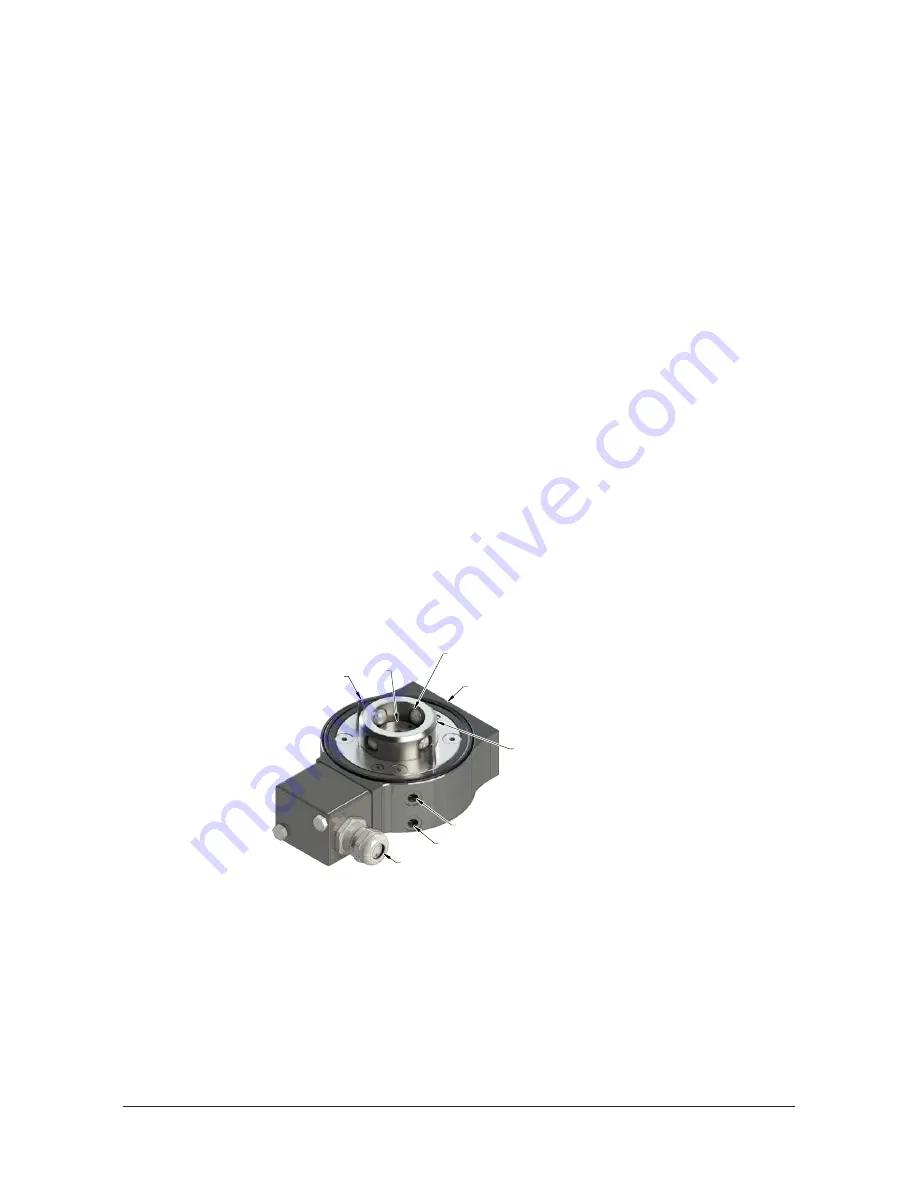
Manual, Robotic Tool Changer, QC‑24Z1
Document #9610‑20‑3727‑03
Pinnacle Park • 1041 Goodworth Drive • Apex, NC 27539 • Tel: 919.772.0115 • Fax: 919.772.8259 •
8
2. Product Overview
ATI Tool Changers enhance the versatility of a robot by enabling the use of multiple customer tools, such as:
grippers, vacuum cup tooling, pneumatic and electric motors, weld guns, and more.
The Tool Changer consists of a Master plate, which is attached to the robot arm, and a Tool plate, which is
attached to customer tooling. When the robot picks up the customer tooling, a pneumatically‑driven locking
mechanism couples the two plates. The patented, fail‑safe locking mechanism utilizes a multi‑tapered cam with
ball locking technology to ensure the Tool Changer does not uncouple If the air pressure falls below 60 psi (4.1 bar)
during operation.
The robot can be programmed to select the desired customer tooling by coupling the Master plate to the Tool plate.
Electricity, fluid, and other forces of energy transfer to the customer tooling through optional modules that are
attached to the Master and Tool plates. Refer to the ATI website for compatible modules or contact an ATI sales
representative for more details.
2.1 Master Plate Assembly
The Master plate assembly includes the following features:
•
A stainless steel body
•
A hardened stainless steel locking mechanism (a cam, male coupling, and tungsten
carbide ball bearings)
•
Hardened steel alignment pins that mate with bushings on the Tool plate.
•
(1) flat for mounting an optional module
•
Proximity sensor assemblies used to verify the lock/unlock position of the piston and cam
•
A mounting pattern for a robot arm or an interface plate
Non‑toxic food grade grease is applied to the cam, male coupling, ball bearings, and pins to enhance
performance and maximize the life of the Master plate.
Figure 2.1—Master Plate Assembly
M5 Lock Air Port
M5 Unlock Air Port
Lock/Unlock Sensor Cable Exit
Mounting Flat for Optional Module
Male Coupling
(4) Ball Bearing
(2) Alignment Pin Cam