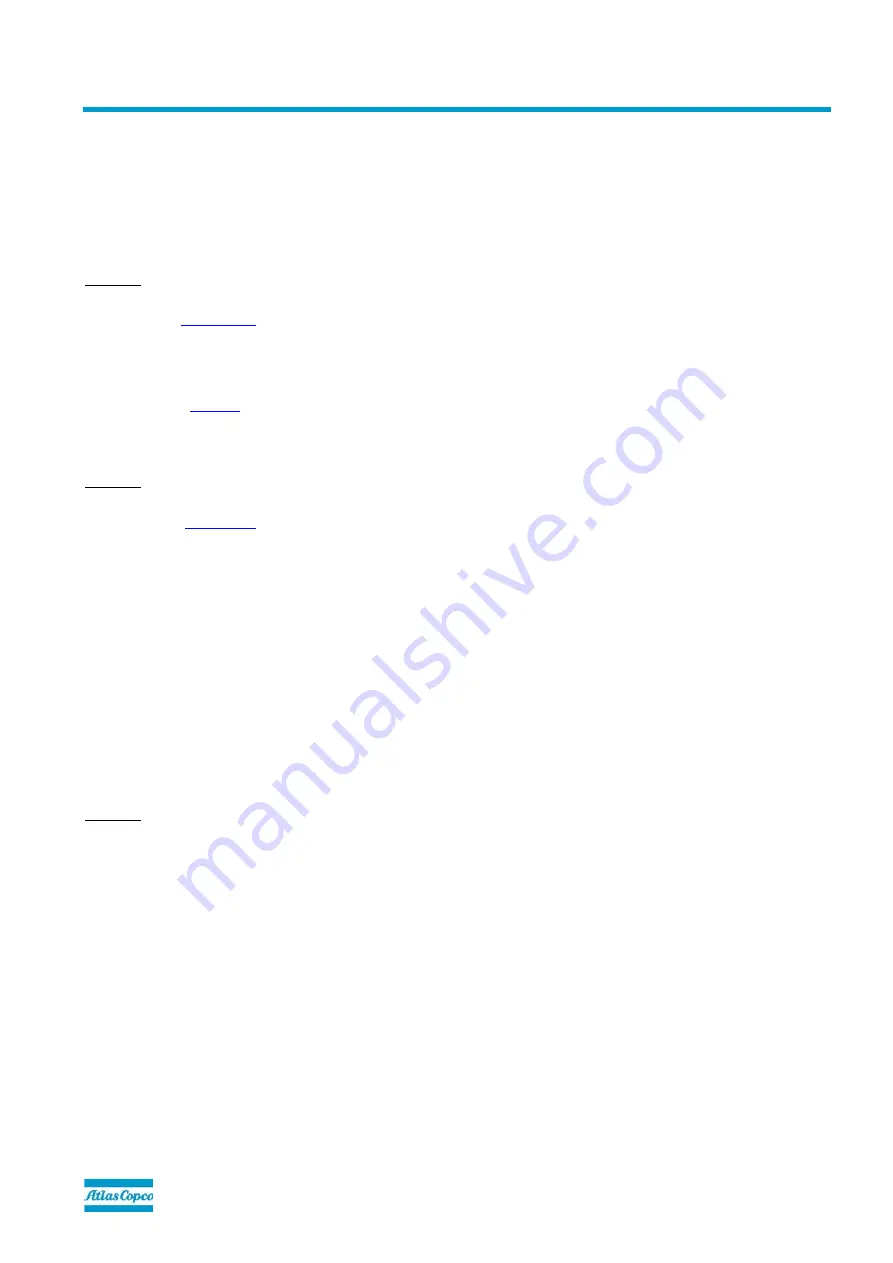
20/06/2011
PM 9845 0512 02
Page 19 of 36
6. Applications for the energy recovery system
6.1. General
The energy recovery system can be applied as a low temperature rise/high water flow system or as a high temperature
rise/low water flow system.
6.2. Low temperature rise/High water flow
For this type of application, the temperature difference between the water in the energy recovery system and the
compressor oil is low. Therefore, a high water flow is needed for maximum energy recovery.
Example:
Calculation: see
The heated water is used to keep another medium at a moderately high temperature in a closed circuit, e.g.
central heating.
6.3. High temperature rise/low water flow
NOTE:
The decrease in water flow to obtain higher water outlet temperatures will result in higher oil injection temperatures up to maximum
75°C. At this temperature, the 2nd bypass valve (Figure 3/4/5-14) will ensure that the oil injection temperature does not rise above
75°C. (See
for operation). The higher oil injection temperature will adversely affect the performance of the compressor.
The AML of the tropical thermostat option should therefore be applied when using the energy recovery in ‘high temperature rise/low
water flow’ type of applications.
This type of application generates a high water temperature rise in the energy recovery system, resulting in a low flow rate.
Example:
Calculation: see
An open circuit with cold water from a main supply being heated by the energy recovery system for use in a
factory, e.g. preheating boiler feed water.
6.4. Recovery water flow
The recovery water enters the ER unit at the water inlet connection (Figure 1-1). In the heat exchanger (Figure 1-8) the
compression heat is transferred from the compressor oil to the water. The water leaves the heat exchanger (Figure 1-8)
through the water outlet connection (Figure 1-2).
6.5. Recovery water requirements for closed water circuits
When the Energy Recovery system is integrated in a closed recirculation water circuit, the use of soft or even demineralised
water is economically beneficial and eliminates problems with scale deposits. Although the heat exchanger of the ER unit is
entirely made of stainless steel, the water circuit connected to the compressor may require corrosion inhibitors. Please refer
to the table below to minimize problems due to poor water quality. Please contact Atlas Copco in case of doubt.
Add an anti-freeze product, such as ethylene glycol, to the water as needed according to the expected temperature to avoid
freezing. Remember that adding ethylene glycol to the cooling water reduces the heat capacity of the coolant. The heat
capacity of ethylene glycol is only 61.2% of that of water. To obtain an equivalent cooling performance the coolant flow rate
must therefore be increased.
Example: if the coolant contains x% glycol in 100-x% water, the coolant flow rate should be increased by
38.8•x (100
−0.388•x)% versus 100% water.
Summary of Contents for ER S-1
Page 1: ...Atlas Copco Energy Recovery Stand Alone Kit Instruction book ...
Page 2: ......
Page 34: ...20 06 2011 PM 9845 0512 02 Page 32 of 36 Figure 17 9845 0070 00 Figure 18 9845 0071 00 ...
Page 35: ...20 06 2011 PM 9845 0512 02 Page 33 of 36 Figure 19 9845 0124 00 Figure 20 9845 0125 00 ...
Page 39: ......
Page 40: ...PM 9845 0512 02 2011 06 Printed in Belgium www atlascopco com ...