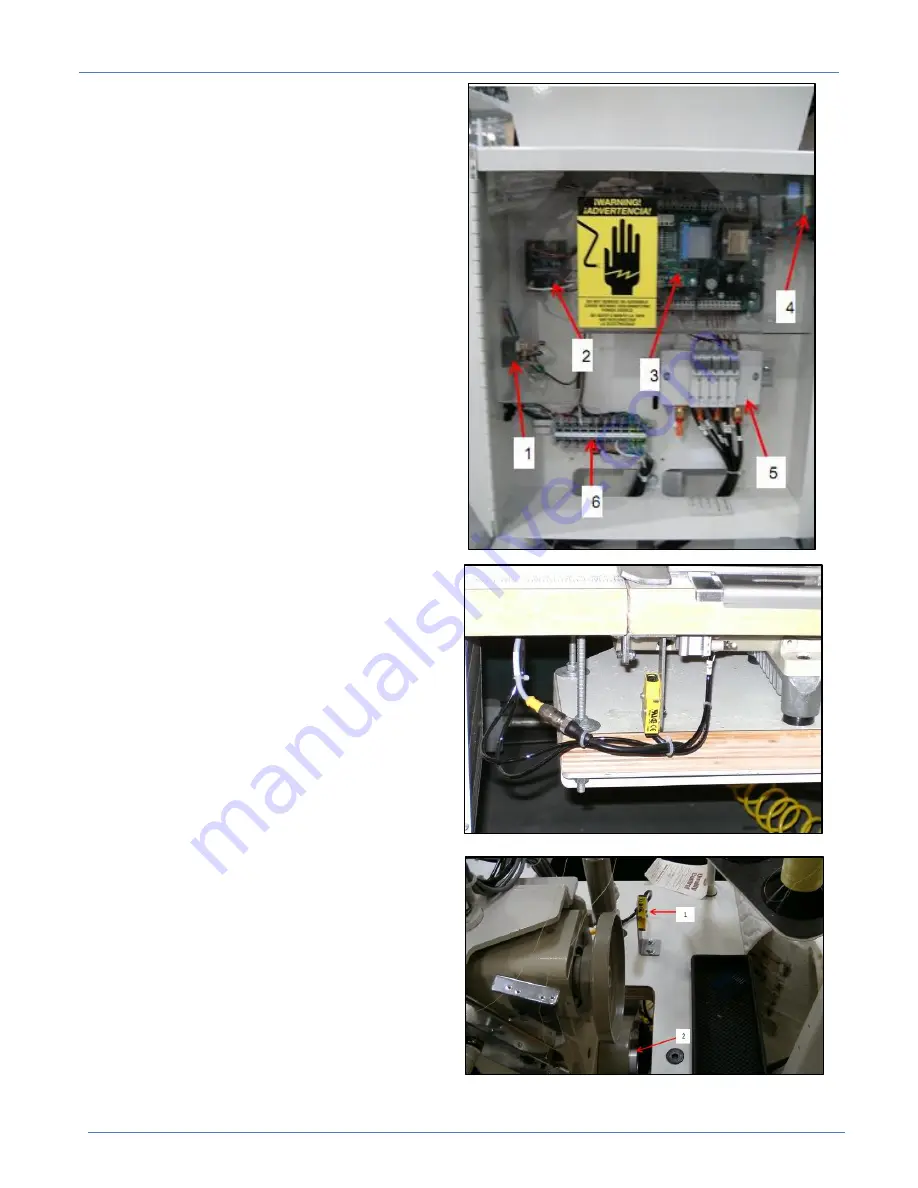
Technical Manual & Parts Lists
78
The door on the left side of the ruffler control box
gives access to the electronic components. The
on/off switch (1), the unwinder relay (2), the
computer board (3), the thumbwheels (4), the valve
assembly (5), the WAGO blocks (6). Do not
service this part of the machine while power is still
connected. Unplug the power cable from the back
of the control box, follow all lock out/tag out
procedures.
3.4.5.- Eyes
1.- Panel End Sew Eye
The panel end sew eye is located under the table
top, part of the flip down access. The panel end
eye, “looks” for the end of the panel. When the
end of the panel goes by it sends a signal to the
ruffler control box to start counting stitches for the
stop count, thumbwheels 3 and 4.
2.- Hand wheel Eye
The Hand wheel eye (1) is mounted to the top of
the table, behind and to the right of the sewing
head. The Hand wheel eye (1) reads a piece of
reflective tape located on the pulley disks (2). The
Hand wheel eye is responsible for reporting to the
Efka motor that the sewing head is sewing at the
set RPM, stitch counting for all counters, and for
needle position when stopping.
From
the
library
of:
Diamond
Needle
Corp
Summary of Contents for 1335MG
Page 2: ...From the library of Diamond Needle Corp ...
Page 106: ...Technical Manual Parts Lists 99 From the library of Diamond Needle Corp ...
Page 108: ...Technical Manual Parts Lists 101 From the library of Diamond Needle Corp ...
Page 110: ...Technical Manual Parts Lists 103 From the library of Diamond Needle Corp ...
Page 122: ...Technical Manual Parts Lists 115 From the library of Diamond Needle Corp ...
Page 126: ...Technical Manual Parts Lists 119 From the library of Diamond Needle Corp ...
Page 128: ...Technical Manual Parts Lists 121 From the library of Diamond Needle Corp ...
Page 130: ...Technical Manual Parts Lists 123 From the library of Diamond Needle Corp ...
Page 134: ...Technical Manual Parts Lists 127 From the library of Diamond Needle Corp ...
Page 136: ...Technical Manual Parts Lists 129 From the library of Diamond Needle Corp ...
Page 138: ...Technical Manual Parts Lists 131 From the library of Diamond Needle Corp ...
Page 140: ...Technical Manual Parts Lists 133 From the library of Diamond Needle Corp ...
Page 142: ...Technical Manual Parts Lists 135 From the library of Diamond Needle Corp ...
Page 144: ...Technical Manual Parts Lists 137 From the library of Diamond Needle Corp ...
Page 146: ...Technical Manual Parts Lists 139 From the library of Diamond Needle Corp ...
Page 148: ...Technical Manual Parts Lists 141 From the library of Diamond Needle Corp ...
Page 150: ...Technical Manual Parts Lists 143 From the library of Diamond Needle Corp ...
Page 154: ...Technical Manual Parts Lists 147 From the library of Diamond Needle Corp ...
Page 158: ...Technical Manual Parts Lists 151 From the library of Diamond Needle Corp ...
Page 160: ...Technical Manual Parts Lists 153 From the library of Diamond Needle Corp ...
Page 162: ...Technical Manual Parts Lists 155 From the library of Diamond Needle Corp ...
Page 164: ...Technical Manual Parts Lists 157 From the library of Diamond Needle Corp ...