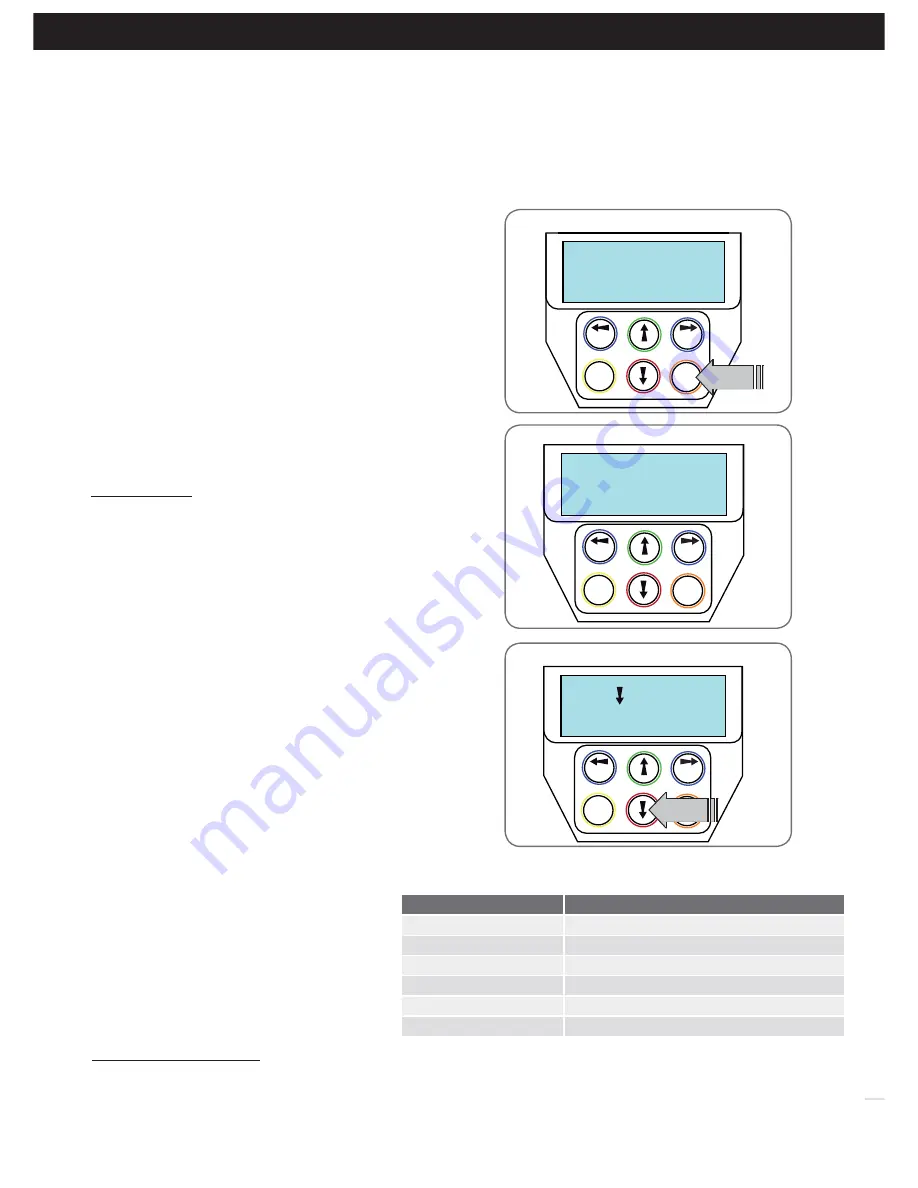
30
DCB-05V2 Gate Controller
Owner Installation Instructions
Hold To Set
PREV
NEXT
EXIT
SET
Close Cycle Time
PRESS
This section shows how to set the travel times when using drive units with slip clutches etc. Two methods are available for
setting up the travel times. The first allows the installer to drive the motor(s) so that the actual travel time can be recorded.
The second allows exact times to be entered.
Current Trips
PREV
NEXT
EXIT
SET
Are Disabled OK?
PRESS
Confirming Obstruction detection is disabled
I - Time Travel 2 Wire Setup
Appendix
Fig I.1
Fig I.2
SET=Drive Motors
PREV
NEXT
EXIT
SET
EXIT=Enter times
Selecting install method
Setting close cycle time
Fig I.3
Fig I.4
Parameter
Description
M1 Normal Open Time
Sets Open drive time for M1
M1 Normal Close Time
Sets Close drive time for M1
* M2 Normal Open Time
Sets Open drive time for M2
* M2 Normal Close Time
Sets Close drive time for M2
* Close Sync Delay
Sets Delay before M1 is started on closed cycles
* Open Sync Delay
Sets Delay before M2 is started on open cycle
* Only used for dual gate installations. Once the parameter values have be set
press EXIT and the main screen is displayed, the gate is ready for use.
NOTE: The limit setting procedure can be aborted at any time by
pressing EXIT.
Navigating To “Timed Travel Menu”
a. Press NEXT to navigate to Menu 10.
b. Presee SET to locate Menu 10.2.
c. Press SET again to start the the setup.
d. Confirm that the motor wiring is complete. Press SET to continue.
e. No current trip obstruction detection is available when using timed
travel. Press SET if you accept this
(Fig. I.1
)
.
f. Enter the number or motors by using the UP or DOWN key to
select the correct number and then press SET.
Selecting Setup Method
a. DCB-05V2 will now prompt for the setup procedure to be selected.
There are 2 methods
(Fig. I.2)
;
i. DRIVE MOTORS = Press SET to continue
ii. ENTER TIME PARAMETERS = Press EXIT to continue
DRIVE MOTORS
Adjusting Gate Leaf Synchronising Delays.
(Dual gate installations only)
DCB-05V2 will prompt for you to edit the gate leaf synchronising
delays. The settings are used to introduce a delay between when
the motors start so that overlapping gates are opened and closed in
the correct order.
a. Press SET to access the gate leaf synchronising delay parameters
b. Follow LCD display to edit delay.
Confirming Gate Is Open
DCB-05 will now prompt for you to confirm that the gate is open.
a. If the gate is open press SET and continue.
b. If the gate is closed Press EXIT and DCB-05 will now prompt for
the gate to be opened.
i. Press and Hold the UP key until the gate is open. When the UP
key is released the motor(s) will stop and you will be asked if
the gate is open.
NOTE:
If the motor drives in the wrong direction the motor wiring
needs to be swapped.
Setting Close Cycle Drive Time
To set the close cycle drive time press and hold the DOWN key until
the gate is driven fully closed.
(Fig I.3)
NOTE:
If the motor drives in the wrong direction the motor wiring
needs to be swapped.
Setting Open Cycle Drive Time
To set the open cycle drive time press and hold the
UP key until the gate is driven fully open.
Confirming Settings
Press SET to confirm or EXIT to restart from
Confirming gate is open.
Once the setting have been SET and the main
screen is displayed, the gate is ready for use.
ENTER TIME PARAMETERS
When the ENTER TIMES method is selected a list
of parameters is provided to configure the gates
travel. The parameters provided are listed below
in
Fig I.4
with a brief description
.