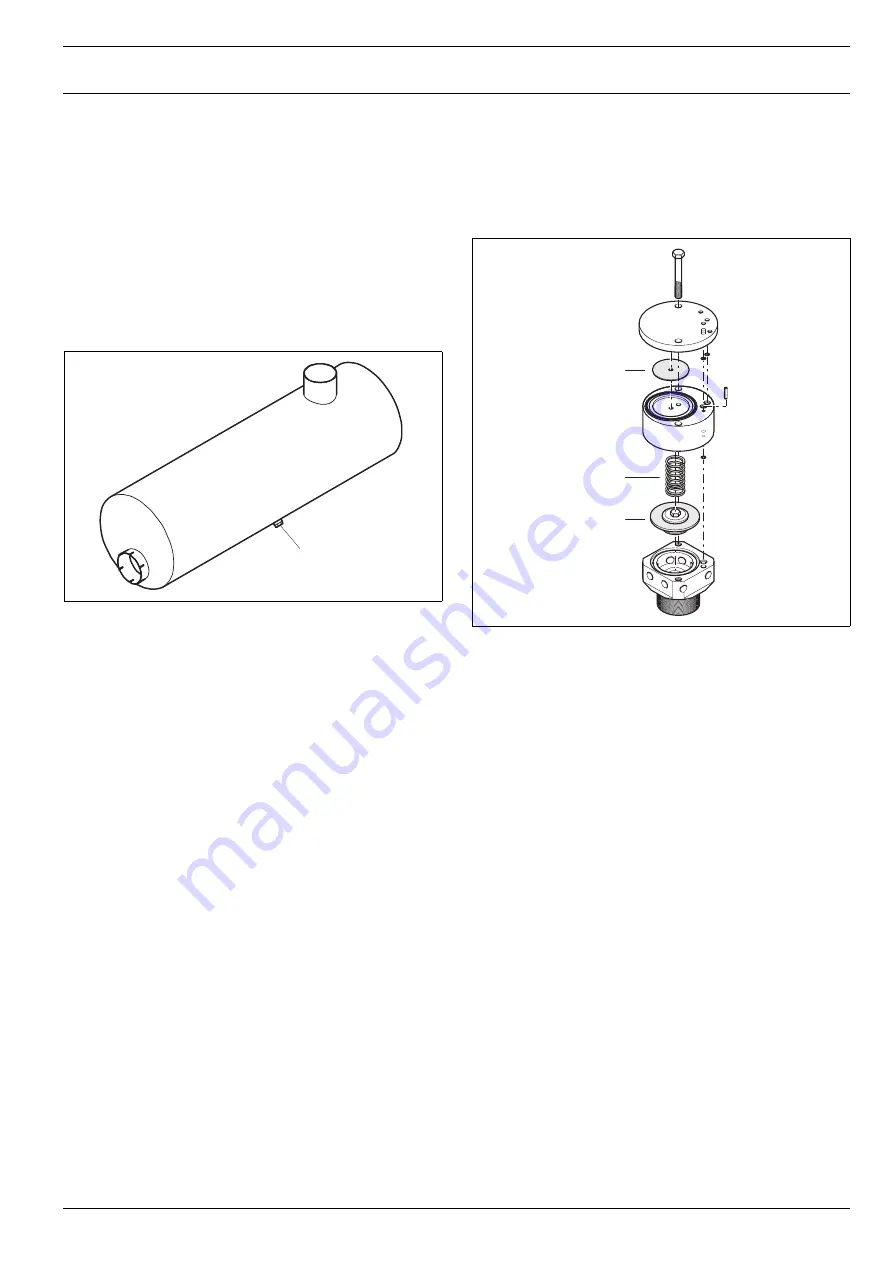
Instruction manual
49
5.14 Caterpillar air shut-off valve
The air shut-off valve, mounted on the engine, is part of the refinery
equipment. This valve prevents combustion air to enter the engine.
When an overspeed is detected, the engine will shutdown
(emergency stop) and the air shut-off valve will close.
To reset the air shut-off valve, pull the handle of the valve up until
a click is heared.
5.15 Integrated spark arrestors
Stop the unit and allow the exhaust system to cool. Remove the
plug (1) of the spark arrestor. Start up the unit to blow out collected
particles. Stop the unit and reinstall the plug.
The water separator in the back of the unit filters water condensate
out of the compressed air, before the air is discharged through the
outlet valves.
Water condensate from the water separator is drained through a
nipple in the bottom of the frame. Connect a drain hose to the nipple
and make sure that the condensate is properly disposed of.
Service the filter of the water separator every 500 hours.
The blow-off valve, fitted on the MP air inlet pipe, is opened to
release air when the air inlet throttle valve is closed; it closes when
the throttle valve is opened.
Replace the membrane (1), the diaphragm valve assembly (3), the
spring (2) and the o-rings every 2000 hours.
1
1
2
3
Summary of Contents for PTS 916 Cd
Page 1: ...Instruction Manual for Portable Compressors PTS 916 Cd ...
Page 2: ......
Page 57: ...Preliminary 57 Circuit diagrams ...
Page 72: ......
Page 73: ......
Page 74: ...Printed in Belgium 07 2007 Preliminary www atlascopco com ...