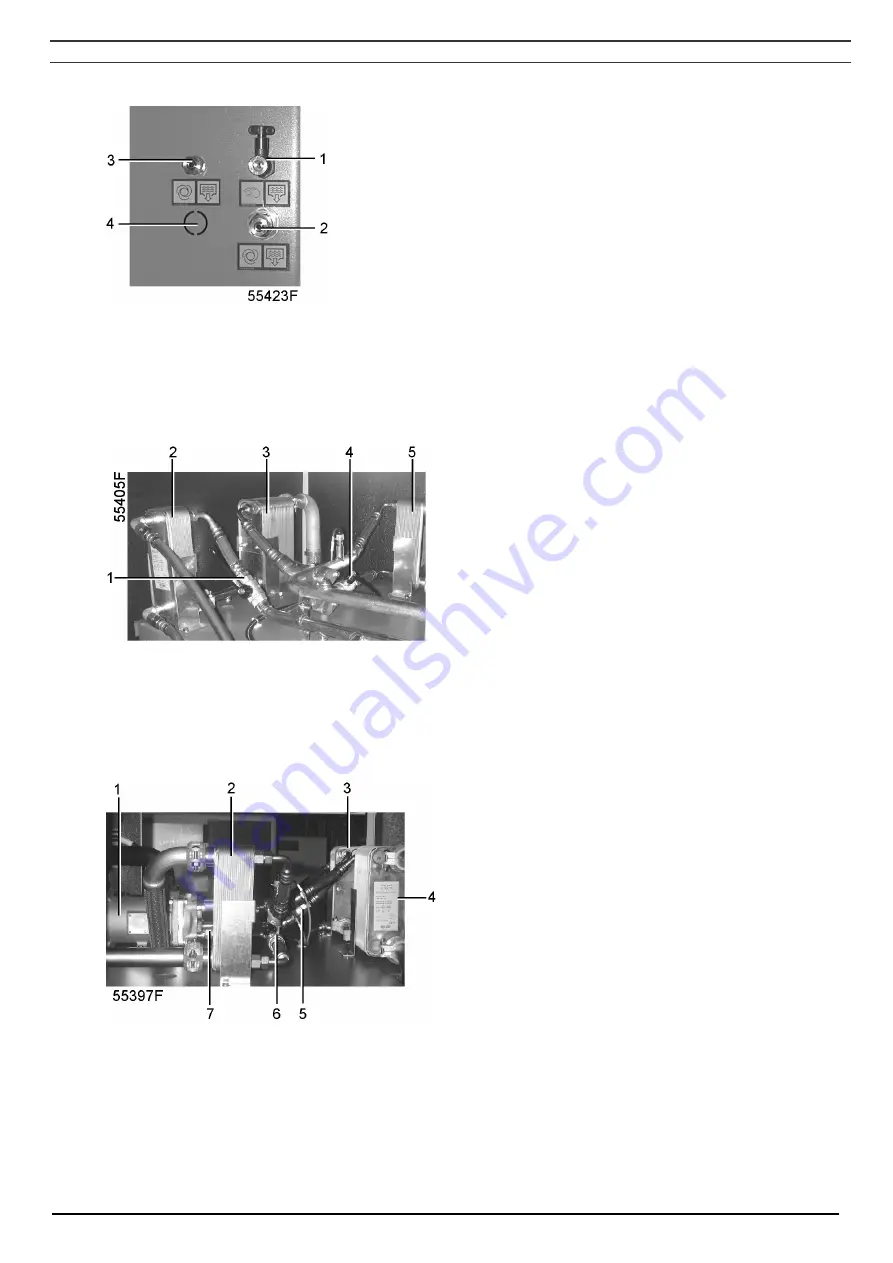
Instruction book
2920 1472 03
49
1
Manual condensate drain, aftercooler
2
Electronic condensate drain, intercooler
3
Automatic condensate drain, aftercooler
4
Prepared for electronic drain (only for
IMD)
Fig. 3.5 Condensate drains
1
Water flow regulating valve, oil cooler
and intercooler
2 Oil
cooler
3 Intercooler
4
Water flow regulating valve, aftercooler
5 Aftercooler
Fig. 3.6 Water system on ZR compressors
1 Regeneration
cooler
2 Aftercooler
3 Oil
cooler
4 Intercooler
5
Regulating valve for the oil cooler and
the intercooler
6
Regulating valve for the aftercooler
7
Regulating valve for the regeneration
cooler
Fig. 3.7 Water system on ZR with IMD