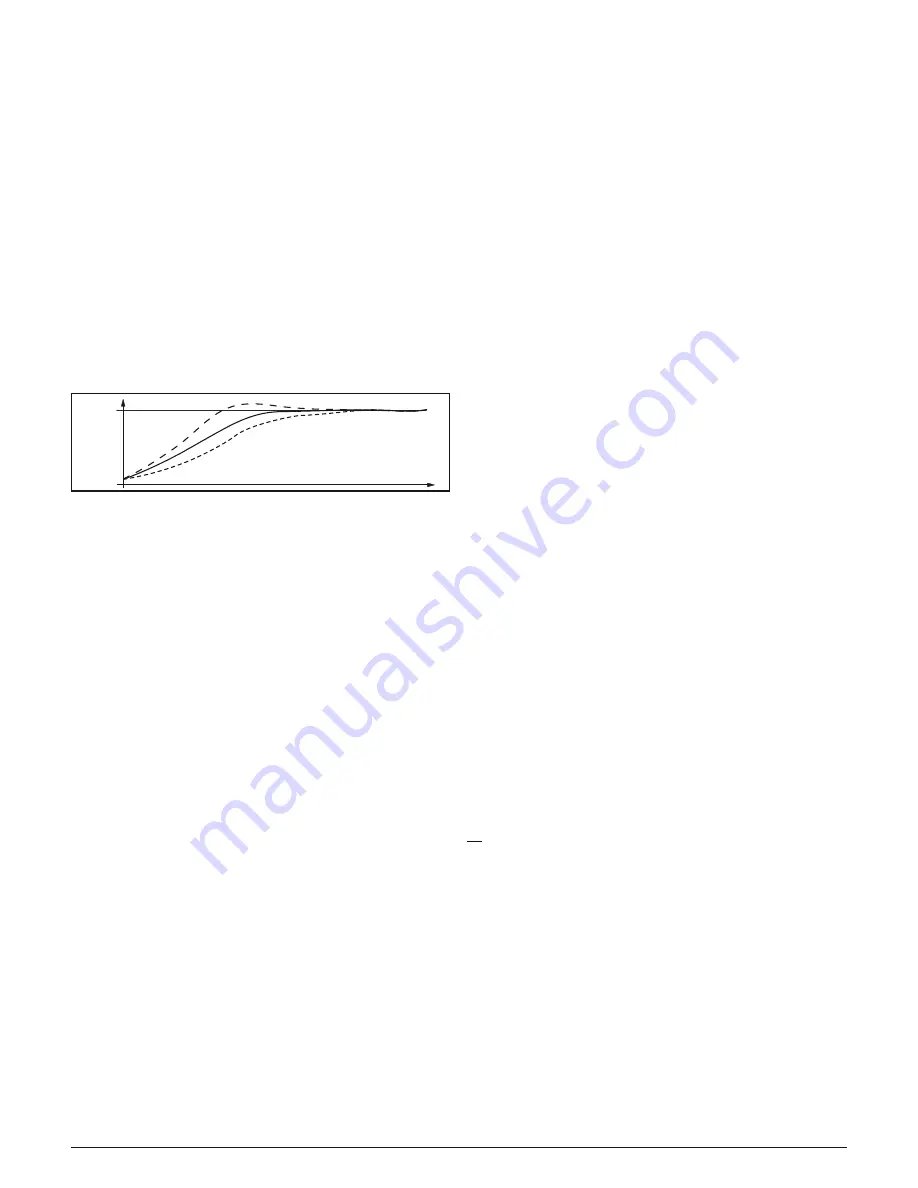
Ascon Tecnologic - K Series - ENGINEERING MANUAL - Vr. 9.0
PAG. 14
[59] int - Integral time
Available:
When [52] cont = PID and [55] SELF = no.
Range:
OFF = Integral action excluded;
1... 9999 seconds;
inF= Integral action excluded.
Note:
Auto-tune functions calculate this value.
[60] dEr - Derivative time
Available:
When [52] cont = PID and [55] SELF = no.
Range:
oFF = Derivative action excluded;
1... 9999 seconds.
Note:
Auto-tune functions calculate this value.
[61] Fuoc - Fuzzy overshoot control
This parameter reduces the overshoot usually present at
instrument start up or after a set point change and it will be
active only in this two cases.
Setting a value between 0.00 and 1.00 it is possible to slow
down the instrument action during set point approach.
Setting
Fuoc = 1
this function is disabled.
PV
SP
time
2
1
3
Available:
When [49] cont = PID and [52] SELF = no.
Range:
0... 2.00.
Note:
Fast auto-tune calculates the Fuoc parameter while
the oscillating-tune sets it equal to 0.5.
[62] H.Act - Heating output (H.rEG) actuator
This parameter sets the minimum cycle time of the heating
output.
It aims to respect the minimum cycle time of a specific
actuator in order to ensure a long actuator life.
Available:
When at least one output is programmed in order
to be the heating output (H.rEG), [52] cont = PID
and [55] SELF = no.
Range:
SSr = Solid state relay output;
rELY = Relay or contactor;
SLou= Slow actuator (e.g. burners).
Note:
Setting:
•
SSr no limit is applied to the auto-tune calculation and
[63] tcrH is pre-set equal to 1 second.
•
rELY the limit applied to the auto-tune calculation is equal
to 20 seconds and [63] tcrH is pre-set equal to 20 seconds.
•
SLou the limit applied to the auto-tune calculation is equal
to 40 seconds and [63] tcrH is pre-set equal to 40 seconds.
[63] tcrH - Cycle time of the heating output
Available:
When at least one output is programmed in order
to be the heating output (H.rEG), [52] cont = PID
and [55] SELF = no.
Range: •
When [62] H.Act = SSr: 1.0... 130.0 seconds;
•
When [62] H.Act = reLY: 20.0... 130.0 seconds;
•
When [62] H.Act = SLou: 40.0... 130.0 seconds.
Note:
Auto-tune functions calculate this value but, when
necessary, it is possible to set it manually.
[64] PrAt - Power ratio between heating and
cooling action (relative cooling gain)
The instrument uses the same PID parameter set for heat
and for cool action but the efficiency of the two actions are
usually different.
This parameter allows to define the ratio between the
efficiency of the heating system and the efficiency of the
cooling one.
An example will help us tu explain you the philosophy.
Consider one loop of a plastic extruder.
The working temperature is equal to 250°C.
When you want to increase the temperature from 250 to
270°C (
Δ
20°C) using 100% of the heating power (resistor),
you will need 60 seconds.
On the contrary, when you want to decrease the temperature
from 250 to 230°C (
Δ
20°C) using 100% of the cooling power
(fan), you will need 20 seconds only.
In our example the ratio is equal to 60/20 = 3 ([60] PrAt = 3)
and says that the efficiency of the cooling system is 3 times
more efficient than the heating one.
Available:
When two control action are programmed (H.rEG
and c.rEG) and [52] cont = PID and [55] SELF = no.
Range:
0.01... 99.99.
Note:
Auto-tune functions calculate this value.
[65] c.Act - Cooling output (C.rEG) actuator
Available:
When at least one output is e programmed in
order to be the cooling output (c.rEG),
[52] cont = PID and [55] SELF = no.
Range:
SSr =
Solid state relay output;
rELY = Relay or contactor;
SLou = Slow actuator (e.g. compressors).
Note:
For more details see [62] h.Act parameter.
[66] tcrc - Cycle time of the cooling output
Available:
When at least one output is programmed in order
to be the cooling output (c.rEG),
[52] cont = PID and [55] SELF = no.
Range: •
When [65] c.Act = SSr: 1.0... 130.0 s;
•
When [65] c.Act = reLY: 20.0... 130.0 s;
•
When [65] c.Act = SLou: 40.0... 130.0 s.
Note:
Auto-tune functions calculate this value but, when
necessary, it is possible to set it manually
[67] rS - Manual reset (integral pre-load)
rS
allows to drastically reduces the undershoot due to a
hot restart. When your process is steady, the instrument
operates with a steady power output (e.g. 30%).
If a short power down occurs, the process restarts with a
process variable close to the set point while the instrument
starts with an integral action equal to zero.
Setting a manual reset equal to the average power output
(in our example 30%) the instrument will start with a power
output equal to the value it will use at steady state (instead
of zero) and the undershoot will become very little (in theory
equal to zero).
Available:
When [52] cont = PID and [55] SELF = no.
Range:
-100.0... 100.0%.