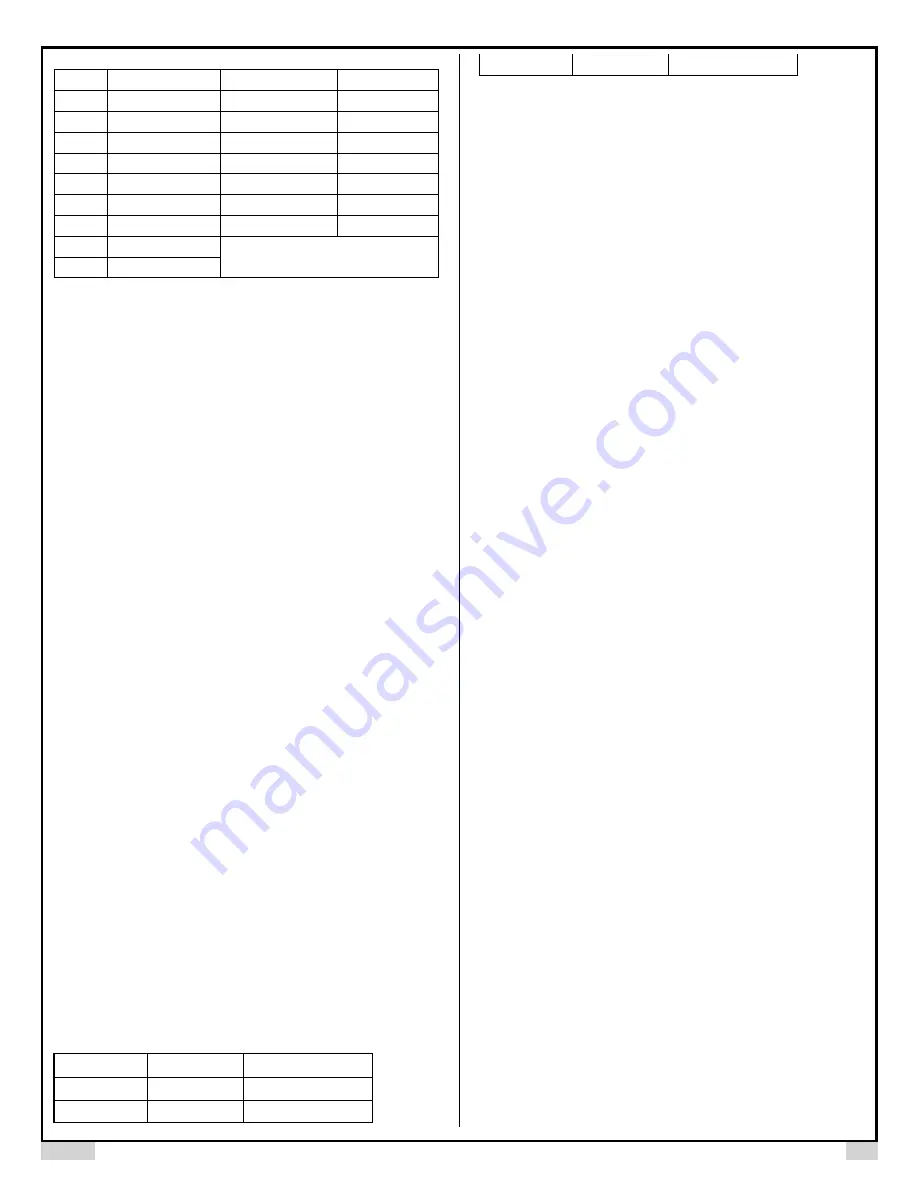
AUBER INSTRUMENTS
WWW.AUBERINS.COM
2021.01
P5/6
Table 3. Code for Sn and its range.
Sn Code
Input Device
Display Range (
˚
C)
Display Range (
˚
F)
Cu50
Cu50 (RTD)
-49 ~160
-56 ~ 302
Pt
Pt100 (RTD)
-199 ~610
-198 ~1111
K
K (thermocouple)
-30 ~ 1300
-20 ~ 2370
E
E (thermocouple)
-29 ~ 719
-20 ~ 1292
J
J (thermocouple)
-29 ~ 905
-20 ~ 1651
T
T (thermocouple)
-198 ~ 400
-190 ~ 750
S
S (thermocouple)
-29 ~ 1619
-20 ~ 2912
0 - 5
0 ~5V (0 ~10mA)
Not available for this model.
1 - 5
1 ~5V (4 ~20mA)
4.6 Decimal point setting
“
dP
”
In case of thermocouple or RTD input, dP is used to define temperature display
resolution.
When dP = 0, temperature display resolution is 1º (C or F).
When dP = 1, temperature display resolution is 0.1º (C or F). The temperature
will be displayed at the resolution of 0.1º for input below 1000º and 1º for input
over 1000º (C or F).
4.7 Limiting the control range,
“
DIL
”
and
“
DIH
”
1) For temperature sensor input, the “DIL”
and “DIH”
define the set value range.
DIL is the low limit, and DIH is the high limit. Sometimes, you may want to limit
the temperature setting range so that the operator cannot set a very high
temperature by accident. For example, if you set the DIL = 100 and DIH = 130,
operator will only be able to set the temperature between 100 and 130.
2) For linear input devices,
“
DIL
”
and
“
DIH
”
are used to define the display span.
For example, if the input is 0 - 5V. DIL is the value to be displayed at 0V and
DIH is the value at 5V.
4.8 Input offset
“
SC
”
SC is used to set an input offset to compensate the error produced by the
sensor or input signal itself. For example, if the controller displays 5ºC when
probe is in ice/water mixture, setting Pb = -5, will make the controller display
0ºC.
4.9 Output definition
“
OPA
”
This parameter should be kept at zero for this model.
4.10 Heating, and Cooling Mode Selection
“
COOL
”
When COOL = ON, the controller is set for cooling control.
When COOL = OFF, the controller is set for heating control.
4.11 Temperature Unit Selection, Celsius or Fahrenheit,
“
C, F
”
This parameter sets temperature units, C for Celsius, F for Fahrenheit. When it
is for current or voltage input, this parameter is voided.
4.12 Output range high limit
“
OUTH
”
OUTH allows you set the output range high limit.
OUTH can be used when you have an overpowered heater to control a small
subject. For example, if you set the OUTH = 50, the 5000W heater will be used
as 2500W heater (50%) even when the PID wants to send 100% output.
4.13 Lock up the settings, parameter
“
LOCK
”
To prevent the operator from changing the settings by accident, you can lock
the parameter settings after initial setup. Table 4 shows the privileges
associated with each lock code.
Table 4. LOCK parameter.
LOCK value
SV Adjustment
Other Parameters
0
Yes
Yes
1
Yes
Locked
2 and up to 50
No
Locked
Note: to limit the control temperature range instead of completely locking it,
please refer to section 4.7.
4.14 Set Time for Timer
“
TE1
”
and “TE2”
“
TE1
”
is for setting value for the timer. Press
▼
for 3 seconds and change the
value directly.
“TE2”
is for setting time of timer 2, it is only valid for dual timer working mode.
4.15 Time Unit and Timer Counting Mode
“
UPT
”
UPT = 0, timer counting down in seconds.
UPT = 1, timer counting down in minutes.
UPT = 2, timer counting up in seconds.
UPT = 3, timer counting up in minutes.
4.16 Timer control mode
“
INT
”
*
INT = 0.
The timer is disabled.
The controller functions as a regular dual
display controller. The lower display shows the set temperature instead of time.
INT = 1. The timer starts after the temperature reaches set point. When set time
reaches, controller’s output stops and timer relay
pulls in (turns on). It can be
connected to a buzzer to warn the operator.
INT = 2. The timer starts after the temperature reaches set point. When set time
reached, relay pulls in. The controller’s output will continue to be on.
INT = 3. The timer starts after the temperature reaches set point. When set time
reaches, controller’s output stops. Relay pulls in when timer starts and drops
out when it reaches the set time.
INT = 4. Timer function is independent of temperature controller. After powered
up (or reset), timer starts. The relay will pull in (close) when it reaches the set
time.
INT = 5. Timer function is independent of temperature controller. After powered
up (or reset), timer starts and the relay pulls in (close). It will drop out (open)
when it reaches the set time.
INT = 6. Timer function is independent of temperature controller. After powered
up (or reset), the relay drops out (open) for preset time TE1, then pulls in for
preset time TE2. This process cycles (dual timer cycling mode).
INT = 7. Timer function is independent of temperature controller. After powered
up (or reset), the relay drops out (open) for preset time TE1, then pulls in for
preset time TE2. The relay will remain drop out (open) until reset. After reset,
the relay will keep open for preset time TE1 then pulls in for preset time TE2
again (dual timer no cycling mode).
INT = 8. Timer function is independent of temperature controller. After powered
up (or reset), the relay pulls in for preset time TE1 then drops out (open) for
preset time TE2. This process cycles (dual timer cycling mode).
Note
*:
i). When INT value is greater than 0, timer is enabled. The bottom of the display
is for time. In order to let the timer controls the Alarm 1 (AL1), ALP1 should be
set to 0.
ii). Terminal 11 and 12 must be jumped together to enable the timer. Timer can
be started either at powering up of the controller if terminal 11 and 12 are
shorted together, or at shorting terminal 11 and 12 if they are not shorted
together.
iii) While the timer is running, it can be reset by pressing a reset switch (a
normally closed momentary switch) that is connected between terminal 11 and
12.
iv) When INT is set to 1, 2 or 3, after reset, timer starts counting again if
temperature reaches SV. If the temperature is lower than SV in heating mode
(or higher than
SV in cooling mode), timer won’
t restart until temperature
reaches SV again.