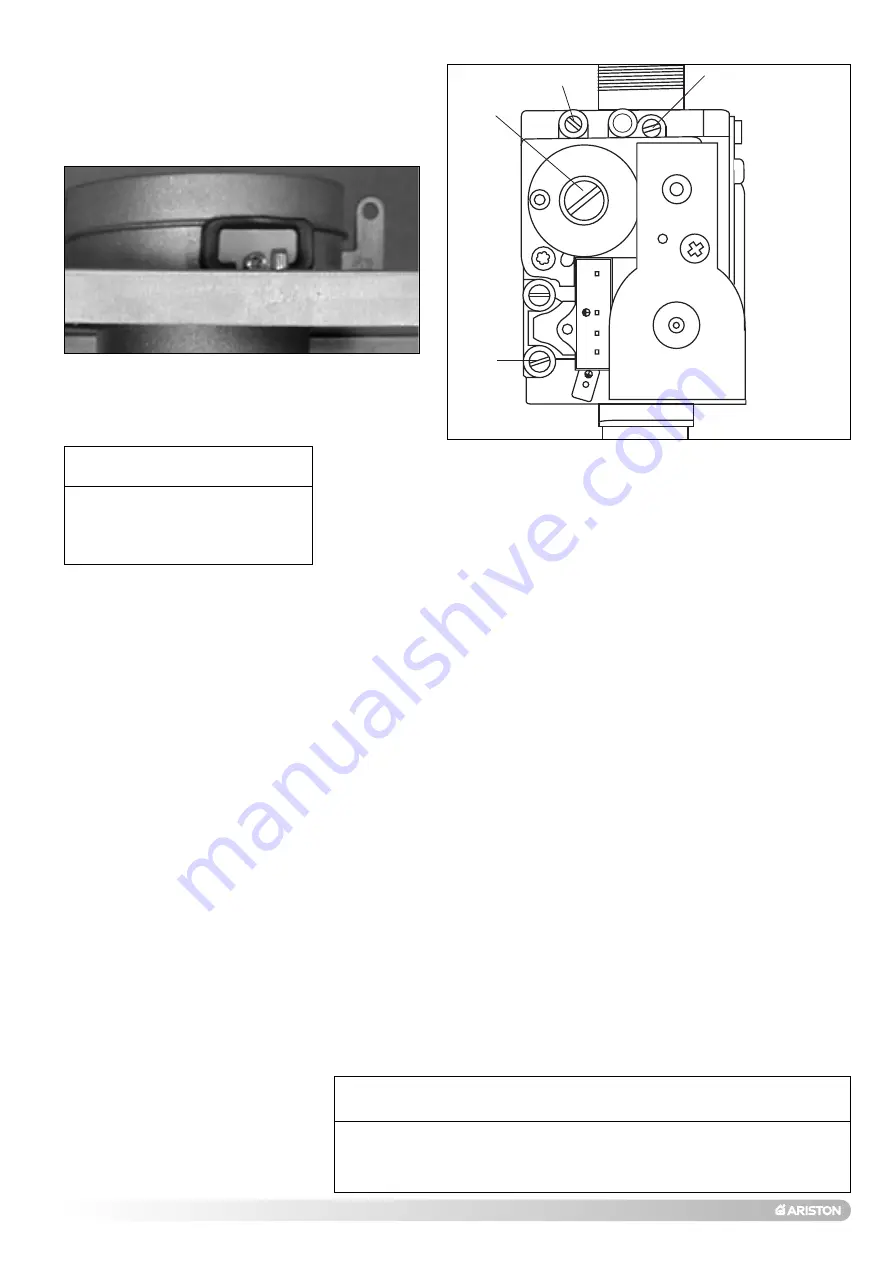
A
IR
/
GAS RATIO SETTING
Calibration values check
methane G20
% vol
10 ±0.2
CO
2
at minimum power
butane
G30
% vol
11.5 ±0.2
after 4 minutes of operation
propane G31
% vol
11.5 ±0.2
Supply pressure
G20 methane
17-25 mbar
G30 butane
25-35 mbar
G31 propane
25-45 mbar
24
13
24
2
4
3
1
3.6.4 G
AS REGULATION CHECK
Supply pressure check
1. Loosen screw “1” (Fig. 3.12) and insert the pressure gauge connection pipe into
the pipe tap.
2. Turn the boiler on at maximum power, enabling the “flue sweep” function (press the
Comfort key “K” for 5 seconds). The supply pressure should correspond to that
foreseen for the type of gas the boiler is designed for (See table 4C).
3. When the check is over, tighten screw “1” and make sure it is securely in place.
4. Disable the flue sweep function by pressing the reset key “H”.
Air/gas ratio at minimum power
To check the air/gas ratio at minimum power, proceed as follows:
1. Connect the combustion analyser to the analysis point (Fig. 3.11) after removing
the cover plate.
2. Turn the boiler on at minimum power via the test function (see paragraph 3.6.1) or
by pressing keys “K” and “H” simultaneously on the control panel. Ensure the CO
2
value on the analyser corresponds with the value indicated in table 4D. If this is not
the case, adjust screw “2” with a screwdriver, after removing the cap, until you
obtain the correct CO
2
reading. Allow the reading to become stable for at least 4
minutes.
3. When the check is over, replace the cap on screw “2” (Fig. 3.11).
4. Disable operation at minimum power by pressing key “H”.
Air/gas ratio at maximum power
To check the air/gas ratio at maximum power, proceed as follows:
1. With the combustion analyser already connected to the analysis point, set the
boiler to maximum power via the test function (see paragraph 3.6.1) or enabling
the “flue sweep function” by pressing the Comfort key “K” for 5 seconds.
Ensure the CO
2
value on the analyser corresponds with the value indicated in
table 4D. If this is not the case, adjust screw “4” with a screwdriver (Fig. 3.12), until
you obtain the correct CO2 reading. Allow the reading to become stable for at least
4 minutes.
2. Disable the “flue sweep function” by pressing key “H”.
The “flue sweep function” is automatically disabled after 5 minutes.
3. Repeat the air/gas ratio at minimum power check (see above).
4. Disconnect the analyser, remount the cover plate and check it is securely in place.
A
IR
/
GAS RATIO CHECK
F
IG
. 3.11
F
IG
. 3.12