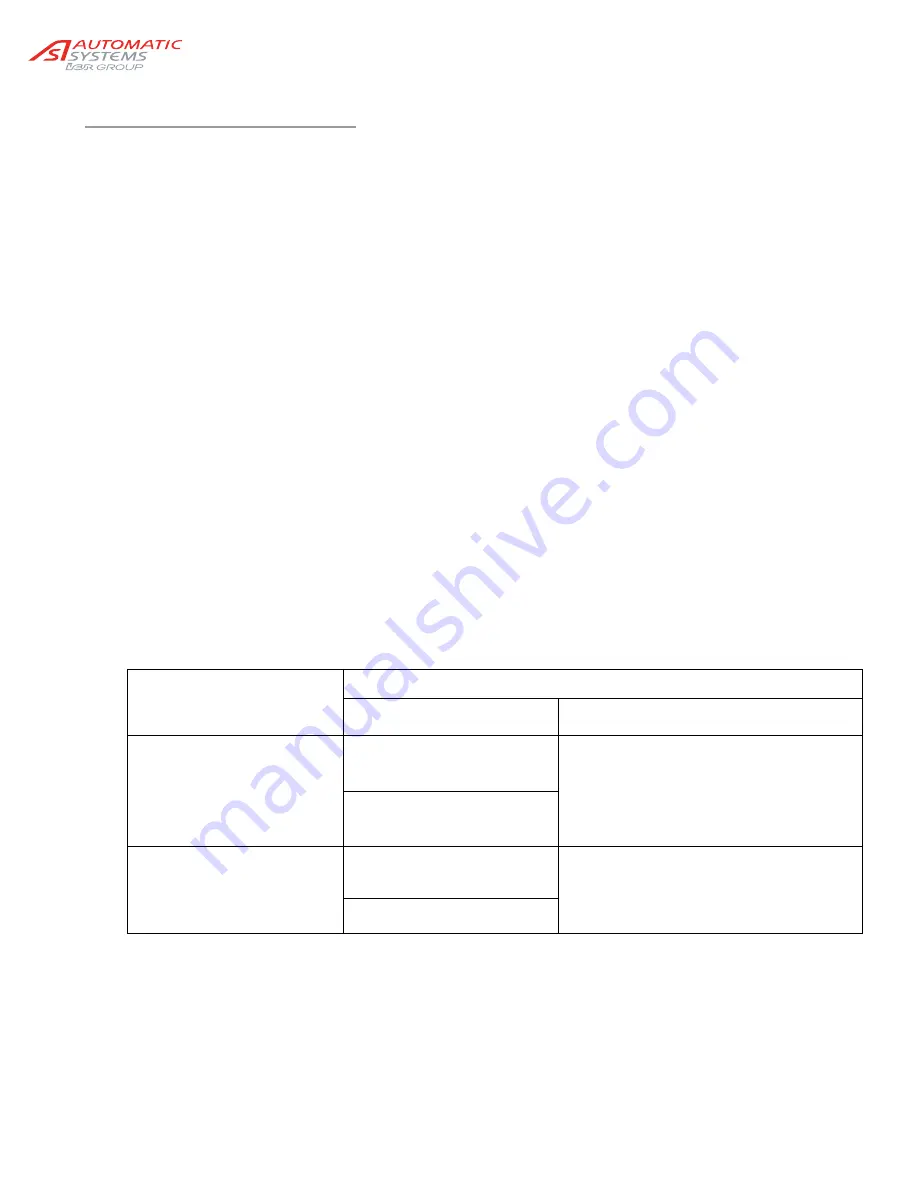
p 7/58
Technical Manual NAM-BL4x-MT-EN-C
The information in this document is the property of Automatic Systems and is confidential. The consignee withholds from using it for anything other than the use of the products or the execution of the
project to which they belong and withholds from communicating it to third parties without prior written agreement from Automatic Systems. Document subject to change without prior notice.
2.2. Operating principle
The indicators in this chapter refer to the illustrations in Ch. 2.1.
The opening of the arm (18) is controlled by the user (through a lockable switch, a push-button, a radio
transmitter), presence detector loops buried under the road, or through an outside unit.
Closing is controlled in the same way, or automatically after a time delay.
The motion generated by the
gear motor
(9) is transmitted to the arm by means of pinion and sector gears
(15 + 11).
The speed of the arm movement, controlled by the
variable speed controller
(17), can be adjusted for both
opening and closing. The movement parameters are adjusted in the factory in order to offer brisk acceleration
and gentle deceleration at the end of the movement.
The 2 inductive
position sensors
(7) indicate the extreme arm positions (open and closed) to the
control
board
(16). The latter coordinates the barrier’s activity: Management of movements, options, processing of
incoming and outgoing information, etc (see Ch. 3. ). This information can, however, be transferred and
processed by an external terminal (not supplied by Automatic Systems).
There are one to six preloaded
balancing springs
(12) to help the motor open and close the barrier.
For barrier models
with the automatic lifting option
during power cuts, the preloading of springs is
increased in order for the latter to ensure the lifting of the arm in the event of power outages.
In normal operation condition a
mechanical locking system
holds the arm in its closed positions. Also, the
variable speed controller compensate for any effort made to move the barrier manually when the arm is in the
open, closed or stopped position.
In order to increase protection against vandalism (forcing the arm), the
mechanical locking system
can be
modified to act in power outage situation and also to lock the open position
(see Ch 2.3. ).
The following table summarises the various possible combinations:
Locking situation
Locking of the arm (optional)
Locked position
Type of lock
(see note Ch. 2.3. )
Locking in power outage and
operation.
(For barrier without automatic lifting
of the arm)
Locking of arm in open position
(option)
Lock NC,
- Receives power during the movement of the arm in
order to release it.
- Lock released only during motion
Locking of arm in the closed position
(option)
Locking in operation only
(For barrier with automatic lifting of
the arm)
Locking of arm in open position
(option)
Lock NO
- Receives power when the arm is closed or open in
order to lock it.
- Lock released in power outage and during motion.
Locking of arm in the closed position
(standard)
NC: Normally Closed
= Closed in standby status (not turned on).
NO: Normally Open
= Open in standby status (not turned on).
Note: The open and close position lock can only work in matching locking situation.