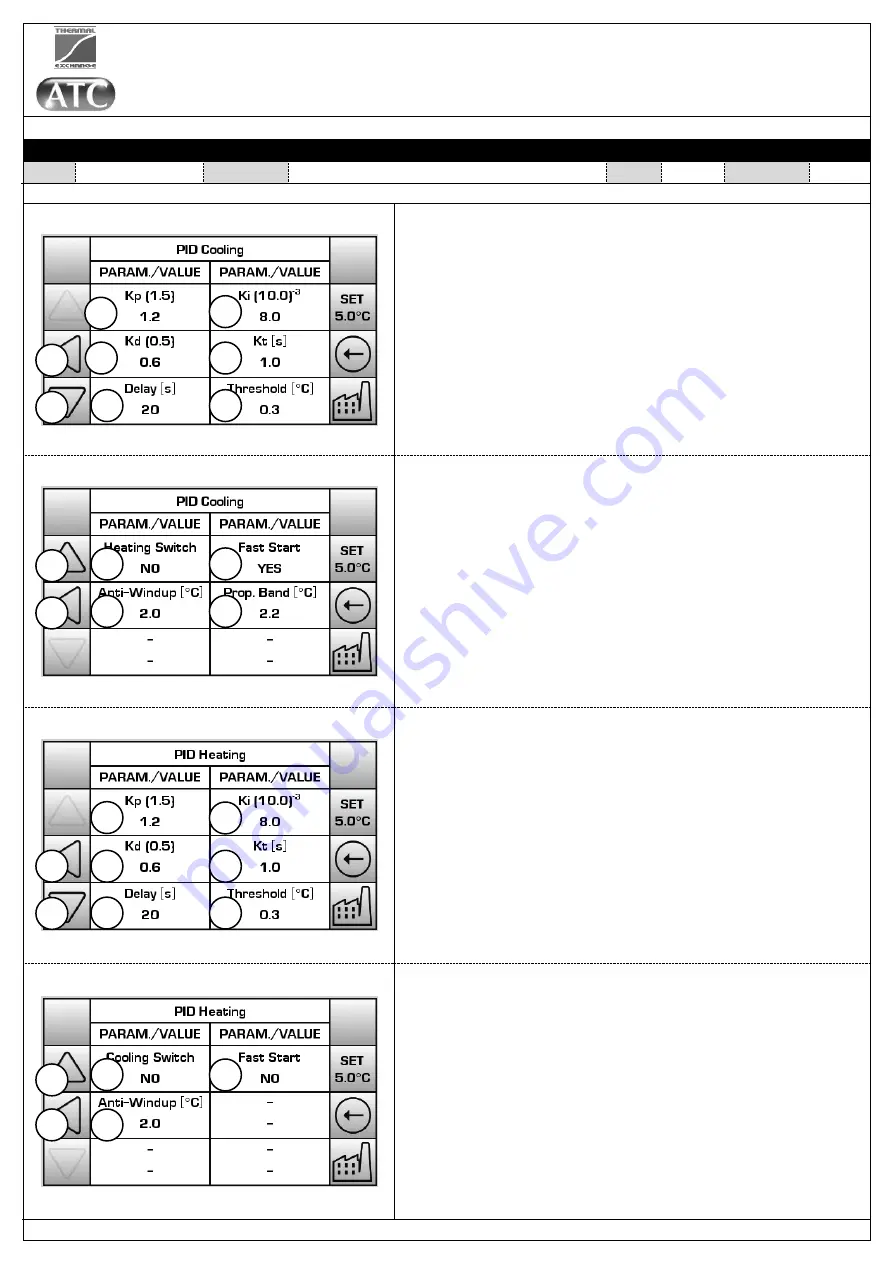
Applied Thermal Control Ltd
39 Hayhill Industrial Estate
Barrow-upon-Soar, Loughborough
LE12 8LD, United Kingdom
+44 (0) 1530 839 998
[email protected]
[email protected]
Operating Manual; Controller Operation
Annex E-1
DOCUMENT DETAILS
Date 5/DEC/2019
Author(s) MJH
Page 9 / 9
Revision 1
PID Cooling Settings (1)
1. Return to
‘Factory Settings’
main menu.
2. Scroll down for more settings.
3. Proportional term adjustment for cooling behavior.
4. Integral term adjustment for cooling behavior.
5. Derivative term adjustment for cooling behavior.
6. Cannot adjust
– this is time for a single PID loop.
7. Time elapsed until cooling PID changes to heating mode.
8. Delay counter
(7)
starts after overshoot exceeds this value.
PID Cooling Settings (2)
1. Return to
‘Factory Settings’
main menu.
2. Scroll up for more settings.
3. Allow heating mode to function via the solenoid valve.
4.
‘Yes’ enables compressor to start running immediately.
5. Integral term removed from PID calculation inside set range.
6. Outside this limit, P-
band control is ‘on-off’, i.e. 0 or 100%.
PID Heating Settings (1)
1. Return to
‘Factory Settings’
main menu.
2. Scroll down for more settings.
3. Proportional term adjustment for heating behavior.
4. Integral term adjustment for heating behavior.
5. Derivative term adjustment for heating behavior.
6. Cannot adjust
– this is time for a single PID loop.
7. Time elapsed until heating PID changes to cooling mode.
8. Delay counter
(7)
starts after overshoot exceeds this value.
PID Heating Settings (2)
1. Return to
‘Factory Settings’
main menu.
2. Scroll up for more settings.
3. Allow cooling mode to function via solenoid valve.
4.
‘Yes’ enables compressor to start running immediately.
5. Integral term removed from PID calculation inside set range.
1
1
1
1
2
2
2
2
3
4
5
6
7
8
3
4
5
6
3
4
5
6
7
8
3
4
5
Annex E-1 200707 XTD controller XTD043RB-K620G&F (Mini at SW v39.4)
18