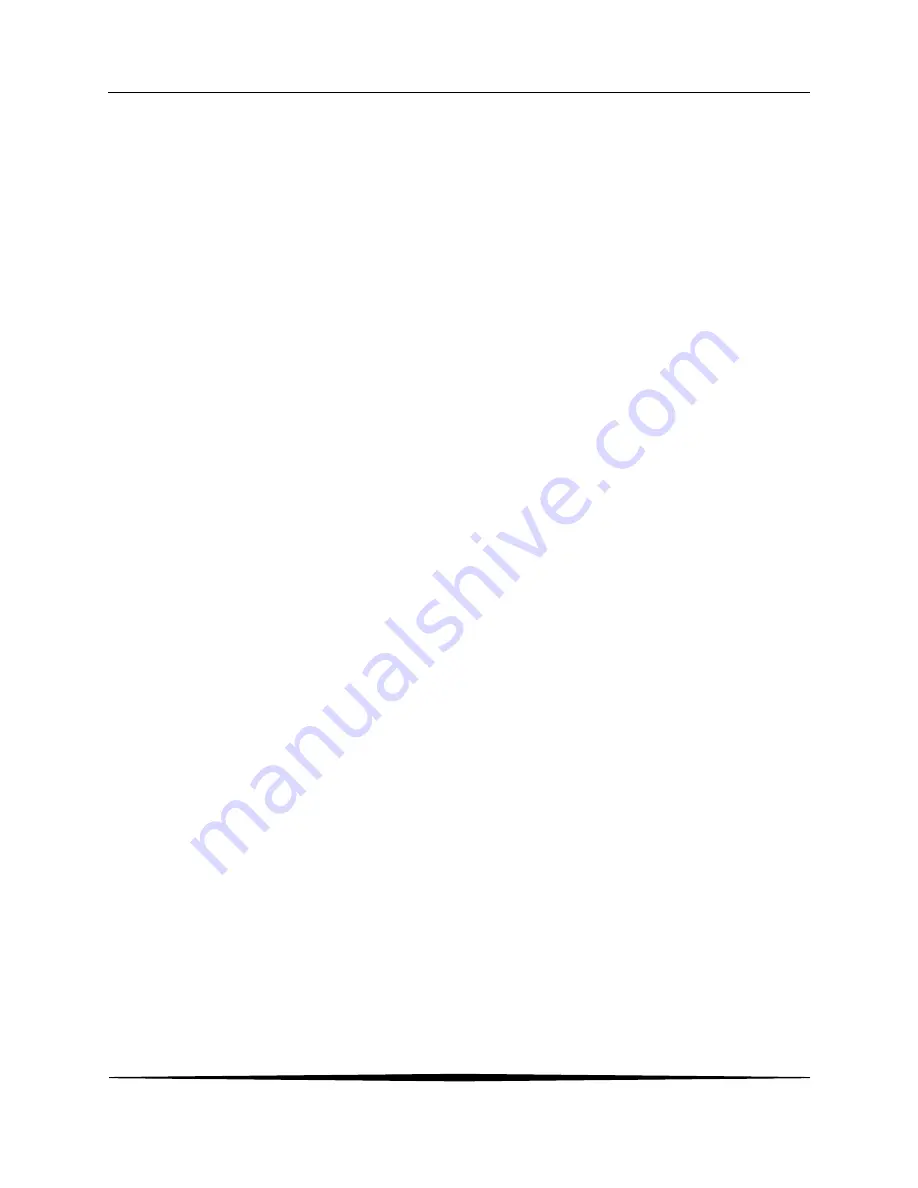
ATI
Q46H/64 Dissolved Ozone System
Part 8
– PID Controller Details
55
O&M Manual
Rev-J (11/18)
The most notable feature of the algorithm is the fact the proportional gain term affects all
components directly (unlike some other algorithms -
like the “series” form.) If a pre-existing
controller utilizes the same form of the algorithm shown above, it is likely similar settings can for
made if the units on the settings are exactly the same. Be careful of this, as many times the units
are the reciprocals of each other (i.e. reps-per-min, sec-per-rep.)
PID stands for “proportional, integral, derivative.” These terms describe the three elements of the
complete controller action, and each contributes a specific reaction in the control process. The
PID controller is designed to be primarily used in a “closed-loop” control scheme, where the
output of the controller directly affects the input through some control device, such as a pump,
valve, etc.
Although the three components of the PID are described in the setting area (section 6.25), here
are more general descriptions of what each of the PID elements contribute to the overall action of
the controller.
P
Proportional gain. With no “I” or “D” contribution, the controller output is simply a factor of
the proportional gain multiplied by the input error (difference between the measured input
and the controller setpoint.) Because a typical chemical control loop cannot react
instantaneously to a correction signal, proportional gain is typically not efficient by itself
–
it must be combined with some integral action to be useful. Set the P term to a number
between 2-4 to start. Higher numbers will cause the controller action to be quicker.
I
Integral gain. Integral gain is what allows the controller to eventually drive the input error
to zero
– providing accuracy to the control loop. It must be used to affect the accuracy in
the servo action of the controller. Like proportional gain, increasing integral gain results
in the control action happening quicker. Set the I term to a number between 3-5 to start
(1-2 more than P). Like proportional gain, increasing the integral term will cause the
controller action to be quicker.
D
Derivative gain. The addition of derivative control can be problematic in many
applications, because it greatly contributes to oscillatory behavior. In inherently slow
chemical con
trol process’, differential control is generally added in very small amounts to
suppress erratic actions in the process that are non-continuous, such as pumps and
valves clicking on and off. However, as a starting point for chemical process control, its
b
est to leave the “D” term set to 0.
Based on these descriptions, the focus on tuning for chemical applications really only involves
adjustment of “P” and “I” in most cases. However, increasing both increases the response of the
controller. The diffe
rence is in the time of recovery. Although combinations of high “P’s” and low
“I” will appear to operate the same as combinations of low “P’s” and high “I’s”, there will be a
difference in rate of recovery and stability. Because of the way the algorithm is structured, large
“P’s” can have a larger impact to instability, because the proportional gain term impacts all the
other terms directly. Therefore, keep proportional gain lower to start and increase integral gain to
achieve the effect required.
Many of the classical tuning techniques have the user start with all values at 0, and then increase
the P term until oscillations occur. The P value is then reduced to ½ of the oscillatory value, and
the I term is increased to give the desired response. This can be done with the Q46H controller,
with the exception that the I term should start no lower than 1.0.