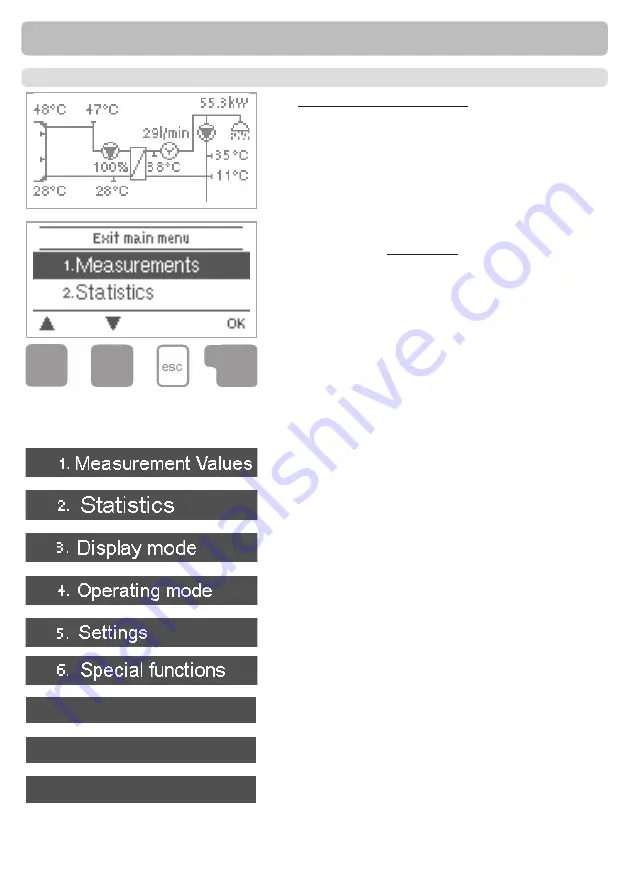
14
E.2. - Menu sequence and menu structure
The graphics or overview mode appears when no
key has been press for 2 minutes, or when the main
menu is exited by pressing “esc“.
Pressing a key in graphics or overview mode takes
you directly to the main menu. The following menu
items are then available for selection there:
Current temperature values with explanations
Function control of the system with operating hours,
etc.
Select graphics mode or overview mode
Automatic mode, manual mode or switch unit off
Set parameters needed for normal operation
Program selection, clock, etc.
Functions to prevent damage to system and user.
Against unintentional setting changes at critical
points
For diagnosis in the event of an error
Operation
7. Protective functions
8. Menu block
9. Service Values