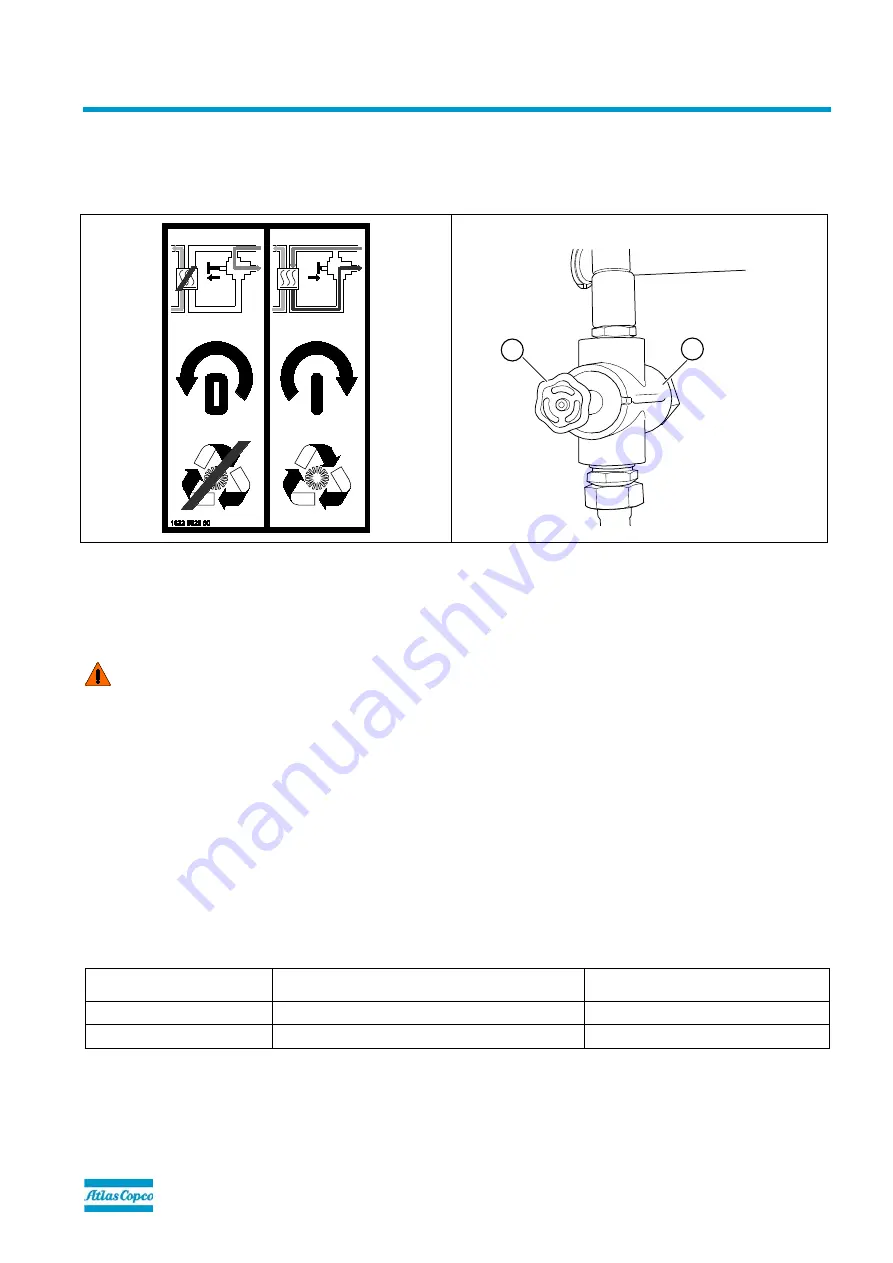
20/06/2011
PM 9845 0512 02
Page 21 of 36
7. Operation
7.1. Thermostatic bypass valve
Heat exchanger bypass valve (of ER unit) with lever
Figure 13: ER label
Figure 14: Thermostatic valve housing ER kit
The 1st bypass valve of the ER (Figure 14-7) is provided with a special lever (Figure 14-26). This lever controls the
operation of the energy recovery system.
As can be seen on the ER label (Figure 13), the ER unit is integrated in the oil circuit and recovers energy when the lever is
turned in fully clockwise.
When the lever is turned out fully counter clockwise, the ER unit is bypassed in the oil circuit and does not recover energy.
Always turn the lever (Figure 14-26) all the way in or out. Do not position it anywhere in between both ends.
Main oil cooler bypass valve of oil filter pipe
The 2nd bypass valve (Figure 2-14) starts closing the bypass line and opening the oil supply line from the main oil cooler
(Figure 2-23) at the lower limit of its temperature range; at the upper limit of its temperature range, the bypass line is
completely closed and all the oil flows through the main oil cooler.
On all compressors (fixed speed and VSD compressors), a thermostat with a higher temperature range (compared to the
standard thermostat) is required in the 2nd bypass valve of the oil filter pipe when using the compression heat as its source
for energy recovery.
Thermostatic valve instructions
The thermostatic valve of the compressor must always open at least 10°C later than the one in the ER unit to prevent
tripping of the valves. See table for actions:
Valve of Compressor
Action on Compressor
Action on ER unit
40 °C
Replace valve with 60 °C
Place valve 40 °C
60 °C
Replace valve with 75 °C
Place valve 60 °C
7
26
Summary of Contents for ER S-1
Page 1: ...Atlas Copco Energy Recovery Stand Alone Kit Instruction book ...
Page 2: ......
Page 34: ...20 06 2011 PM 9845 0512 02 Page 32 of 36 Figure 17 9845 0070 00 Figure 18 9845 0071 00 ...
Page 35: ...20 06 2011 PM 9845 0512 02 Page 33 of 36 Figure 19 9845 0124 00 Figure 20 9845 0125 00 ...
Page 39: ......
Page 40: ...PM 9845 0512 02 2011 06 Printed in Belgium www atlascopco com ...