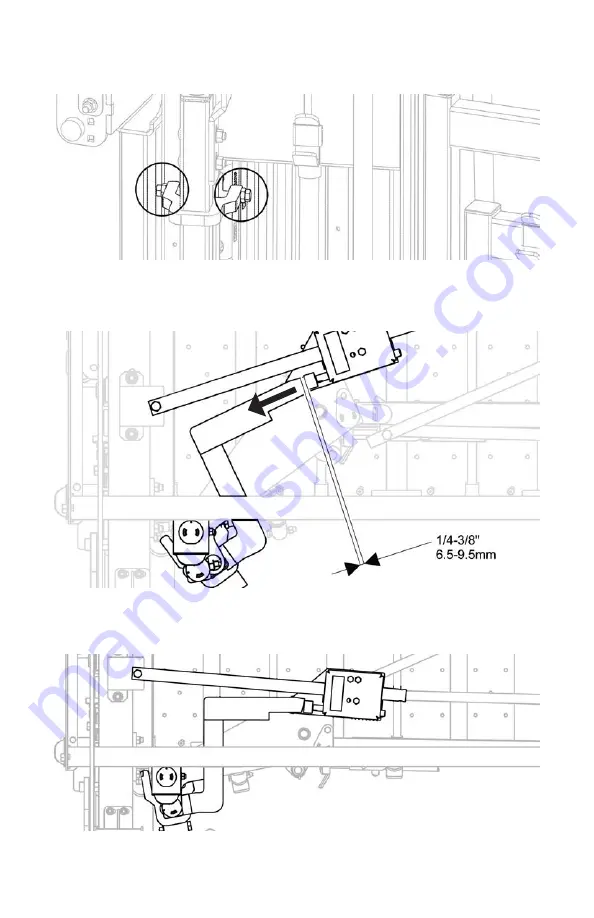
2. Adjust the squeeze lock settings.
a. Loosen jam nuts, and back out front and rear bolts.
b. Push/pull the squeeze handle to get a visual of the release pin.
c. Apply inward pressure on the squeeze handle. Adjust rear bolt until there is 1/4" - 3/8" gap
between the fandangle and release pin.
d. Apply outward pressure on the squeeze handle. Adjust the front bolt until the fandangle
presses the lock box release pin 1/4" - 3/8" in towards the lock box, which will release the
lock mechanism and allow the squeeze to open fully.
RECOMMENDED MAINTENANCE | 44
Summary of Contents for MOBILE Q-CATCH 7408
Page 2: ......
Page 39: ...3 Slide Scale Platform underneath SCALE PLATFORM INSTALLATION 36 ...
Page 51: ......