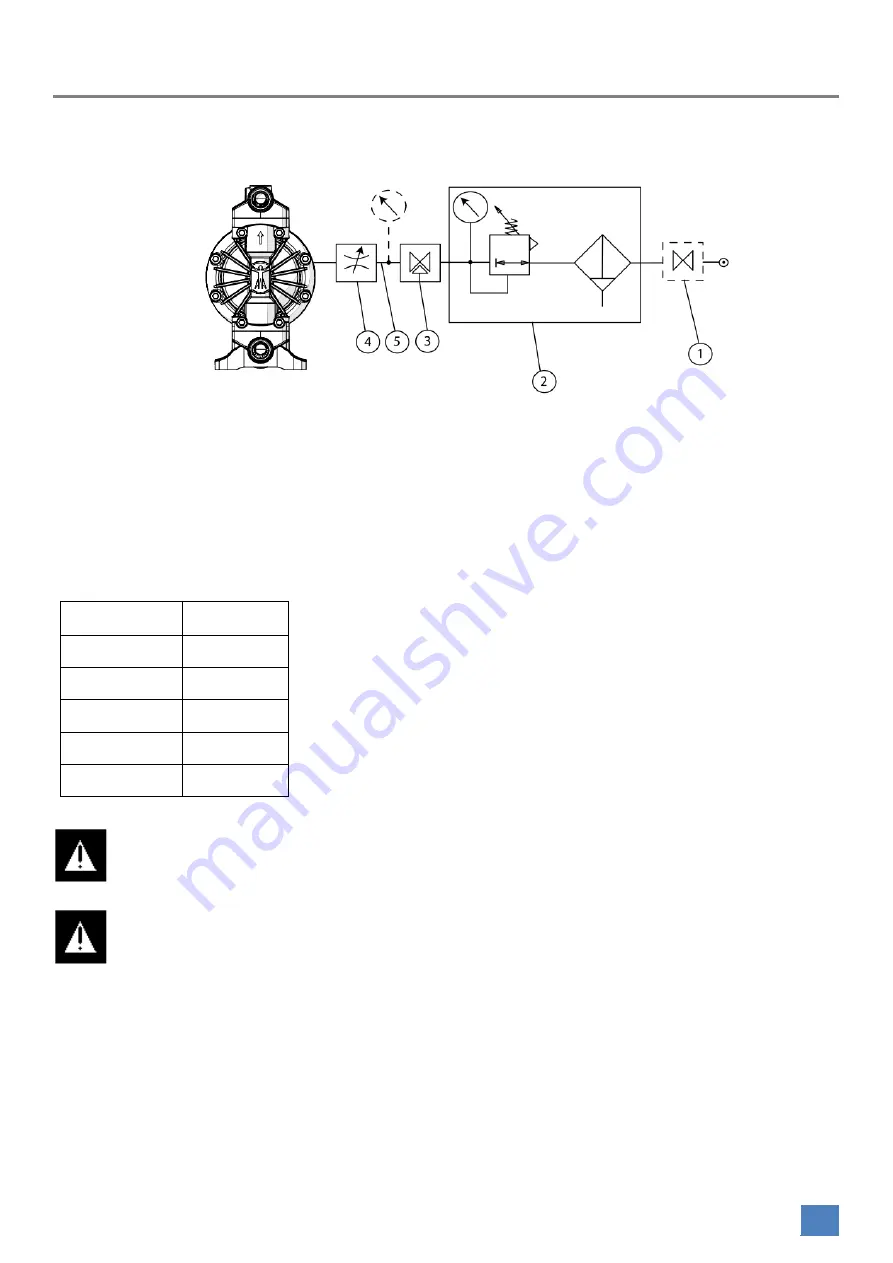
Operations & maintenance manual – ASTRA evo (DDE)
ARGALAIR 2020 | Rev. 6
15
6.
Fittings;
ARGAL AIR REGULATION KIT
The devices n° 2, 3, 4, 5 and all necessary fittings are included in the
ARGAL Air regulation KIT
, supplied by
ARGAL upon request as an accessory. The device n° 1 (On-off valve) is in charge of the customer/installer.
The maximum air feeding pressure for the ASTRA evo pumps is
8 bar
. Higher air pressure can damage the
pump and may cause injury to personnel in vicinity of the pump. The minimum air feeding pressure is
2 bar
.
Compressed air supply pipes:
minimum EXTERNAL dimensions
are reported in the following table.
The maximum length of pipes may be
5m.
MODEL
Ø
air pipe
DDE 030
Ø 6 mm
DDE 060
Ø 8 mm
DDE 100 - 160
Ø 10 mm
DDE 400
Ø 12 mm
DDE 650
Ø 14 mm
Table 5
WARNING:
if head and capacity must be high there is the risk that ice accumulates in high
quantity and the pump stops. To avoid this, it is very important to maintain the air quality as
prescribed within this Manual.
WARNING
: ice may form into the pneumatic exchanger:
SCRUPULOUSLY FOLLOW THE
INSTRUCTIONS WRITTEN IN THIS PARAGRAPH, TO PREVENT THE ICE FORMATION.
0.6.3 OPERATING PRINCIPLE
The
ASTRA evo
pumps are volumetric.
The suction and discharge cycles are simultaneous at alternating phases.
The operating principle concern the VOLUME VARIATION of two chambers. As shown in the scheme below,
while in a chamber a positive volume variation is observed that correspond to a pressure decrease, in the
second one there is a reduction in volume and therefore an increase in pressure occurs. This causes an
aspiration and a thrust on the fluid respectively.
The operation described above is regulated by the VALVES BALL installed on the ASTRA DDE pumps. The
valves open due to the difference in pressure between the two environments that separate, allowing the
passage of the fluid.
Summary of Contents for ASTRA Evo DDE 030
Page 8: ...Operations maintenance manual ASTRA evo DDE ARGALAIR 2020 Rev 6 8 ...
Page 33: ...Operations maintenance manual ASTRA evo DDE ARGALAIR 2020 Rev 6 33 WR_ FC_ AL_ SS_ SP_ ...
Page 49: ...Operations maintenance manual ASTRA evo DDE ARGALAIR 2020 Rev 6 49 ...
Page 50: ...Operations maintenance manual ASTRA evo DDE ARGALAIR 2020 Rev 6 50 WR_ FC_ AL_ ...
Page 53: ...Operations maintenance manual ASTRA evo DDE ARGALAIR 2020 Rev 6 53 SS_ SP_ WR_ FC_ AL_ K1 K3 ...
Page 55: ...Operations maintenance manual ASTRA evo DDE ARGALAIR 2020 Rev 6 55 DDE 030 DDE 060 DDE 100 ...
Page 60: ...Operations maintenance manual ASTRA evo DDE ARGALAIR 2020 Rev 6 60 ...
Page 61: ...Operations maintenance manual ASTRA evo DDE ARGALAIR 2020 Rev 6 61 ...