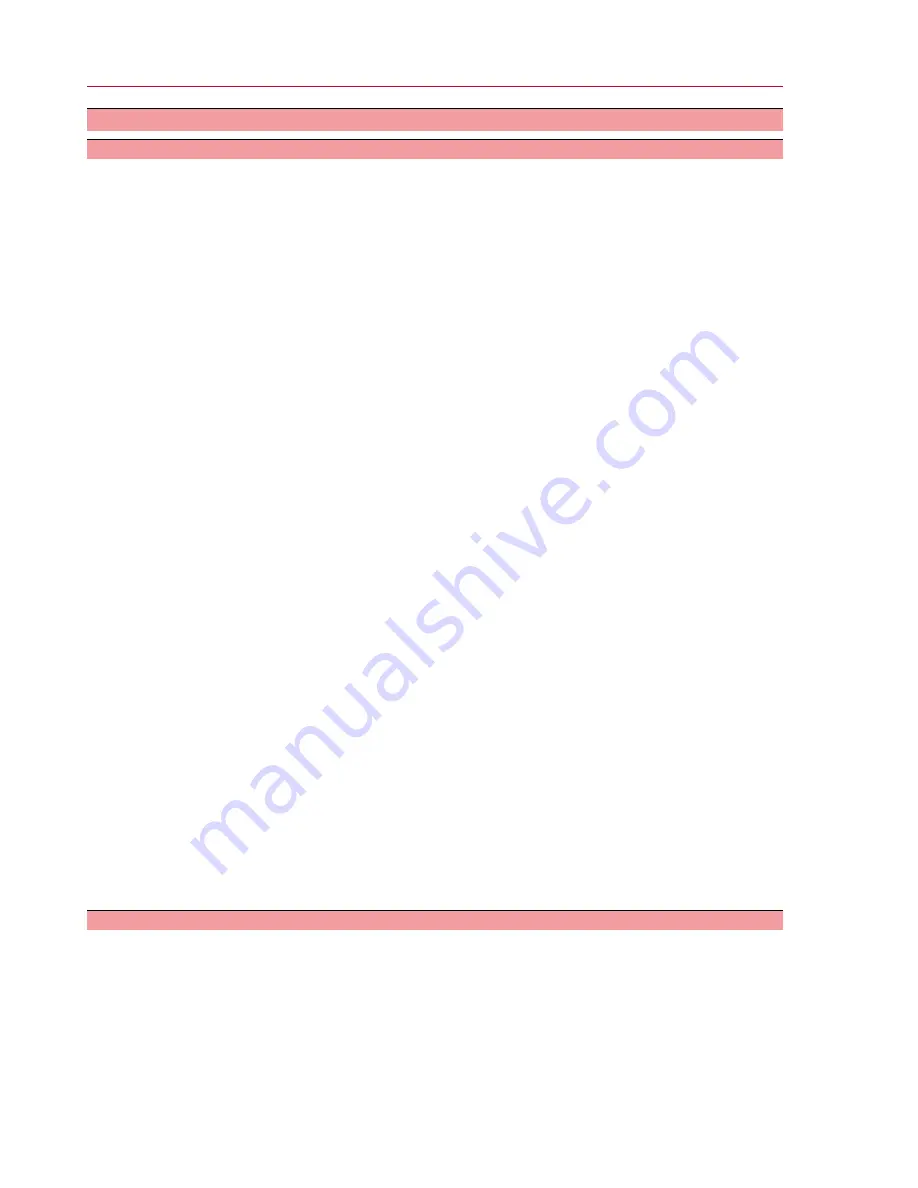
1.
Safety instructions
1.1.
Basic information on safety
Standards/directives
AUMA products are designed and manufactured in compliance with recognised
standards and directives. This is certified in a Declaration of Incorporation and an
EC Declaration of Conformity.
The end user or the contractor must ensure that all legal requirements, directives,
guidelines, national regulations and recommendations with respect to assembly,
electrical connection, commissioning and operation are met at the place of installation.
Safety instructions/warn-
ings
All personnel working with this device must be familiar with the safety and warning
instructions in this manual and observe the instructions given. Safety instructions
and warning signs on the device must be observed to avoid personal injury or property
damage.
Qualification of staff
Assembly, electrical connection, commissioning, operation, and maintenance must
be carried out exclusively by suitably qualified personnel having been authorised by
the end user or contractor of the plant only.
Prior to working on this product, the staff must have thoroughly read and understood
these instructions and, furthermore, know and observe officially recognised rules
regarding occupational health and safety.
Commissioning
Prior to commissioning, it is important to check that all settings meet the requirements
of the application. Incorrect settings might present a danger to the application, e.g.
cause damage to the valve or the installation. The manufacturer will not be held
liable for any consequential damage. Such risk lies entirely with the user.
Operation
Prerequisites for safe and smooth operation:
●
Correct transport, proper storage, mounting and installation, as well as careful
commissioning.
●
Only operate the device if it is in perfect condition while observing these instruc-
tions.
●
Immediately report any faults and damage and allow for corrective measures.
●
Observe recognised rules for occupational health and safety.
●
Observe the national regulations.
●
During operation, the housing warms up and surface temperatures > 60 °C may
occur. To prevent possible burns, we recommend checking the surface temper-
ature using an appropriate thermometer and wearing protective gloves, if re-
quired, prior to working on the device.
Protective measures
The end user or the contractor are responsible for implementing required protective
measures on site, such as enclosures, barriers, or personal protective equipment
for the staff.
Maintenance
To ensure safe device operation, the maintenance instructions included in this manual
must be observed.
Any device modification requires prior consent of the manufacturer.
1.2.
Range of application
AUMA part-turn actuators are designed for the operation of industrial valves, e.g.
butterfly valves and ball valves.
Other applications require explicit (written) confirmation by the manufacturer.
The following applications are not permitted, e.g.:
●
Industrial trucks according to EN ISO 3691
●
Lifting appliances according to EN 14502
●
Passenger lifts according to DIN 15306 and 15309
●
Service lifts according to EN 81-1/A1
4
SQ 05.2 – SQ 14.2/SQR 05.2 – SQR 14.2
Safety instructions