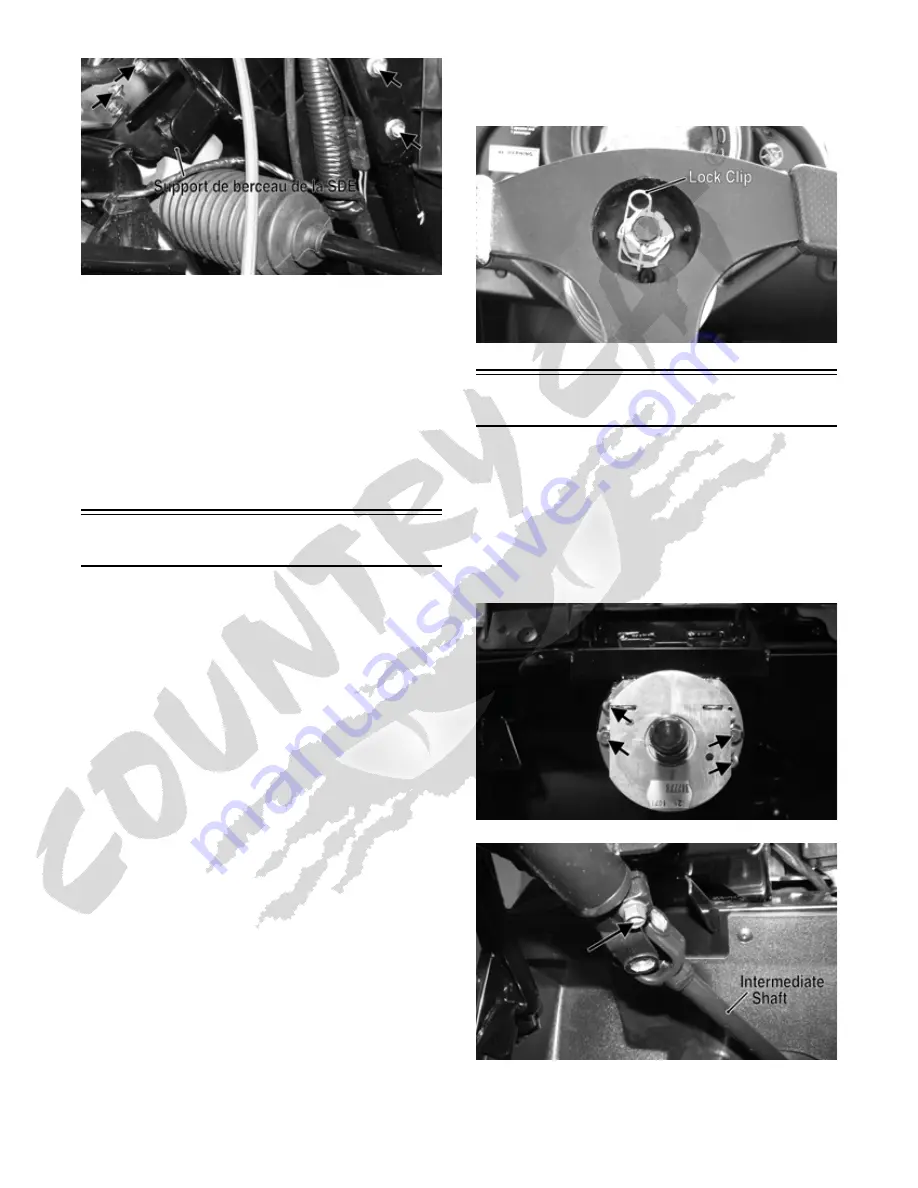
140
PR773A
3. Place the tie rod ends into the knuckles and secure
with the castle nuts (coated with red Loctite #271).
Tighten to 30 ft-lb; then install new cotter pins.
NOTE: If the slots in the castle nut are not
aligned with the hole in the tie rod end, tighten
until the cotter pin can be installed.
4. Install the EPS assembly (see Installing EPS Assem-
bly sub-section in this section); then tighten the cap
screws (from step 2) to 20 ft-lb.
5. Install the wheel and tighten to 80 ft-lb.
Steering Wheel
REMOVING
1. Remove the steering wheel cover; then match mark
the steering shaft and steering wheel.
NOTE: Any time steering components are disas-
sembled, all connecting components should be
marked for proper alignment during assembling.
2. Remove the lock clip from the steering shaft; then
remove the nut securing the steering wheel and
remove the steering wheel.
INSPECTING
1. Inspect the steering wheel for cracks, missing pad-
ding, or broken spokes.
2. Inspect the splines for wear.
3. Check that the steering wheel is not bent.
INSTALLING
1. Install the steering wheel aligning the two match
marks; then apply a drop of red Loctite #271 to the
threads of the nut and secure the steering wheel.
Tighten to 25 ft-lb.
NOTE: If a new steering wheel is being installed,
mark the wheel as close as possible to the old
wheel mark; then check for proper positioning with
the front wheels straight forward.
2. Install the lock clip on the steering shaft.
NOTE: If the hole in the steering shaft does not
align with the slots in the castle nut, tighten the
nut slightly until the next slot aligns with the hole.
HDX131A
Upper Steering Shaft
REMOVING
1. Remove the dashboard (see Dashboard in this sec-
tion).
2. Remove the four cap screws and nuts securing the
steering shaft housing to the steering support; then
remove the cap screw securing the intermediate shaft
yoke to the steering shaft.
PR764A
PR765A
3. Remove the steering shaft housing and shaft from the
steering support and intermediate shaft; then remove
the intermediate shaft from the EPS input shaft.