction, low cost, reliability, and relatively high efficiency, it is likely to remain the prime
source of mechanical energy for the foreseeable future.
3.3.1 – Introduction
Energy conversion, from the electrical supply to rotating mechanical energy, is a characteristic of
all motors. To regulate energy flow, most motor circuits require a mechanism to connect and
disconnect them from their electrical power source. Electro-mechanical switches, known as
“contactors”, are the standard means of achieving this control. Even today, more than one
hundred years after their introduction, contactor-based systems remain the most widely used
method of motor control.
Nevertheless, there is a definite trend towards more sophisticated electronic systems of control
being applied to fixed-speed motor drives. This section will discuss these forms of control; namely
electronic microprocessor-controlled optimizing soft starters such as the SR44.
3.3.2 – The Induction Motor
In order to appreciate the benefits of using an electronic controller, it is important to have some
understanding of the characteristics and limitations of the induction motor and the electro-
mechanical systems currently used to control them.
The standard, fixed-speed induction motor fulfils two basic requirements:
• To accelerate itself and its load to full speed (or speeds with multi-speed motors).
• To maintain the load at full speed efficiently and effectively over the full range of loadings.
Due to the constraints of materials and design, it can be difficult to achieve both objectives
effectively and economically in one machine.
So, how does a motor start in the first place? As mentioned previously, motors convert electrical
energy drawn from the power supply into a mechanical form, usually as a shaft rotating at a speed
fixed by the frequency of the supply. The power available from the shaft is equal to the torque
(moment) multiplied by the shaft speed (rpm). From an initial value at standstill, the torque varies,
up or down, as the machine accelerates until reaching a peak at about two thirds of full speed,
and then dropping to zero at synchronous speed. This characteristic means that induction motors
always run at slightly less than synchronous speed in order to develop power (the ‘slip speed’), and
hence the term asynchronous. Figure 3.3.2.1 shows a graph is of an induction motor torque/speed
curve, and illustrates this important characteristic of asynchronous three-phase induction motors.
SR44 Series Soft Starter User Manual
1st Ed, Rev B 07/31/2019
3–8
Summary of Contents for Stellar SR44
Page 1: ...STELLAR SR44 SOFT STARTER USER MANUAL SR44 M WO 1st Edition Revision B...
Page 2: ...BLANK PAGE SR44 Series Soft Starter User Manual 1st Ed Rev B 07 31 2019...
Page 6: ...SR44 Series Soft Starter User Manual 1st Ed Rev B 07 31 2019 w 4 BLANK PAGE...
Page 8: ...BLANK PAGE SR44 Series Soft Starter User Manual 1st Ed Rev B 07 31 2019...
Page 12: ...Table of Contents BLANK PAGE SR44 Series Soft Starter User Manual 1st Ed Rev B 07 31 2019 t 4...
Page 23: ...ELECTRICAL INSTALLATION 2 CHAPTER CHAPTER 2 2 CHAPTER BLANK PAGE 2 1c...
Page 75: ...KEYPAD MENU ITEMS AND PARAMETERS CHAPTER 5 CHAPTER CHAPTER 5 BLANK PAGE 5 5 1c...
Page 237: ...BLANK PAGE SR44 Series Soft Starter User Manual 1st Ed Rev B 07 31 2019...
Page 238: ...SR44 Series Soft Starter User Manual 1st Ed Rev B 07 31 2019...