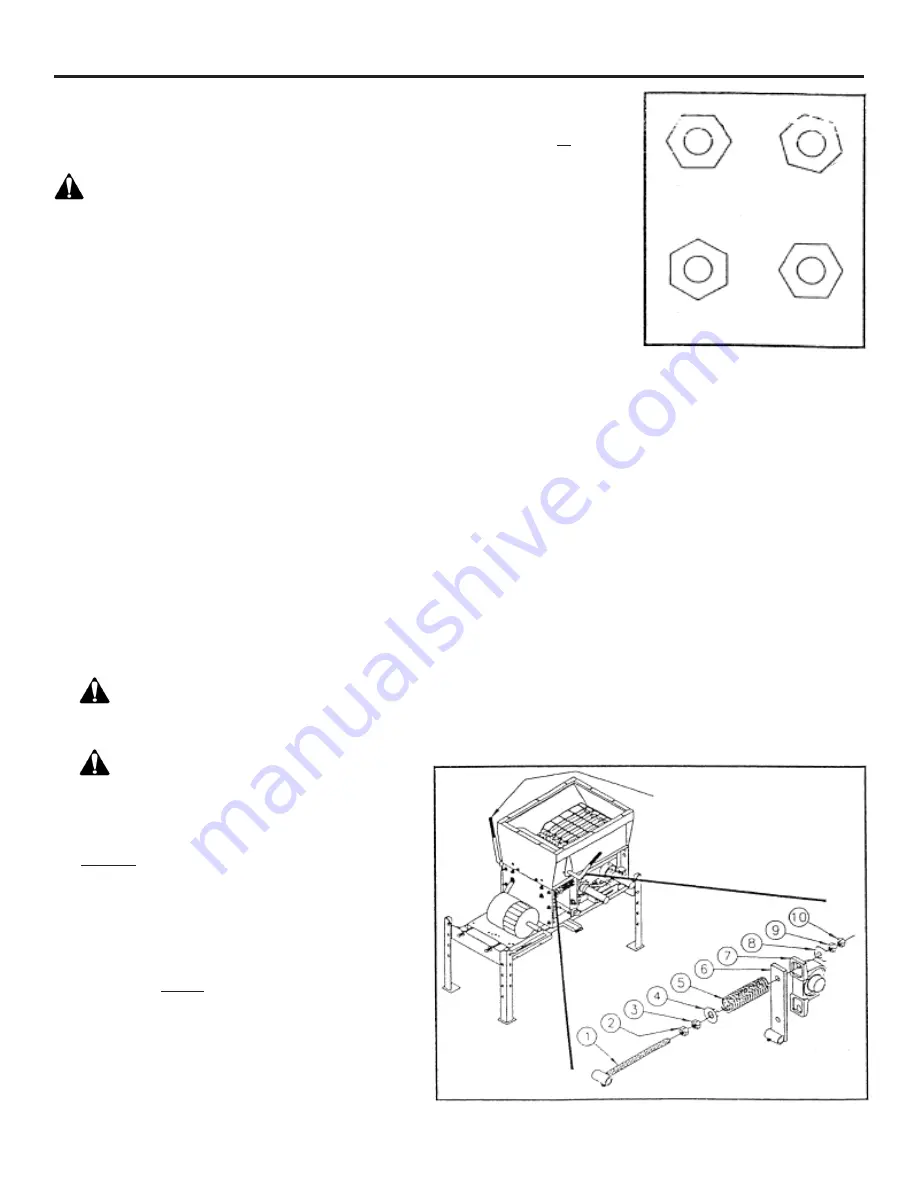
Page 9 of 26
7/9/19
6 Once the roll teeth
touch, turn the
nuts (9) IN about
1/4 to 1/2 flat on
the nut. (See
Figure 7).
NOTE: There are
six flat sides on
each nut. Turning
one full flat means
turning the nut so
that the flats
advance one
position.
7 Hold the nuts (9) in
place and tighten the jam nuts (10) on both sides of
the mill. Recheck that the rolls do not touch by
repeating step 5.
8 Move the roll spacing adjustment handle 50 each way
from center and check to assure the rolls are not
touching. Readjust if necessary. Be sure to tighten jam
nuts (10) when finished.
9 If adjustments were made, measure the length of the
springs (5). They should be 4 1/2” long ±1/8”. If
spring adjustment is needed, loosen the jam nut
(2) on the spring side and move spring nut (3) until
the correct spring length is established. Once
adjusted, tighten the jam nut (2) to hold setting.
10 Make a final check of the rolls for parallel and roll
gap. You may need to use a feeler gauge for 8 cut and
finer rolls. Reinstall the drive belt and shields. Be sure
to remove any tools from the machine before
restarting.
Figure 7
Figure 8
REALIGNING ROLLS
REALIGNING ROLLS - If the rolls ever become out of
alignment (more gap on one end of the roll pair than
the other) they must be realigned to maintain feed
consistency and prolong the life of the rolls. To accomplish
this, follow the instructions below.
DANGER: Before attempting to service your
roller mill be sure to follow the SAFETY SHUTDOWN
PROCEDURE on page 2.
1
Remove the drive belt from all the pulleys and lay it
aside. Loosen the jam nut (item 10) on one of the
sides of the mill. It may be necessary to loosen and
adjust both sides to acquire the correct settings. This
will be determined by how far out of parallel the rolls
are.
2 Adjust the other nut (9) on the same side, until the
rolls are parallel. To check for roll spacing, a strip
of metal banding works well but any strip of metal
approximately 1/32” thick will also work. Slide the
strip between the rolls and verify the roll spacing is
the same along their entire length. Check the spacing
3 or 4 times with the rolls at various rotated positions
to assure the rolls are as close to parallel as possible.
NOTE: Rolls will vary a few thousandths of an inch
in diameter along their length, be sure to check for
the tightest gap.
3 With the rolls parallel you can now set the roll
spacing. Place the roll spacing adjustment handle
straight up with the indicator straight down. This will
place the rolls at their closest possible setting.
4
WARNING: Be careful not to get your hands
between the rolls or between the rolls and the basic
channel.
WARNING: Do not power the mill with the
motor. This creates a personal danger to you and
may cause damage to the rolls if they are touching.
5 By hand, spin the rolls in the same direction
(clockwise) at different speeds. Strike the idler roll
shaft at the bearing, towards the drive roll, with a
rubber mallet to ensure that the idler bearing
mount (6) is free to allow the rolls to be at their
closest position. With the rolls spinning freely at
different speeds, turn the nuts (9) on both sides of
the mill out evenly until you hear the roll teeth
touch. They will make a ticking sound that should
be easily heard. This is to ensure that the rolls do
not move closer together with the vibration of the
mill. Some additional adjustment may be needed
at this time.
292-1329 5/94
ROLL SPACING
ADJUSTMENT
ORIGINAL
1/2 FLAT
1/4 FLAT
1 FLAT
1
1
1
1
2
2
2
2
3
3
3
3
4
4
4
4
5
5
5
5
6
6
6
6