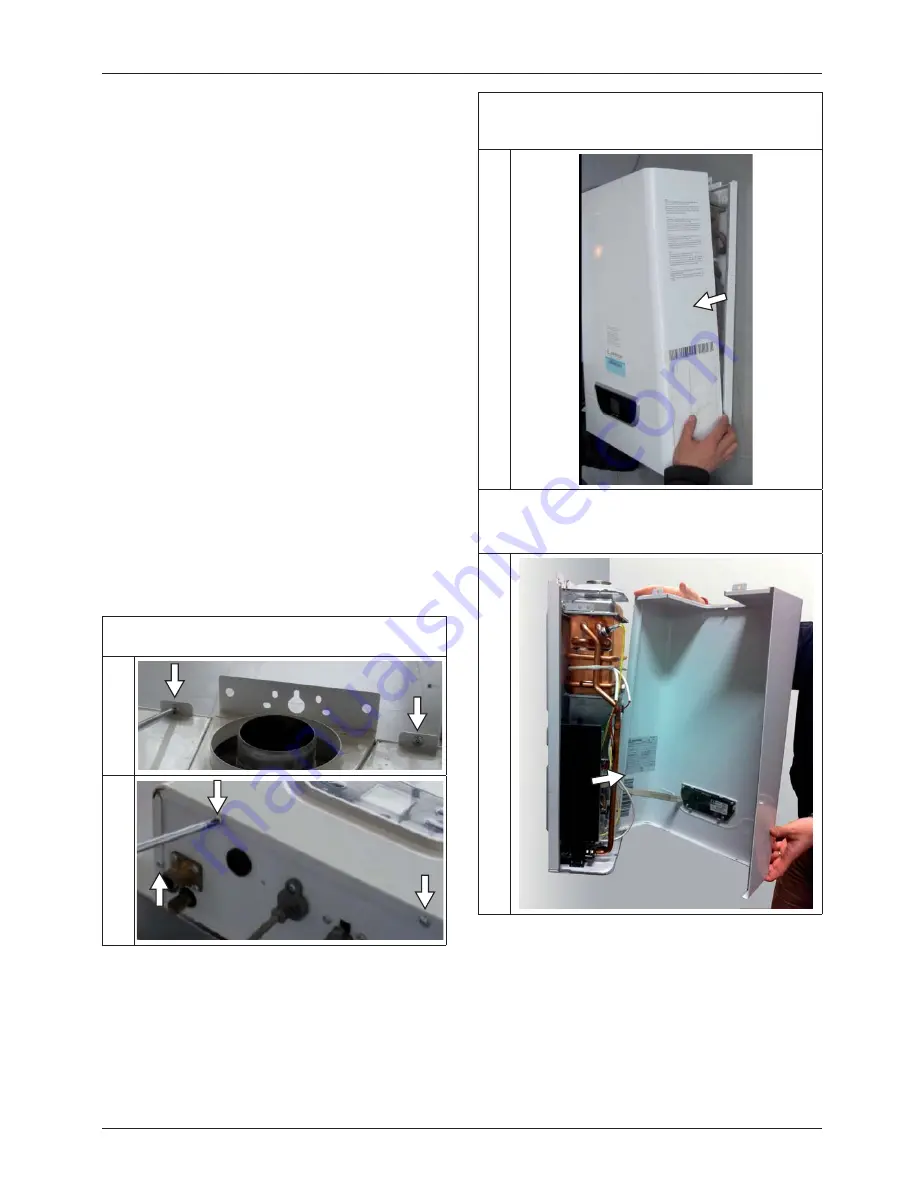
24
6. maintenance
9.
A reading less than or equal to 0.008 following a service is
a good indication that an appliance is operating safely and
will continue to operate until the next planned service
date. Even though the reading is above the 0.004 trigger
value;
10. For readings greater than 0.008, additional checks should
be carried out to ensure that the appliance is assembled,
cleaned and operating as expected (see action points
below).
A
CTION
P
OINTS
Check for the following
:
- Operating pressure at the gas meter
- Appliance operating burner pressures (high and
low)
- Verify the gas rate at the meter test dial
- Burner clean, correctly assembled and positioned
- Clean injectors and check correct size
- Burner for damage
- Heat exchanger clean, fi ns are clean and unblocked
- No combustion products are recirculating causing
vitiation
6.1.1 Replacement of parts
The life of individual components vary and they will need
servicing or replacing as and when faults develop.
The fault fi nding sequence chart in
Section 6.4
will help to
locate which component is the cause of any malfunction, and
instructions for removal, inspection and replacement of the
individual parts are given in the following pages.
6.1.2 To Gain General Access
1.
Release the 2 screws above and 4 screws below, to
remove the front cover.
A
B
2.
Remove the front cover.
Pay attention to disconnect the display from the
main PCB at the main PCB.
C
3. Important!!
Disconnect the connection cable at the main PCB
and remove the front panel
D