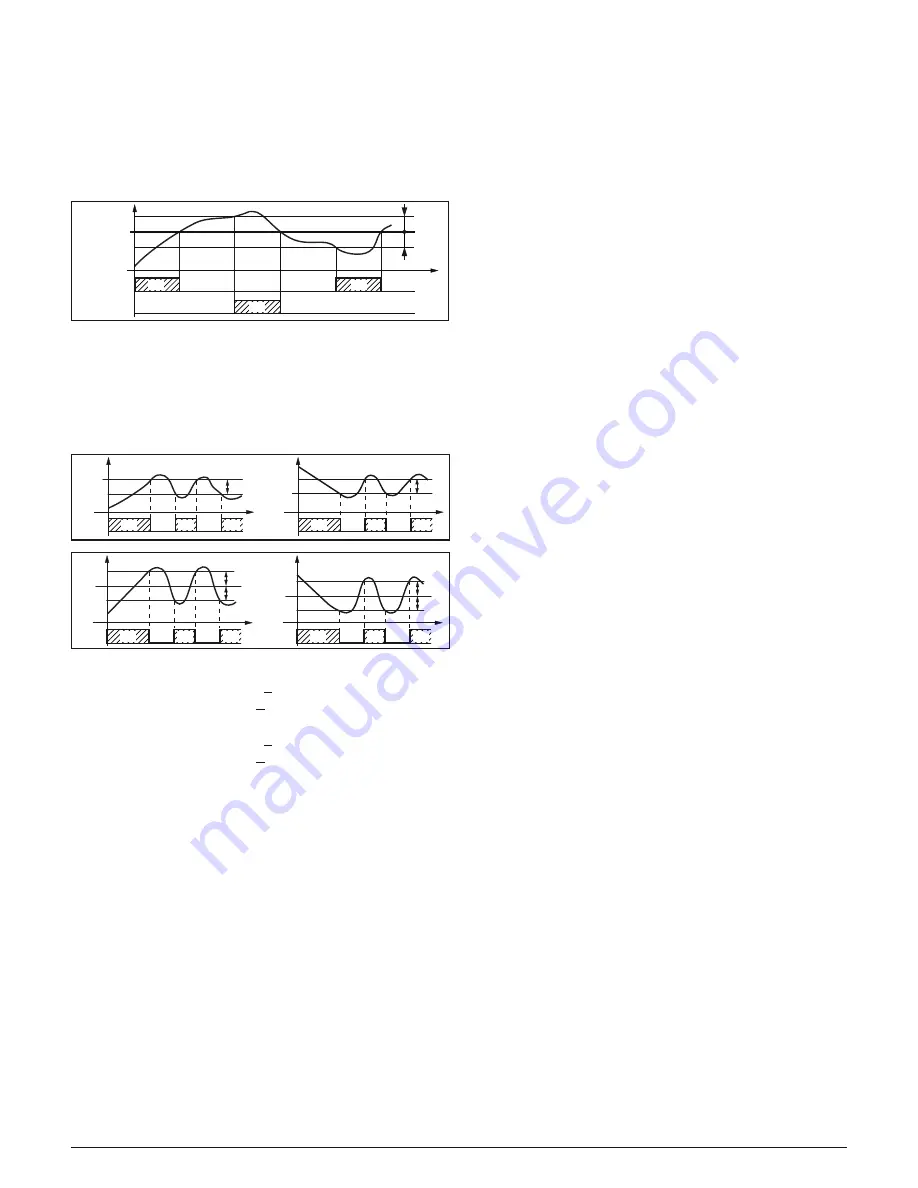
Ascon Tecnologic - KX6 - ENGINEERING MANUAL -
PAG. 12
]
rEG group - Control parameters
.
[39] cont - Control type:
Available:
When at least one output is programmed as con-
trol output (H.rEG or C.rEG).
Range: •
When two control actions (heat & cool) are pro-
grammed:
Pid
PID (heat and cool);
nr
Heat/Cool ON/OFF control with neutral zone;
HSEt
HSEt
SP
PV
time
OUTH.rEG
(heating)
OUTc.rEG
(cooling)
off
ON
ON
off
off
ON
•
When one control action (heat or cool) is pro-
grammed:
Pid
PID (heat or cool);
On.FA ON/OFF asymmetric hysteresis;
On.FS ON/OFF symmetric hysteresis;
3Pt
Servomotor control (available when Out 1
and Out 2 have been ordered as “
MM
”).
HEAt - On.FA
OUT
H.rEG
SP
PV
HSEt
time
off
off
CooL-On.FA
OUT
C.rEG
SP
PV
HSEt
time
ON
ON
ON
off
off
ON
ON
ON
HEAt - On.FS
SP
PV
HSEt
HSEt
time
C ooL - O n.FS
SP
PV
HSEt
HSEt
time
OUT
H.rEG
off
off
OUT
C.rEG
ON
ON
ON
off
off
ON
ON
ON
Notes: 1.
ON/OFF control with asymmetric hysteresis:
•
OFF when PV > SP;
•
ON when PV < (SP - hysteresis).
2.
ON/OFF control with symmetric hysteresis:
•
OFF when PV > (SP + hysteresis);
•
ON when PV < (SP - hysteresis).
[40] Auto - Auto tune selection
Ascon Tecnologic has developed three auto-tune algorithms:
–
Oscillating auto-tune;
–
Fast auto-tune;
–
EvoTune.
1.
The
oscillating
auto-tune is the usual auto-tune and:
•
It is more accurate;
•
Can start even if PV is close to the set point;
•
Can be used even if the set point is close to the
ambient temperature.
2.
The
fast type
is suitable when:
•
The process is very slow and you want to be opera-
tive in a short time;
•
When an overshoot is not acceptable;
•
In multi-loop machinery where the fast method reduces
the calculation error due to the effect of the other loops.
3.
The
EvoTune
type is suitable when:
•
You have no information about your process;
•
You can not be sure about the end user skills;
•
You desire an auto tune calculation independently
from the starting conditions (e.g. set point change
during tune execution, etc).
Note:
Fast auto-tune can start only when the measured
value (PV) is lower than (SP + 1/2 SP).
Available:
When [39] cont = PID or 3Pt.
Range:
-4... 8 where:
-4
Oscillating auto-tune with automatic restart at
all set point change;
-3
Oscillating auto-tune with manual start;
-2
Oscillating auto-tune with automatic start at the
first power up only;
-1
Oscillating auto-tune with automatic restart at
every power up;
0
Not used;
1
Fast auto tuning with automatic restart at every
power up;
2
Fast auto-tune with automatic start at the first
power up only;
3
FAST auto-tune with manual start;
4
FAST auto-tune with automatic restart at all set
point change.
5
EvoTune with automatic restart at every power up;
6
EvoTune with automatic start at the first power
up only;
7
EvoTune with manual start;
8
EvoTune with automatic restart at all set point
change.
[41] tunE - Manual start of the auto-tune
Available:
When [39] cont = PID or 3Pt.
Range:
oFF
The instrument is not performing the auto-tune;
on
The instrument is performing the auto-tune.
[42] HSEt - Hysteresis of the ON/OFF control
Available:
When [39] cont is different from PID or 3Pt.
Range:
0... 9999 engineering units.
[43] Pb - Proportional band
Available:
When [39] cont = PID or 3Pt.
Range:
1... 9999 engineering units.
Note:
Auto-tune functions calculate this value.
[44] ti - Integral time
Available:
When [39] cont = PID or 3Pt.
Range:
OFF = Integral action excluded;
1... 9999 seconds;
inF= Integral action excluded (reserved).
Note:
Auto-tune functions calculate this value.
[45] td - Derivative time
Available:
When [39] cont = PID or 3Pt.
Range:
oFF - derivative action excluded;
1... 9999 seconds.
Note:
Auto-tune functions calculate this value.
[46] Fuoc - Fuzzy overshoot control
This parameter reduces the overshoot usually present at
instrument start up or after a set point change and it will be
active only in this two cases.
Setting a value between 0.00 and 1.00 it is possible to slow
down the instrument action during set point approach.
Setting
Fuoc = 1
this function is disabled.