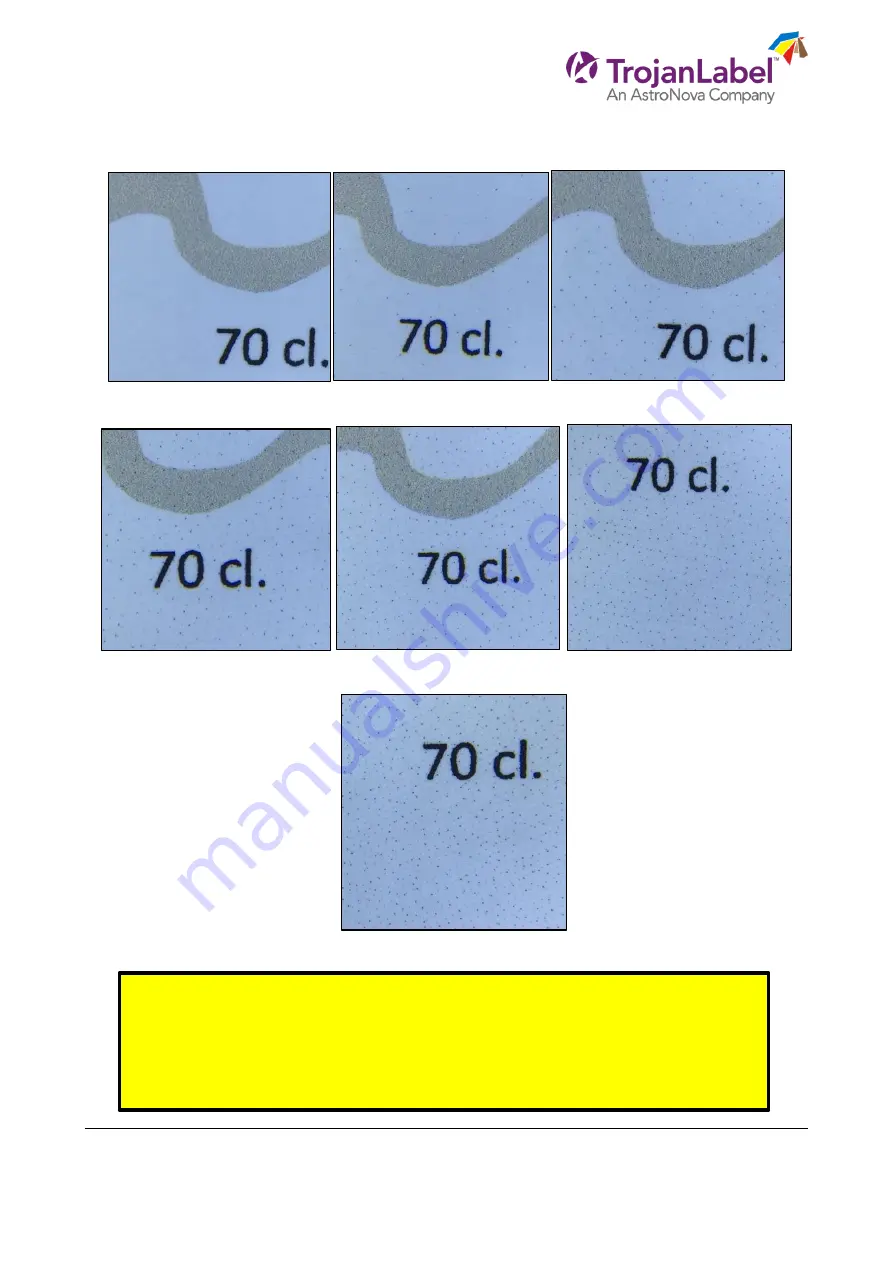
TrojanTwo-Compact User Guide v3.8
Page | 74
KWS levels:
KWS level 0
KWS level 1
KWS level 3
KWS level 5
KWS level 7
KWS level 9
KWS level 11
WARNING:
The degree of KWS has effect on printhead life. The higher KWS level is set the more
protection the printhead gets against dehydration of nozzles. ALTHOUGH switching KWS
off (0) does not result in loosing warranty for the printhead, it is still advised to enable
KWS and set it to a level where the small dots are still acceptable in terms of print
quality.