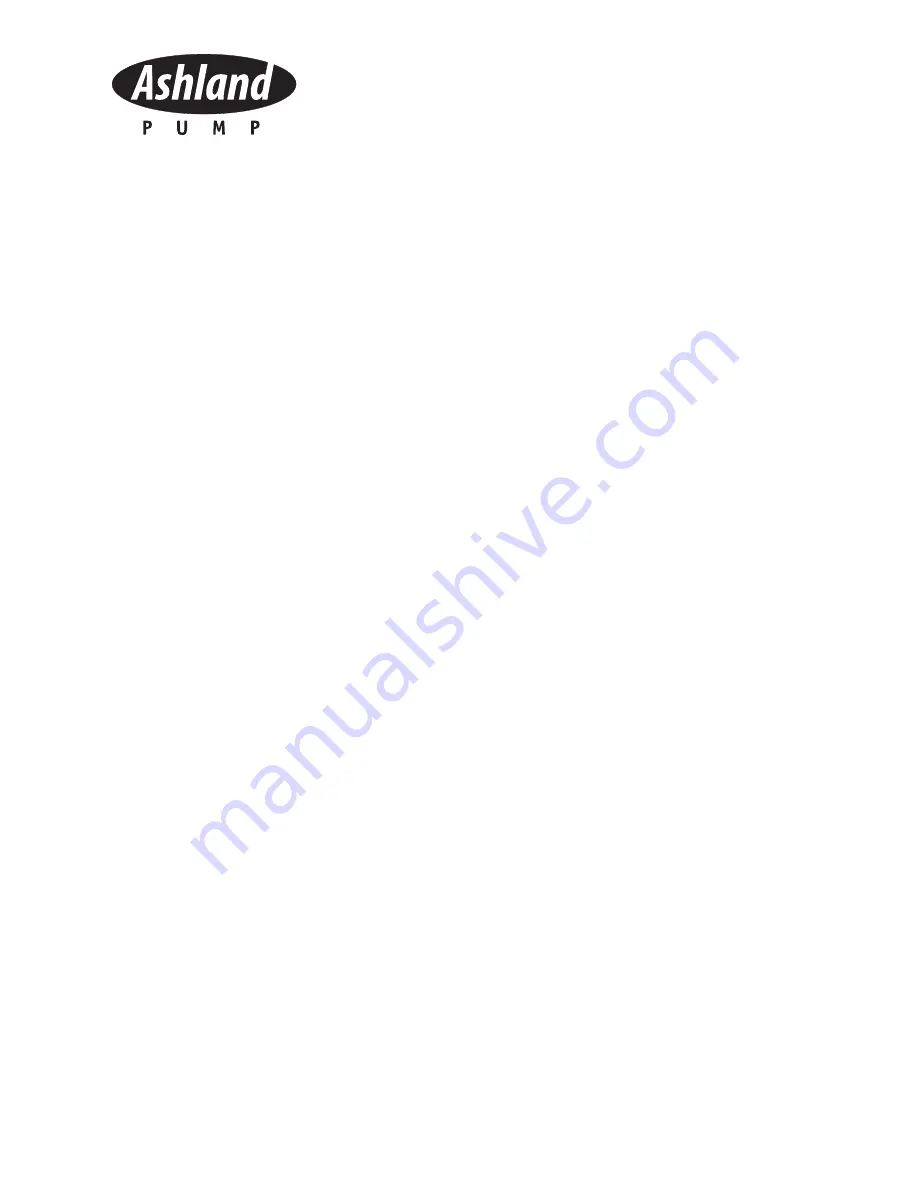
8
Solids Handling Pumps
Models: ANC200/300/500/750/1000/1500 /2000
& ANCV200/300/500/750/1000/1500 /2000
Installation
The reading should be 100,000 ohms or greater. If the
measured values are below those indicated above, then
the pump may have a lower seal failure and require ser-
vice.
Note:
Failure to use proper circuitry and to connect the
motor overheat protection and seal leak detection in the
control panel would negate all warranties.
Motor power cord, control cord and cord cap assembly
Each motor power cord has 4 conductors: white, black,
red and green. See Figure 3 for internal wiring schematic.
Note:
Rotation should be clockwise when observed from
the top of the pump. This can be checked by noting
which direction the pump torque is upon initial starting.
A properly rotating pump will torque counterclockwise
upon start.
The control cable has 5 conductors:
black, white, red, yellow and green. White and black con-
nect to the heat sensor terminals; red and yellow
connect to the seal failure leads; and the green connects
to the ground in the control panel. (Figure 3)
Note:
Each cable has a green ground wire and must be
properly grounded per the National Electric Code and
local codes.
Electrical Motor Controls
All electrical controls and motor starting equipment
should be as specified in these instructions.
Pre-operation
CHECK VOLTAGE AND PHASE
Before operating pump, check to make sure that voltage
and phase information stamped on the pump’s identifica-
tion plate matches the available power.
CHECK PUMP ROTATION
Before putting pump into service for the first time, the
motor rotation must be checked. Improper motor rota-
tion can result in poor pump performance and
can damage the motor and/or pump.
IDENTIFICATION PLATE
Note the numbers on the pumps identification plate and
record at the end of this manual for future reference.
Discharge Piping
Install discharge piping or hose assembly to the pump.
Discharge piping should be as short as possible and sized no
smaller than the pump discharge. Do not reduce the dis-
charge pipe size below that which is provided on the pump.
Both a check valve and a shut-off valve are recommended
for each pump. The check valve is used to prevent backflow
into the sump. The shut-off valve is used to manually stop
system flow during pump servicing. Be sure the discharge
pipe has a 1/8” diameter hole approx. 5” from end nearest
volute and oriented towards the pump body.
Control Panel
All pumps require a controll panel. Single/phase models
require start components in panel.
Motor Seal Failure Warning
In all models,the seal chamber is oil filled and provided
with moisture sensing probes to detect water leakage
through the lower shaft seal. The probes can also detect
moisture present in the upper motor housing.
The presence of water energizes a red seal leak warning
light at the control panel. This is a warning light only, and
does not stop the motor. It indicates a leak has occurred
and the pump must be repaired. Normally, this indicates
the outboard seal has leaked. Allowing the unit to oper-
ate too long after the warning could cause upper seal
leakage along with motor failure.
The resistance across the moisture sensing (seal failure)
probes should be checked after a seal leak warning light
has lit. This can be done by disconnecting the red and or-
ange control wires from the control panel, and measuring
the resistance with an ohmmeter between the wires.