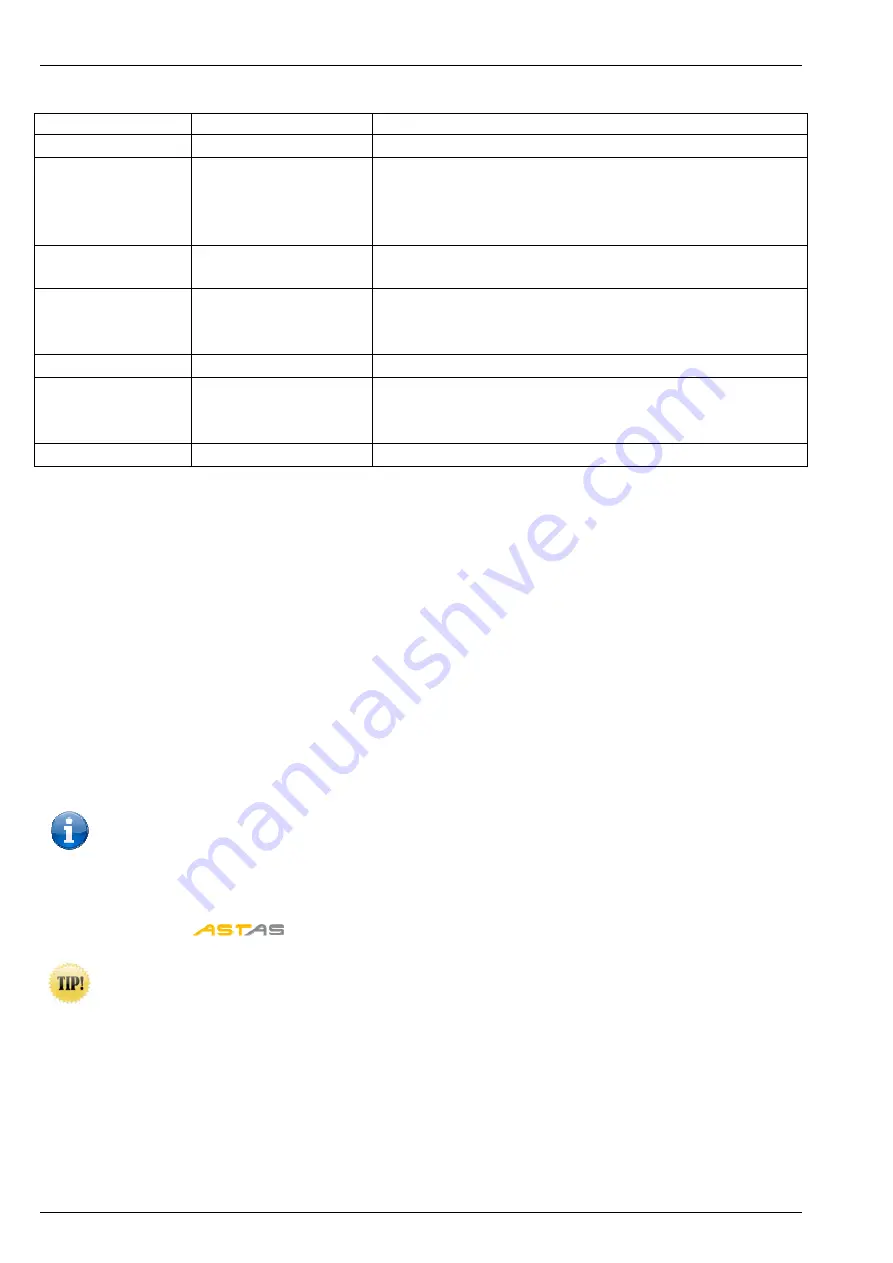
Manual BA 662
Page 8 of 10
Technical changes reserved. 09/2016
A.S.T. - Angewandte System Technik GmbH, Mess- und Regeltechnik
4.7. LED Status
LED display
Explanation
Error description
Green
Ready for operation
No error
Red 1 x flashing
ADC-Overload
Error at connections of sensor lines
Cable break in sensor line
Switch for 6- and 4-wire not accordingly
connected
Red 2x flashing
Indicates overload
or underload
Exceed of maximum load of 120% of nominal
sensitivity, or exceed minimum load (
see too 4.6
)
Red 3x flashing
TEDS error
Error in the memory of the automatic sensor
recognition
(only option with TEDS)
Red 4 x flashing
Output > 100%
The amplification at the output is set too high.
Red 5 x flashing
Current output open
or overheating DAC
Output side not closed
Cable break at output
Thermal overheating - cooling necessary
Red 6 x flashing
Hardware error
General error – restart necessary
4.8. Restart
100% - and >0% +< simultaneously: A restart is carried out. All settings are saved.
4.9. Factory setting (RESET)
For all ten
sensitivity settings
/ measuring ranges (see 4.1 – sensitivity in mV/V of the sensor)
factory settings are stored in the amplifier.
Individual adjustments of the amplification (see 4.3.) or of the zero point (see 4.4) carried out
later by the user, do only influence the active measuring range that has just been set.
When simultaneously pushing the two keys >100% +< and >0% -< for 2s, all zero-point
adjustments and end-value adjustments of all ten measuring ranges are deleted and reset to
the factory settings of 0mV/V
≙
initial value of the selected signal output (-5/-10/0V or 0/4mA)
and 2mV/V
≙
end value of the selected signal output (5/10V or 20/24mA).
NOTE!
After reset to factory settings, the amplifier has to be newly adjusted to the
sensor!
5. Using the Software ASTAS (USB)
Load the software
from our website www.ast.de
TIP: Linearization:
If the measured values between zero and rated load should
deviate from the real load, up to four additional points can be set to increase the
measurement accuracy. These measuring points can be made in any order, similar to
the input of the zero point and end point. After entering all of the calibration points, the
result must be stored.