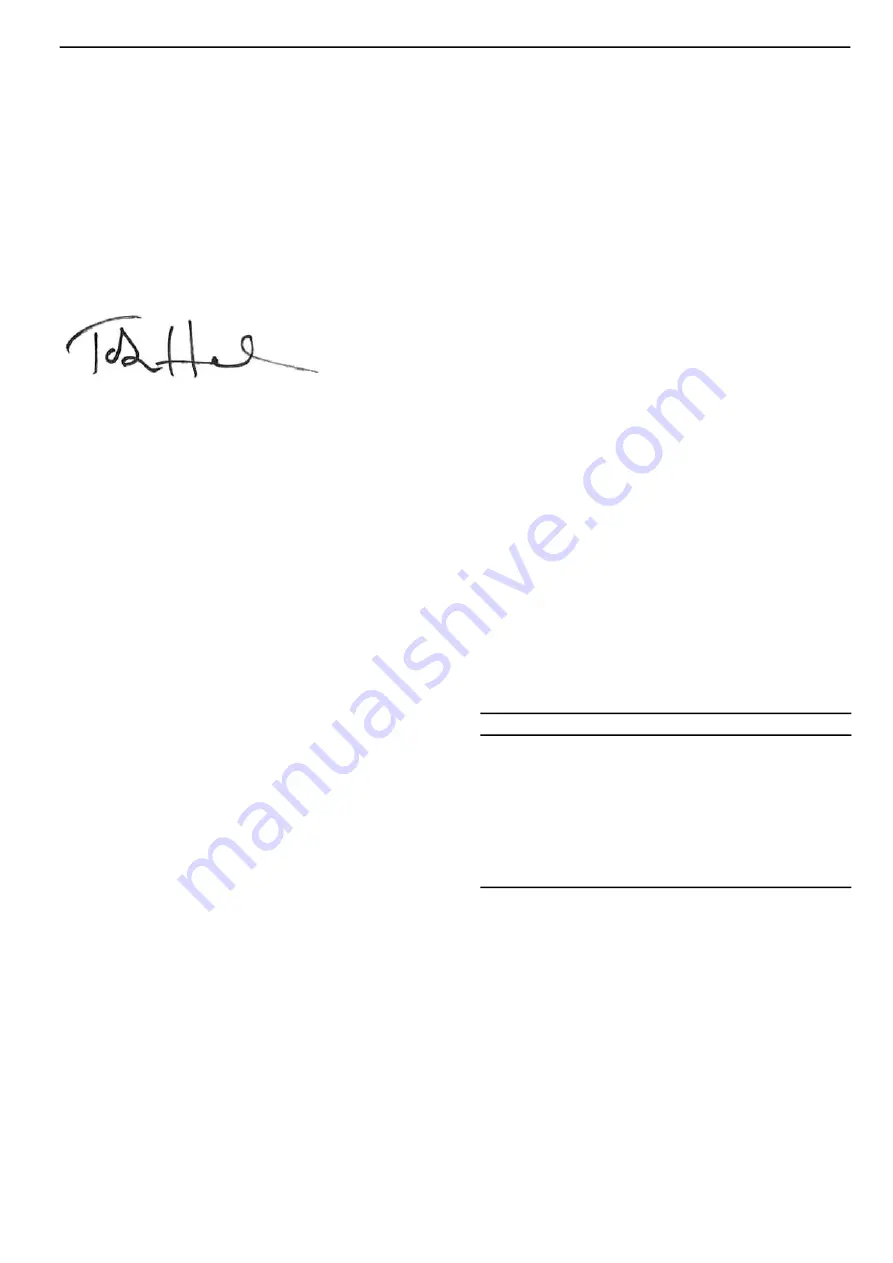
page) is in conformity with the following Direct-
ive(s):
2006/42/EC
Harmonised standards applied:
ISO 11148-4
Technical file available from:
Quality Manager, Atlas Copco Industrial Technique,
Stockholm, Sweden
Stockholm, 1 July 2013
Tobias Hahn, Managing Director
Signature of issuer
Installation
Air quality
• For optimum performance and maximum machine
life we recommend the use of compressed air with
a maximum dew point of +10°C. We also recom-
mend the installation of an Atlas Copco refrigera-
tion-type air dryer.
• Use a separate air filter of type Atlas Copco FIL.
This filter removes solid particles larger than 15
microns and also removes more than 90 % of li-
quid water. The filter must be installed as close
as possible to the machine/equipment and prior
to any other air preparation unit such as REG or
DIM (please see Air Line Accessories in our main
catalogue). Blow out the hose before connecting.
Models which need air lubrication:
• The compressed air must contain a small quantity
of oil.
We strongly recommend that you install an Atlas
Copco oil-fog lubricator (DIM). This should be
set according to air consumption by the air line
tool according to the following formula:
L
= Air consumption (litre/s).
(May be found in our sales literature).
D
= Number of drops per min (1 drop = 15 mm
3
)
L* 0.2 = D
this applies to the use of long work cycle air line
tools. A single point lubricator type Atlas Copco
Dosol can also be used for tools with short running
cycles.
Information about Dosol settings may be found
under Air Line Accessories in our main catalogue.
Lubrication-free models:
• In the case of lubrication-free tools it is up to the
customer to decide on the peripheral equipment
to be used. However, it is no disadvantage if the
compressed air contains a small quantity of oil
e.g. supplied from a fog lubricator (DIM) or Dosol
system. This does not apply to turbine tools, which
should be kept oil free.
Compressed air connection
• The machine is designed for a working pressure
of 6–7 bar = 600–700 kPa = 87–102 psi.
• Blow out the hose before connecting.
Maintenance
Maintenance
Lubricate the machine regularly with air tool oil.
If the machine is used every day, it should be
overhauled and cleaned once every six months.
The use of other than genuine Atlas Copco replace-
ment parts may result in decreased tool performance
and increased maintenance and may, at the option
of the company, invalidate all warranties.
Cleaning
At 100 hour operating intervals or earlier if operation
becomes sluggish or the machine shows sign of
sticking, flush through with paraffin or a similar
material. Immediately after flushing thoroughly oil
the machine with air tool oil.
Grease guide
Air lubrication
Grease
Brand
Energol E46
Energrease LS-EP2
BP
Arox EP46
Beacon EP2
Esso
Chopin 46
Rembrandt EP2
Q8
Almo Oil 525
Mobilegrease XHP 222
Mobil
Torcula 32
Alvania EP2
Shell
Aries 32
Multifak EP2
Texaco
BR2 Plus
Molycote
Useful information
C
Log in to Atlas Copco www.atlascopco.com
You can find information concerning our products,
accessories, spare parts and published matters on our
website.
Ergonomic guidelines
Consider your workstation as you read through this
list of general ergonomic guidelines and see if you
can identify areas for improvement in posture, com-
ponent placement, or work environment.
5
© Atlas Copco Industrial Technique AB - 9836 3979 00
Safety and operating instructions
EN
P2535-H