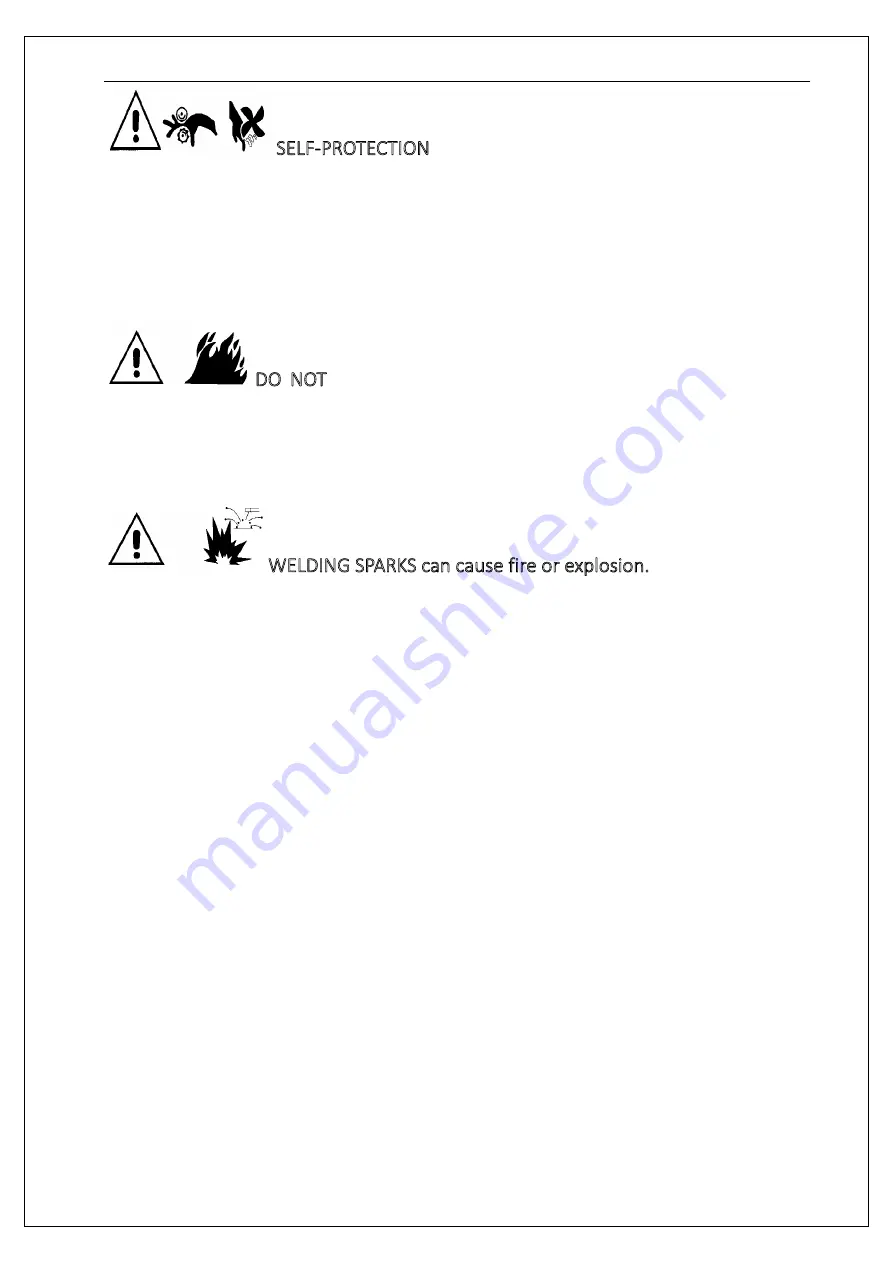
SELF-PROTECTION
Keep all equipment safety guards, covers and devices in position and in good repair. Keep
hands, hair, clothing and tools away from V-belts, gears, fans and all other moving parts when
starting, operating or repairing welding equipment.
Do not put your hands near the engine fans. Do not attempt to override the governor or idler
by pushing on the throttle control rods while an engine is running
.
DO NOT
add fuel near an open flame welding arc or when engines are
running. Stop the engine and allow it to cool before refueling to prevent spilled fuel from
vaporizing on contact with hot engine parts and igniting. Do not spill fuel when filling tank. If fuel
is spilled, wipe it up and do not start engine until fumes have been eliminated.
WELDING SPARKS can cause fire or explosion.
Remove fire hazards from the welding area. If this is not possible, cover them to prevent the
welding sparks from starting a fire. Remember that welding sparks and hot materials from
welding can easily go through small cracks and openings to adjacent areas. Avoid welding near
hydraulic lines. Have a fire extinguisher readily available.
Where compressed gases are to be used at the job site, special precautions should be used to
prevent hazardous situation.
When not welding, make certain no part of the electrode circuit is touching the work or ground.
Accidental contact can cause overheating and create a fire hazard.
Do not heat, cut or weld tanks, drums or containers until the proper steps have been taken to
ensure that such procedures will not cause flammable or toxic vapors from substances inside.
They can cause an explosion even though they have been “cleaned”.
Vent hollow castings or containers before heating, cutting or welding. They may explode.
Sparks and spatter are thrown from the welding arc. Wear oil free protective garments such as
leather gloves, heavy shirt, cuff less trousers, high shoes and a cap over your hair. Wear ear plugs
when welding out of position or in confined places. Always wear safety glasses with side shields
when in a welding area.
•
Connect the work cable to the work as close to the welding area as practical. Work cables
connected to the building framework or other locations away from the welding area increase
Summary of Contents for ARCOSTICK MMA 180
Page 1: ......
Page 24: ...21 5 3 Electrical principle drawing 180 system chart ...