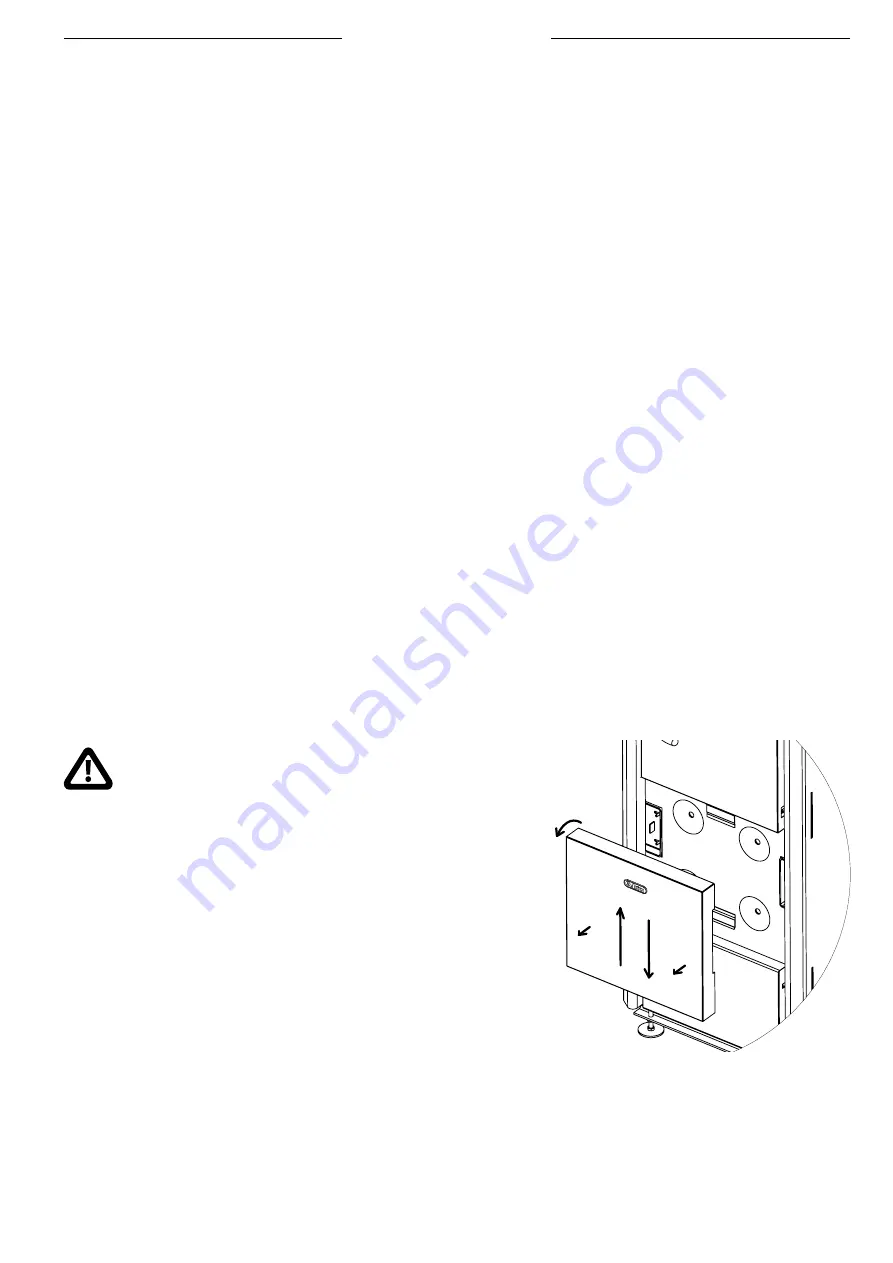
20
HEATING BOILERS: Astra G-120E
Although the optimal smoke temperature is set up in the factory, we recommend that you set the temperature by yourself
once again after the installation of the boiler at its operation place. In this way, a more precise temperature will be set up
with respect to the fuel used, draught and other peculiarities of the installation. For that purpose, the boiler must be brought
up to an optimal and stable operation mode, and the smoke temperature at this time must be determined and fixed. First,
set the water temperature on the boiler controller; we recommend 85°C, or at least 75°C. This temperature should be the
one you will use to set in the future boiler operation. Kindle the boiler using the two stages method described in the chapter
“Fire bed and tips for effective boiler stoking”. Verify the state of combustion by opening the lower door after 45-60 minutes
from the beginning of firing. At that moment, the flame tongue must be reaching the lower ceramic element, and the colour
of the tongue must be yellow-red. Then check the actual smoke temperature by pressing the controller knobs “P” and “+”
simultaneously. As a result, the screen should display a two-digit number representing the actual smoke temperature. The
number must be multiplied by 10 to determine the actual temperature. For example, if the number 16 is displayed, that
means that the actual measured smoke temperature is 160°C. The number will stay lit for 3 seconds. During this period,
the controller knob “P” must be pressed again. The number on the display will blink and will then stay lit permanently for a
short moment; after 3 next seconds, the controller will automatically leave the programming mode and return to its usual
operation mode. Now the new optimal smoke temperature has been set up.
In a usual boiler operation, after the firing has been completed, the smoke temperature sensor will help to turn off the
ventilator of the boiler and the circulation pump. When the temperature of the flue gases drops bellow 75°C, the rotational
speed of the ventilator is minimized and after some more time, the ventilator and circulation pump are turned off.
If you think that that the smoke temperature sensor is unnecessary for your boiler, you can easily shut it off. For that purpose,
take off the rooftop panel of the boiler (Fig.7) and unplug the sensor from the controller’s X3 socket. The boiler controller will
automatically switch to operate by another programme controlling the boiler without the smoke temperature sensor.
• CLEANING THE BOILER
Ashes are removed from the boiler every 4-7 days. Open the door of the upper combustion chamber and shovel ashes down
to the lower chamber. Open the door of the lower chamber, take out only ceramic segments 3 (Fig. 2), pour ashes to a metal
box. Plates of the ceramic basket should not be removed while cleaning.
In any case, strictly follow the established procedure
when opening the upper door: open the damper of the upper
flue, then after 20 seconds, open the boiler door.
Clean boiler chambers from tar, pitch and scurf once or twice a month.
Clean the boiler when the fuel has been completely burned and the
boiler is cooled down to at least +40°C.
Clean the heat exchanger tubes 34 (Fig. 1) with a crescent-shaped
scraper. Push the scraper forwards with the round side turned up. Move
it backwards with the round side positioned down. That way you will be
able to extract the combustion residues in front of the tubes for further
sweeping.
Open the upper cap 21 for cleaning the flue (Fig. 1). Remove the
turbulence plates from the flue by hooking them and pulling them out
with the poker, then clean them using a scraper. Clean tar and scurf from
combustion chambers and flue walls using a scraper and metal hog.
1 3
4
2
4
Fig. 14 Front side panel removal.
1. Push the panel upwards till reaching a door. 2. Lean
the upper side of the panel towards yourself. 3. Push the
panel downwards till reaching a door. 4. Pull the panel
towards yourself and remove.