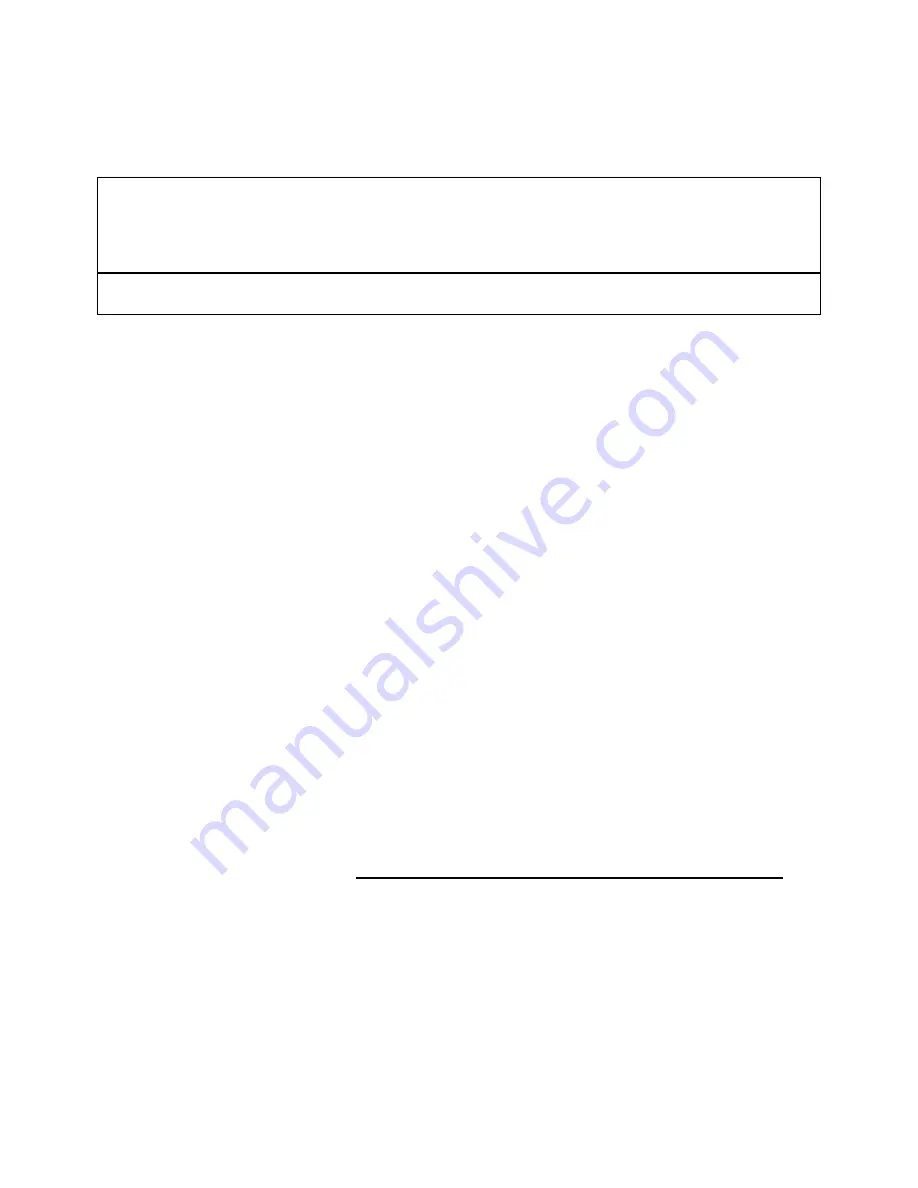
20
4.4 Welding Operation
4.4.1. Recommendations for E70S-3 Spray Transfer
Wire
Range 2
Current
Wire Feed
Voltage
Diameter
Power
(A)
Speed
(V)
(inches)
Setting
(IPM)
.035
50-100
180-290
350-450
25-28
.045
60-100
200-300
250-450
25-28
*
Using 98/2 AR0O2 shielding gas. The recommended power and range settings represent the
manufacturer’s best estimate and are intended only as guidelines for the Workhorse 300MS
.
4.4.2 Short Circuit Transfer/Short Arc
The Migweld 300MS
achieves the short circuit transfer by precisely controlling the instantaneous
power output during alternating arcing and shorting periods. An internal control circuit monitors
the output voltage to detect the shorted condition and reacts to increase the arc current during
the shorted time. This heats the filler metal in contact with the base material to the melting point;
the molten filler flows in the base, the short circuit condition ends and a period of arcing begins
again. During arcing, the increase in arc voltage is detected by the internal control which acts to
limit the arc current until a short circuit is once again detected, beginning another cycle.
4.4.3. Stick Welding
All secondary outputs must be connected to output terminals of the power source
After the primary input connections have been made, close the main wall disconnect switch or
circuit breaker. Place the primary power selector in the ON position. This will turn on the control
circuitry. The Power-On light on the front panel will be lit. Turn the Mode Selector in the ‘Stick’
position. The welding output will be energized and the electrode holder will become “electrically-
hot”. Turn the Arc Force Control Selector in its mid position. Adjust the Weld Power Control to
fit the type and diameter of electrode to be used, as recommended by the electrode
manufacturer.
4.5 Dual Voltage Changeover
Prior to changing voltage, the unit
MUST BE SWITCHED OFF FOR AT LEAST 2 MINUTES
.
This will give time for the capacitors to discharge. The Wo is equipped with a protection
device to prevent an overvoltage condition. If the unit is configured for 240V (horizontal slot) and
connected to a 480V supply, the circuit breaker switch will trip, disconnecting the overvoltage.
DO NOT ALLOW THIS CONDITION TO BE REPEATED MORE THAN 10 TIMES. Warranty will
be voided if the unit is exposed to excessive overvoltage trip sequence.
The Dual Voltage (240/480V) Workhorse 300MS machine uses a switch similar to the range
switch is used to change between the two voltages, 240V and 480V. The switch changes the
power capacitors, the main transformer and the auxiliary transformer when the switch shaft is
rotated 90 degrees. The opening exposing the switch shaft is located at the rear panel to the
right of the primary cable. ( See Figure 4)
Summary of Contents for 10310
Page 26: ......
Page 27: ......
Page 28: ......
Page 29: ...1 of 1 ...
Page 30: ...1 of 1 ...
Page 31: ...1 of 1 ...