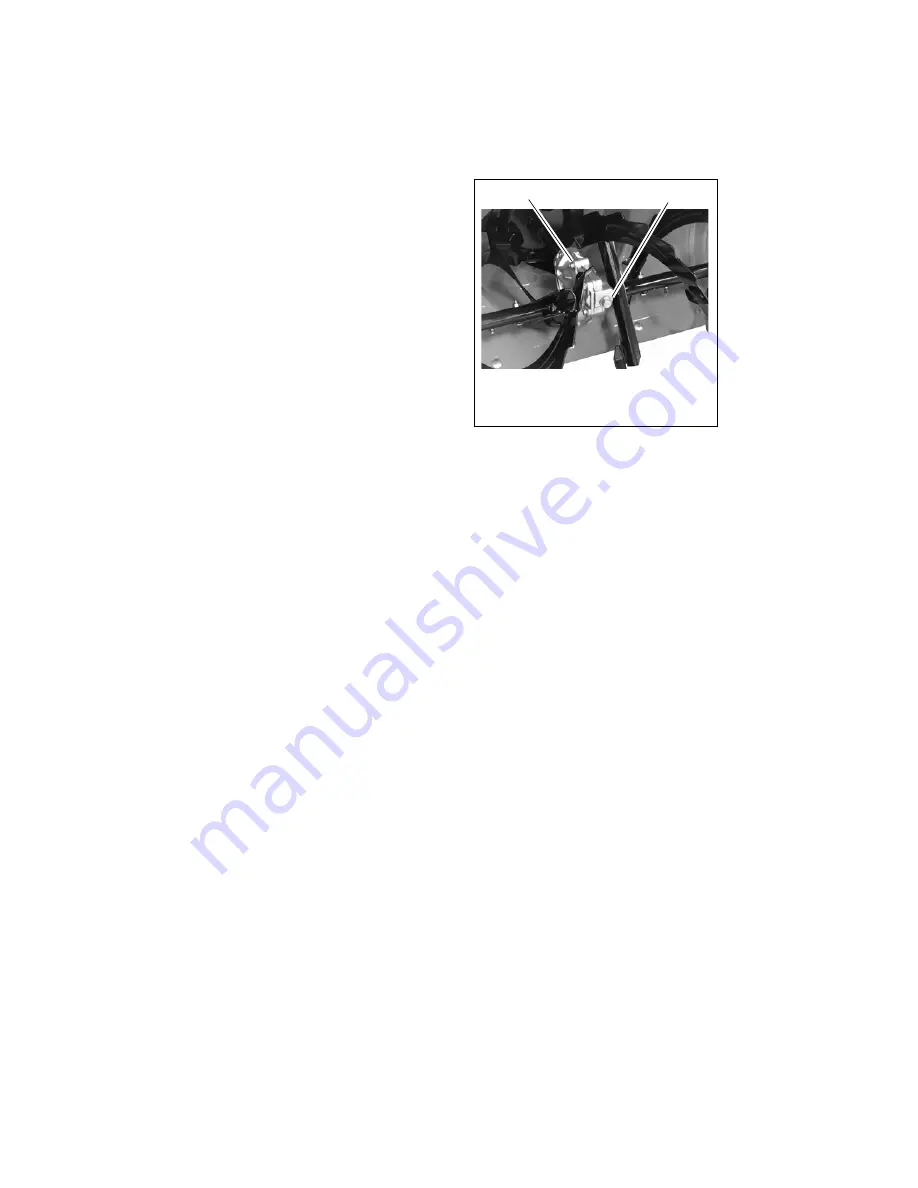
GB - 19
CHECK CLUTCH OPERATION
Auger and impeller must stop within 5
seconds when attachment clutch/impeller
brake lever is released.
Wheels must stop quickly when traction drive
clutch lever is released.
If clutches do not engage or disengage
properly, adjust or repair before operation
(see
Attachment Clutch/Brake Adjustment
CHECK CLUTCH SPRING
ADJUSTMENT
Make sure the attachment clutch and traction
drive clutch are adjusted to the range
specified in
CHECK TIRE PRESSURE
Keep tires at pressure listed on the tire
sidewall. (see
CHECK AUGER GEARCASE
IMPORTANT:
Proper oil level must be
maintained.
Gear cases are filled to the correct level at
the factory. Unless there is evidence of
leakage, no additional lubricant should be
required. Check oil level each season or
every 25 hours of operation.
To ensure adequate lubricant level:
1. Remove filler plug (Figure 16). Lubricant
must be at least up to bottom of lubricant
filler hole with unit resting on a level
surface.
2. Add lubricant if required. Allow oil to
drain to level of plug and replace plug.
IMPORTANT:
Use only Ariens special gear
lubricant L-2 (Part Number 00008000).
Gearcase filler plug may require an
application of Loctite® 565 thread sealant
with repeated servicing.
GENERAL LUBRICATION
IMPORTANT:
Wipe each fitting clean before
and after lubrication. Do not wipe gearcase
filler plug; wiping the gearcase filler plug may
remove thread sealant and cause leaks.
IMPORTANT:
DO NOT allow grease or oil to
get on friction disc, friction plate or belts.
NOTE:
Apply Ariens Hi-Temp Grease or
equivalent to the lubrication fittings. See
.
Sno-Thro should be lubricated (Figure 17) at
beginning of season or every 25 operating
hours.
Auger Shaft
NOTE:
To grease auger shaft, remove shear
bolt nuts, and shear bolts. Apply grease at the
grease zerks and then turn the auger
assemblies on the auger shaft. Replace
shear bolts per instructions in
Figure 16
1. Auger Gearcase
2. Filler Plug
OS2600
Summary of Contents for 916003
Page 35: ......