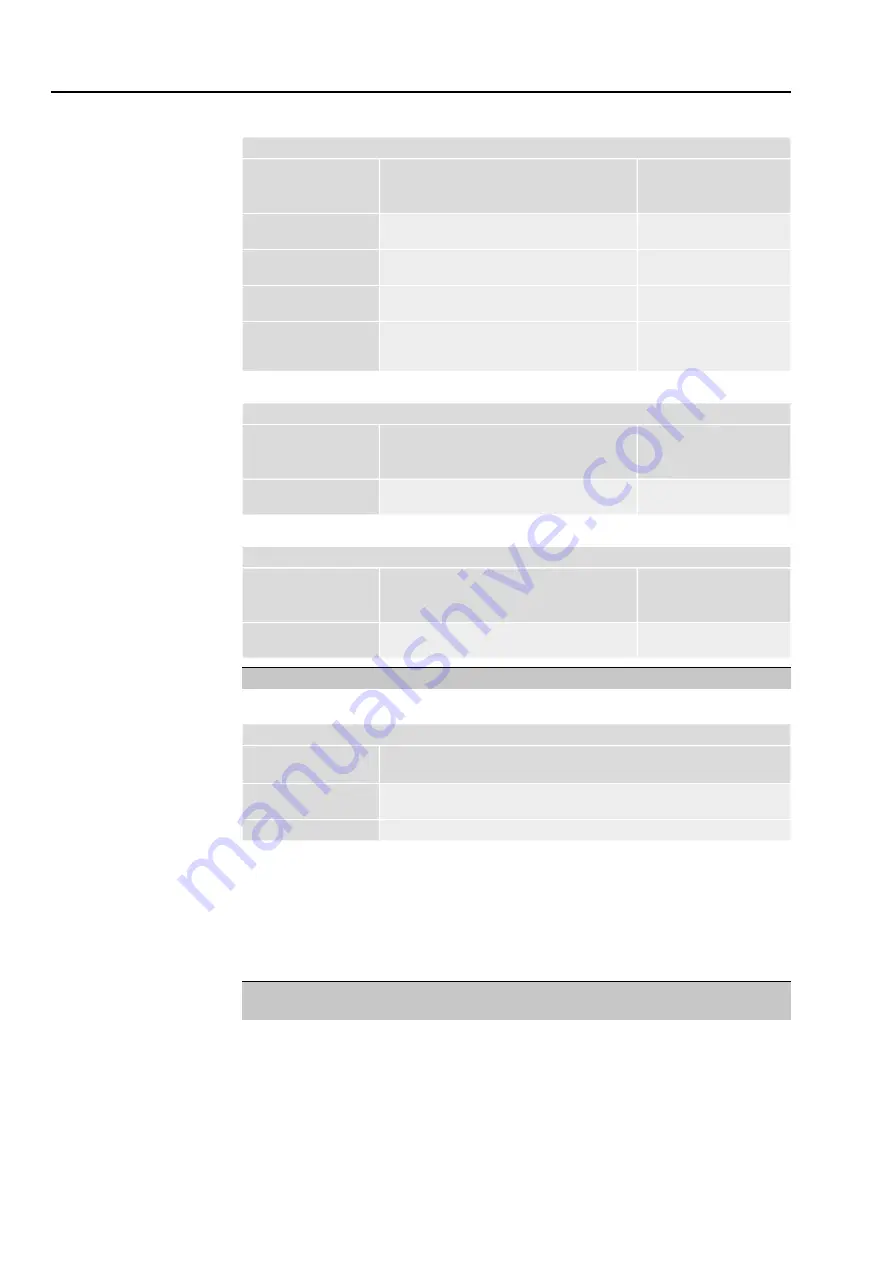
Table 4:
For actuators with electromechanical control unit:
Configuration
Type of seating
Standard controls
Short description
Configuration
SIL seating type
Freely selectable
No seating by limit or torque switches during
safety operation
1: No seating
Torque seating
Safety operation is stopped if both limit and
torque switches trip simultaneously
2: Forced torque seating
in end position
Limit seating
Safety operation is stopped by limit switch trip-
ping
3: Forced limit seating in
end position
Limit seating
Safety operation is stopped by tripping the limit
switches and/or the torque switches (overload
protection).
4: Limit seating with
overload protection
Table 5:
for actuators with electronic control unit MWG
Configuration
Type of seating
Standard controls
Short description
Configuration
SIL seating type
Freely selectable
No seating by limit or torque switches during
safety operation
1: No seating
Table 6:
for actuators with electronic control unit MWG including limit switches
Configuration
Type of seating
Standard controls
Short description
Configuration
SIL seating type
Limit seating
Safety operation is stopped by limit switch trip-
ping
3: Forced limit seating in
end position
Configuration options for motor protection assessment
Table 7:
Configuration options for motor protection assessment
Short description
Configuration
SIL motor protection
Tripping of the motor protection (thermal fault) stops or prevents safety oper-
ation
Active
Motor protection has no impact on the safety operation
Inactive
Information
“SIL motor protection” = “inactive” configuration is only set if explicitly required. The
version does not meet the Ex approval requirements.
Information
If limit and/or torque switches for the end positions are available, precise setting is
imperative to ensure correct function of the “Safe end position feedback” or the “ESD
function”. For setting details related to the respective switches, please refer to oper-
ation instructions.
Configuration of “reaction monitoring” diagnostics and “Partial Valve Stroke
Test (PVST)”
Depending on the type of diagnostics specified, the reaction monitoring via blinker
transmitter or Partial Valve Stroke Test configurations have to be checked and
adapted, if required.
For detailed configuration options as well as detailed information on the Partial Valve
Stroke Test (PVST), refer to Manual (Operation and setting) AUMATIC AC 01.2.
Please note that reaction monitoring may only be executed via the blinker
transmitter/SIL fault signal and not via the reaction monitoring function of the AC .2
firmware.
10
Part-turn actuators
Architecture, configuration and applications
with AC 01.2-SIL/ACExC 01.2-SIL