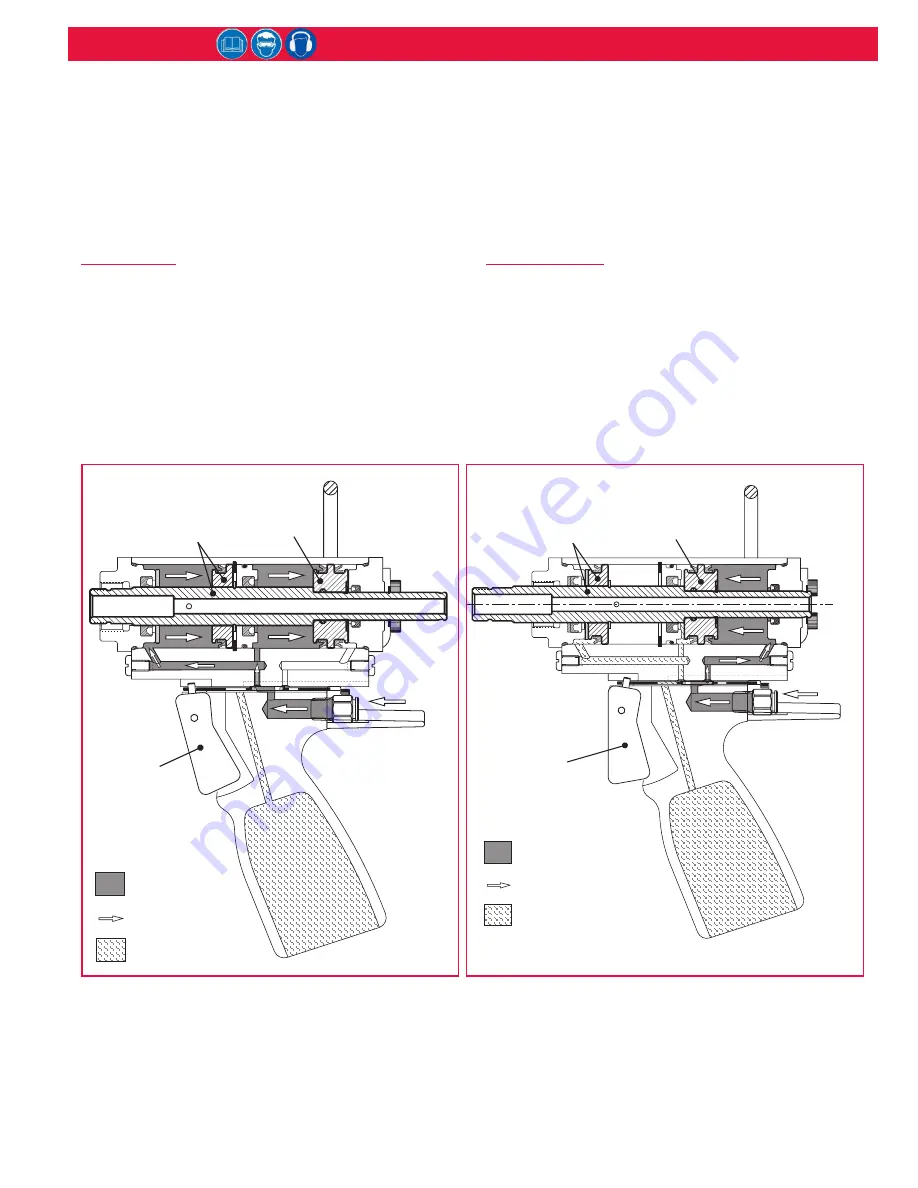
5
ERT7 and ERT8 Ebbert Rivet Tools (HK1061
)
PULL CYCLE
When the trigger is pressed, the incoming non-oiled
plant air, regulated at 90 psi forces the Piston Assembly
and Double Piston to the rear of the tool, and air is
exhausted out the bottom of the tool. The fastener is
installed, and the fastener pintail breaks off.
NOTE
:
The ERT8 exhaust air exits through small holes
in the bottom of the Valve Body. (See Item 16 of ERT8
Assembly Drawing in this manual.)
RETURN CYCLE
When the trigger is released, the pressurized air is
directed to the rear of the pistons, causing them to move
forward. The fastener pintail is vacuumed out the rear
of the tool and into the Power Unit Pintail Collection bin,
and the tool is ready for the next fastener installation.
This manual contains operating and service procedures
for the Ebbert Rivet Tool models ERT7 and ERT8. Pay
close attention to the recommended service procedures
in this manual.
Specific instructions for each tool are given under that
tool model number heading. While the tools appear
similar, each tool contains parts not used on other
models, and removal and replacement methods may
vary.
General Information
Principle of Operation