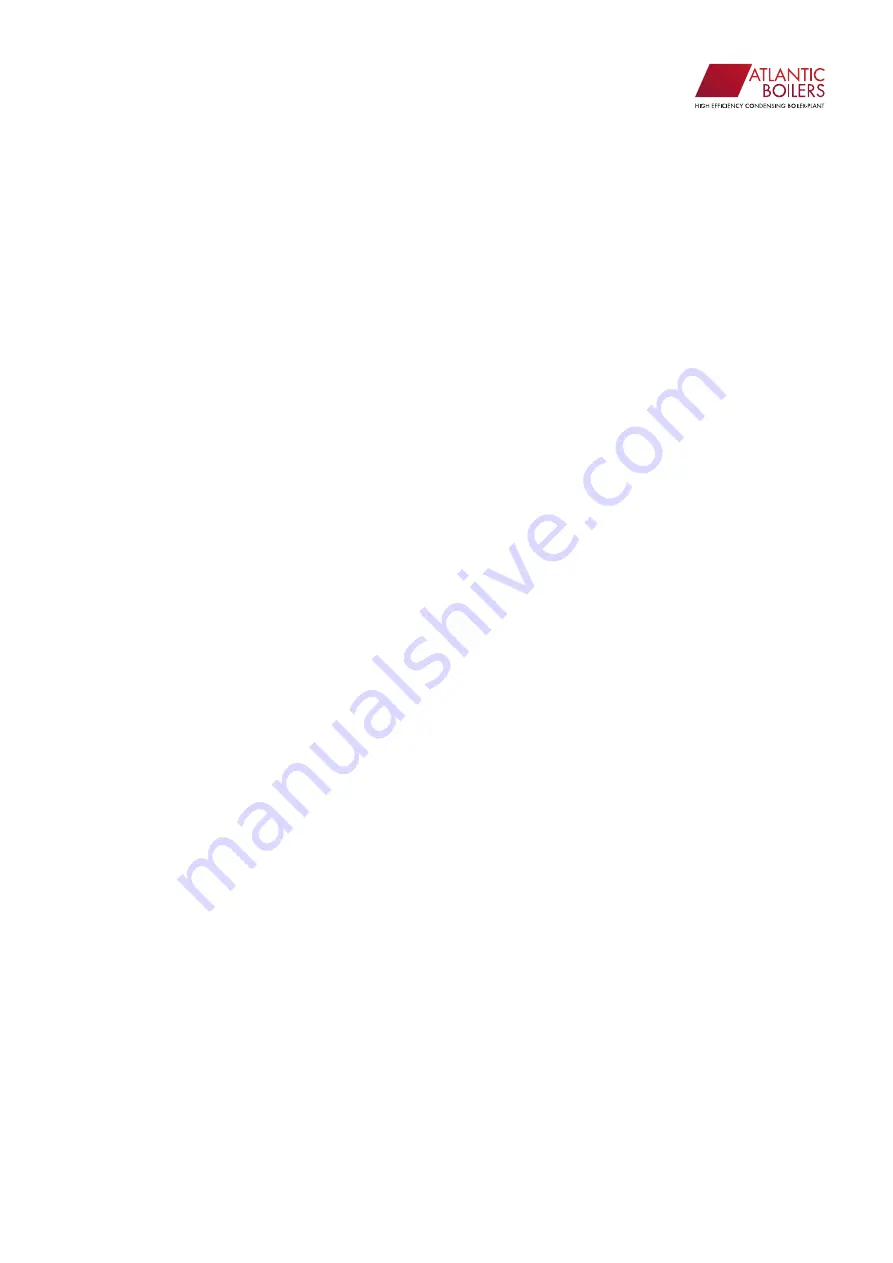
9
ME Standard Manual
2.4
Precautions
The Multi-elec Standard requires an installation conforming to:
• Directive 2009/125/CE (Eco-Design)
• Directive 2010/30/UE (Energy Labelling)
• Directive 2014/35/UE (Low Voltage)
• Directive 2014/30/UE (Electromagnetic compatibility)
• Directive 2014/68/UE (Pressure equipment directive)
• The electric boilers operate at more than 99.5%GCV efficiency
• They require minimal maintenance, are silent & are compact.
• With wind or water electric generation, they use green energy.
To release a large amount of heat to water heating systems:
A: They need a minimum static water pressure of 1 BAR when cold. When hot, this pressure will
rise and must not exceed 6 BARS for the normal boiler (higher pressures available)
B: They need a minimum water flow rate which is given in the boiler manual. Atlantic Boilers
offer a shunt pump set for each boiler which is fitted in the same pipe line as the boiler. The
pump will exceed the minimum water flow rate.
C: They must not exceed maximum water flow rate which is given in the boiler manual.
D: In case the pump fails or a valve is closed, Atlantic Boilers offer a water flow switch fitted
in the same pipeline as the boiler and set to just below maximum flow. If the switch registers
maximum flow, the boiler stops
E: We recommend an automatic pressurisation unit, with low and high pressure limits to
safeguard the electric boiler via its control panel. The unit will include a fast-fill loop to
initially fill the system.
F: The system should be isolated, flushed, filled and treated separately from the boiler.
Fill the boiler with clean, pure water only.
Detailed water treatment of Multi-elec electric boilers fitted with
adjoining balancing * sedimentation vessel
• Filling the outgoing secondary through the BSV pipework, the water can be variable due to its
source and it can be aggressive. It may need neutralisation by chemical additives or even the
use of Plate Heat Exchanger to divide the system out.
• The secondary water needs to be introduced though the BSV drain point or cold feed point.
• The electric boiler(s) need clean pure water introduced from the boiler drain valves
• The strainers, fitted in the secondary, need to be fitted in returns to the BSV where they
capture the most part of the deposits.
• The strainers, fitted in the boiler returns, need to be of fine extended secondary circuits,
mesh, to capture any overflow of deposit from the secondary circuits.