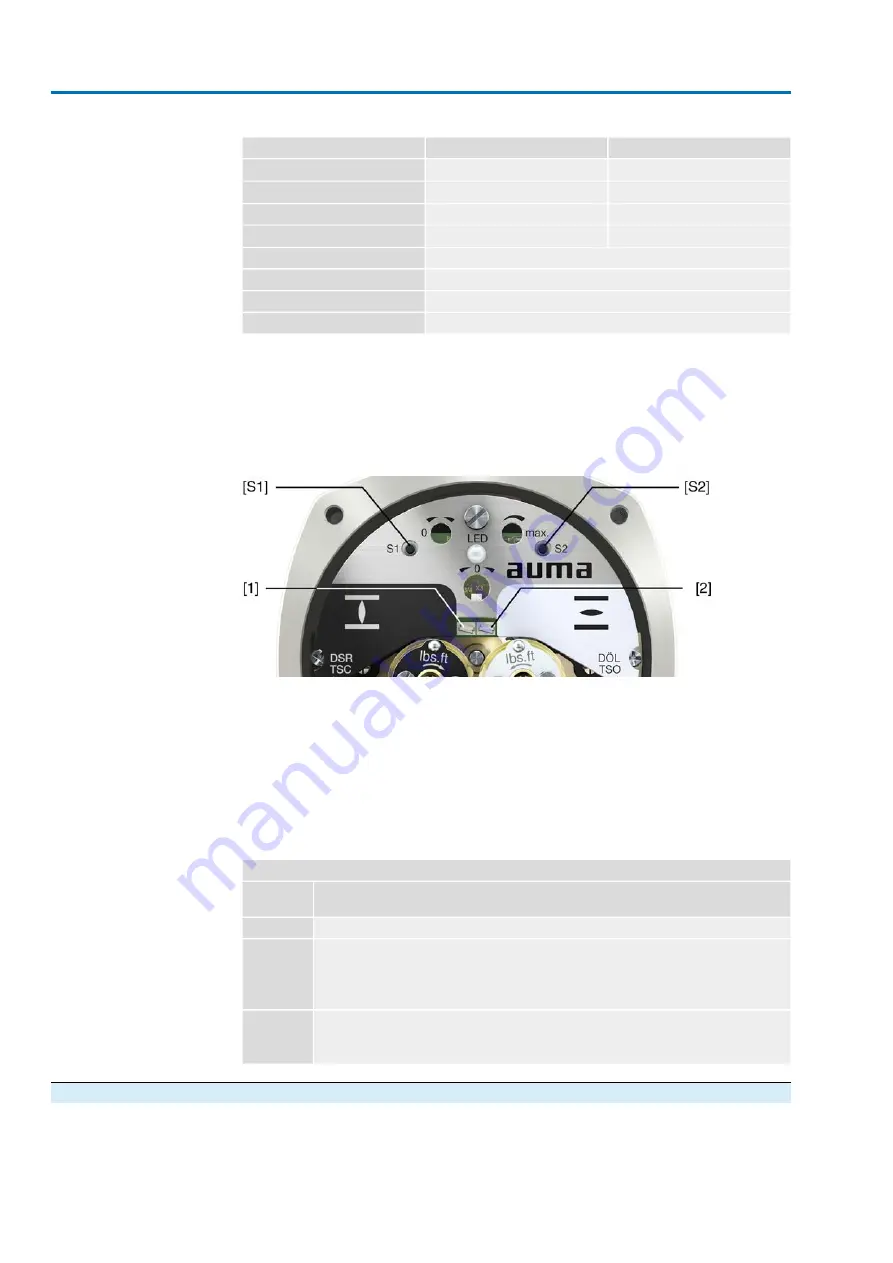
Technical data
Table 18: EWG 01.1
2-wire system
3-wire and 4-wire systems
Data
4 – 20 mA
0 – 20 mA, 4 – 20 mA
Output current I
a
24 V DC (18 – 32 V)
24 V DC (18 – 32 V)
Power supply U
V
1)
20 mA
LED off = 26 mA, LED on = 27 mA
Max. current consumption
(U
V
– 12 V)/20 mA
600
Ω
Max. load R
B
0.1 %
Impact of power supply
0.1 %
Load influence
< 0.1 ‰/K
Temperature impact
–76 °F to 176 °F (–60 °C to +80 °C)
Ambient temperature
2)
Power supply possible via: AC, AM controls or external power supply
1)
Depending on temperature range of the actuator: Refer to name tag
2)
Setting components
The EWG is housed in the actuator switch compartment. The switch compartment
must be opened to perform any settings. Refer to <Switch compartment: open>.
All settings are made via the two push buttons [S1] and [S2].
Figure 50: View on control unit when switch compartment is open
[S1]
Push button: Set 0/4 mA
[S2]
Push button: Set 20 mA
LED Optical aid for setting
[1]
Measuring point (+) 0/4 – 20 mA
[2]
Measuring point (–) 0/4 – 20 mA
The output current (measuring range 0 – 20 mA) can be checked at measuring points
[1] and [2].
Table 19:
Short overview on push button functions
Function
Push but-
tons
→
press simultaneously for 5 s: Activate setting mode
[S1] + [S2]
→
press in setting mode for 3 s: Set 4 mA
→
press in setting mode for 6 s: Set 0 mA
→
press in operation for 3 s: Switch on/off LED end position signaling.
→
touch in end position: Reduce current value by 0.02 mA
[S1]
→
press in setting mode for 3 s: Set 20 mA
→
press in operation for 3 s: Switch on/off LED end position signaling.
→
touch in end position: Increase current value by 0.02 mA
[S2]
10.3.1.
Measuring range: set
For measuring range setting, voltage must be applied at the position transmitter.
For output current verification, connect a test device for 0 – 20 mA to measurement
points (+/–) (for 2-wire systems, connecting a test device is required).
50
SAEx 25.1 – SAEx 35.1 / SAREx 25.1 – SAREx 30.1
Commissioning (setting optional equipment)
NORM (without controls)