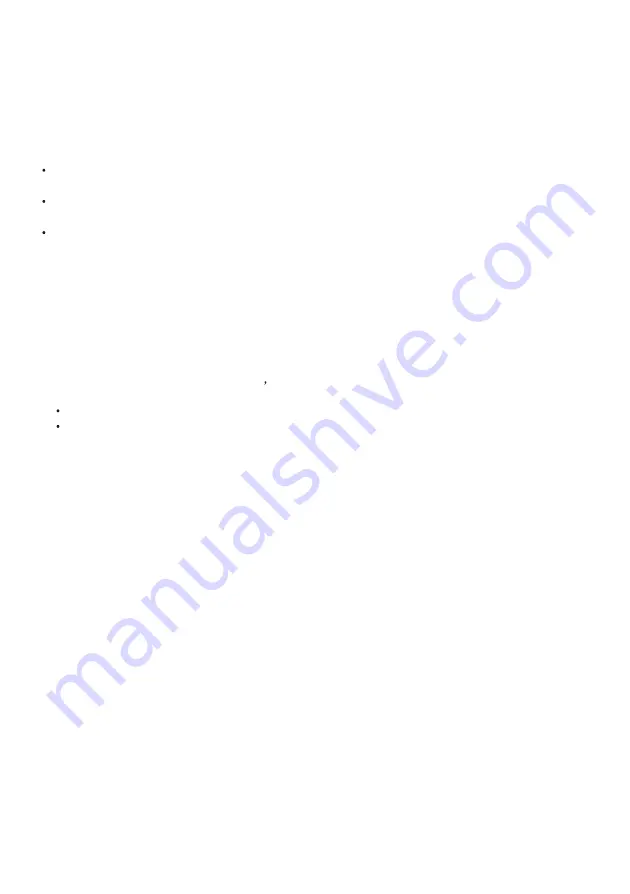
.
9. Checks to electrical devices
The repair and maintenance of electrical components shall include preliminary safety inspection
and component inspection procedures. If there are faults that may endanger safety, do not
connect any power source to the circuit until the circuit is satisfactorily handled. If the failure
cannot be corrected immediately, but it is necessary to continue the operation, an appropriate
temporary solution should be used. This should be reported to the equipment manufacturer in
order to inform the parties
Initial safety checks shall include:
that capacitors are discharged: this shall be done in a safe manner to avoid possibility
of sparking
that there no live electrical components and wiring are exposed while charging, recovering
or purging the system;
that there is continuity of earth bonding
10. Sealed components maintenance
.
10.1 During repairs to sealed components, all electrical supplies shall be disconnected from the
equipment being worked upon prior to any removal of sealed covers, etc. If it is absolutely
necessary to have an electrical supply to equipment during servicing, then a permanently
operating form of leak detection shall be located at the most critical point to warn of a
potentially hazardous situation.
10.2 Particular attention shall be paid to the following to ensure that by working on electrical
components, the casing is not altered in such a way that the level of protection is affected.
This shall include damage to cable
excessive number of connections, terminals not made
to Original specification, damage to seals, incorrect fitting of glands, etc.
Ensure that apparatus is mounted securely
Ensure that seals or sealing materials have not degraded such that they no longer serve
the purpose of preventing the ingress of flammable atmospheres. Replacement parts shall
be in accordance with the manufacturer s specifications.
11.Safe components
Do not impose any permanent inductive or capacitive load on the circuit unless it is ensured that
it will not exceed the voltage and current allowed by the equipment in use. This machine safety
component is the only type that can be operated in the presence of flammable gases. The test in
strument should have the correct rating. Replace components only with parts specified by the
manufacturer.
.
12.Cabling mantainence
Check the cable for wear, corrosion, excessive pressure, vibration, sharp edges, or any other
adverse environmental effects. The inspection should also take into account the effects of aging
or continuous vibration such as compressors or fans.
.
13.Detection of flammable refrigerants
Under no circumstances shall potential sources of ignition be used in the searching for Or
detection
of refrigerant leals.
For systems containing flammable refrigerants, the following leak detection methods are consid-
ered acceptable. An electronic leak detector should be used to detect flammable refrigerants, but
the sensitivity may be insufficient or may require recalibration. (The testing equipment should be
calibrated in an area free of refrigerant.) Make sure that the tester is suitable for the refrigerant.
Leak detection equipment should be set as a percentage of the refrigerant LFL, and should be
calibrated for the refrigerant used, and confirm the appropriate percentage of gas (maximum 25%).
Leak detection fluids are suitable for most refrigerants, but the use of chlorine-containing cleaning
agents should be avoided because chlorine may react with the refrigerant and corrode the copper
pipes. If a leak is suspected, all open flames should be cleared or extinguished. If it is found that
the refrigerant that needs to be brazed leaks, all the refrigerant should be recovered from the
system, or be isolated in the system part away from the leakage through the shut-off valve.
39