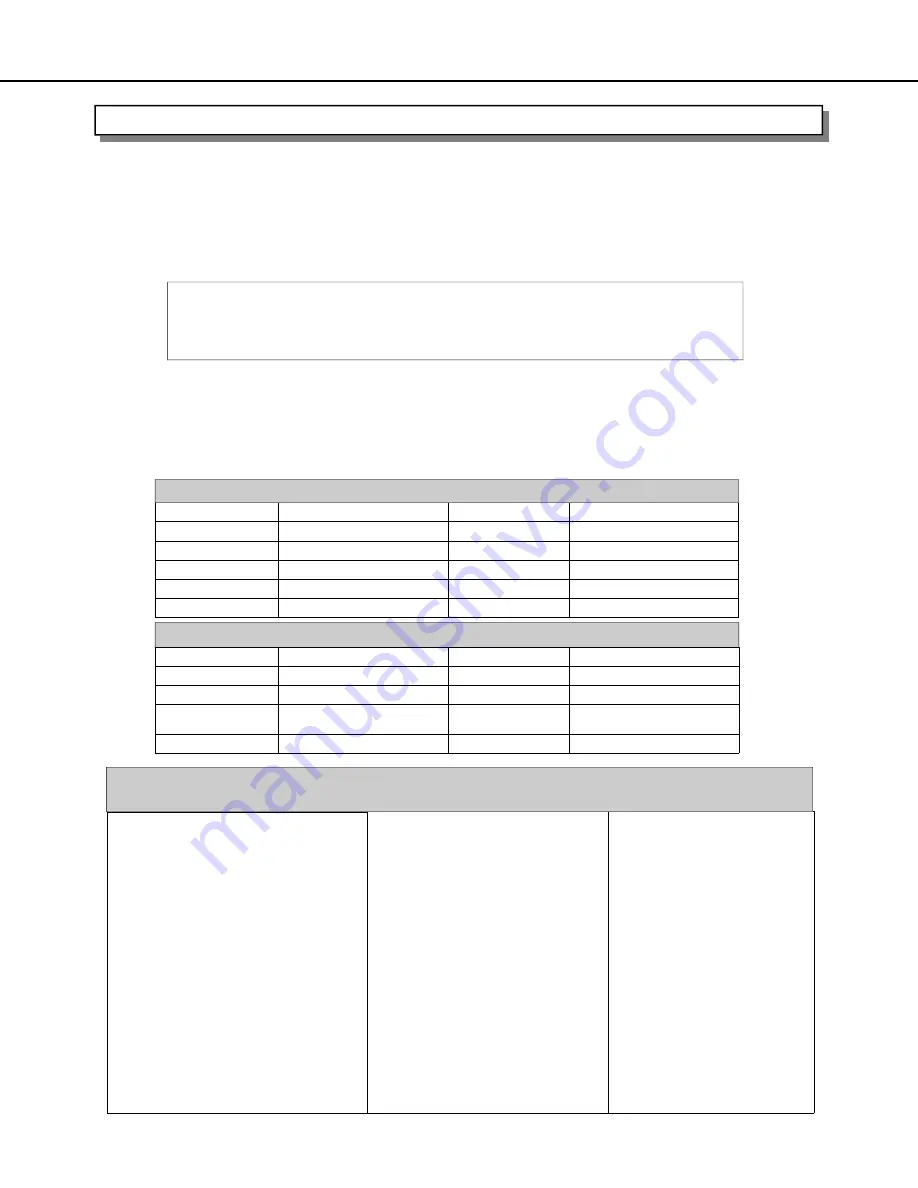
Optima 70 - 2
21
VENTING - HORIZONTALLY USING SIMPSON DURA-VENT DIRECT VENT SYSTEMS
The Optima 70 can be vented horizontally using Simpson Dura-Vent Direct Vent System. To vent using
Simpson Dura-Vent exclusively, you must use the Archgard SDA-3 Adaptor and connect the SDA-3 adap-
tor to the top of the Optima 70 as shown in Fig. 1. NOTE: Apply high temperature sealant to the SDA-3
adaptor and the flue connection on the Optima 70. Seal all pipe joints and follow all venting instructions
within this manual.
NOTE: Call your local Authorized Archgard Dealer to purchase Simpson Dura-Vent Direct Vent Kits and/
or venting components.
Wall Thickness (inches)
Vent Length Required (inches)
Wall Thickness (mm)
Vent Length Required (mm)
4” - 5-1/2”
6”
101 mm - 140 mm
152 mm
7” - 8-1/2”
9”
178 mm - 216 mm
228 mm
10” - 11-1/2”
12”
254 mm - 292 mm
305 mm
9” - 14-1/2”
11” - 14-5/8” Adj. Pipe
228 mm - 368 mm
228 mm - 371 mm
15” - 23-1/2
17” - 24” Adj. Pipe
381 mm - 597 mm
432 mm - 610 mm
Flat Wall Installation
Wall Thickness (inches)
Vent Length Required (inches)
Wall Thickness (mm)
Vent Length Required (mm)
3-1/4” - 6-3/4”
11” - 14-5/8” Adj. Pipe
82 mm - 171 mm
228 mm - 371 mm
7-3/4” - 16-1/4”
17” - 24” Adj. Pipe.
197 mm - 412 mm
432 mm - 610 mm
7-1/4” - 8-3/4”
6” + 12”
Or 9” + 9”
184 mm - 222 mm
101 mm + 305 mm
Or 228 mm + 228 mm
4-1/4” - 5-3/4”
6” + 9”
108 mm - 146 mm
152 mm - 228 mm
Corner Installations
Measure wall thickness from the back of the fireplace standoffs to the inside mounting surface of the ter-
mination cap. If a Vinyl siding standoff is required, measure to the outside surface of the wall without
siding and add 2” (50mm).
NOTE: The Termination cap must NOT be recessed into siding. Measure wall thickness including finish-
ing straps.
Minimum components required for horizontal termination using Simpson Dura-Vent:
1 SDA-3 (Appliance adaptor) 1 90 Deg. Elbow
1 Horizontal Termination Cap 1 Wall Thimble
1 Length of pipe for top of appliance 1 Length of pipe to suit wall thickness
Part #
Description
971
Horiz. Term. Kit Includes; 90
0
. Blk elbow, wall thimble
cover, Horiz. square term. Cap, 24” (610 mm) blk pipe
and 11”-14” (279 mm x 356 mm) adj. blk pipe.
970
Basic Horiz. Term. Kit Includes; 90
0
. blk elbow, wall
thimble cover, Horiz. square term. cap.
987
Vertical Termination Kit Includes;
0/12- 6/12 pitch adj. flashing, storm collar, low profile
term. cap.
908B
6” (152 mm) Pipe Length - Black
907B
9” (228 mm) Pipe Length - Black
906
12” (305 mm) Pipe Length - Galv.
906B
12” (305 mm) Pipe Length - Black
904
24” (610 mm) Pipe Length - Galv.
904B
24” (610 mm) Pipe Length - Black
903
36” (914 mm) Pipe Length - Galv.
903B
36” (914 mm) Pipe Length - Black
Part #
Description
902
48” (1.22 M) Pipe Length - Galv.
902B
48” (1.22 M) Pipe Length - Black
911B
11” - 14-5/8” (228 mm x 371 mm) Adj. Pipe
Length - Black
917B
17”’ - 24” (432 mm) x (610mm) Adj. Pipe
Length - Black
945
45
0
Elbow - Galv.
945B
45
0
Elbow - Black
945G
45
0
Elbow - Swivel - Galv.
945BG
45
0
Elbow - Swivel - Black
990
90
0
Elbow - Galv.
990B
90
0
Elbow - Black
990G
90
0
Elbow - Swivel - Galv.
990BG
90
0
Elbow - Swivel - Black
991
Vertical Termination Cap High Wind
980
Vertical Termination Cap
Part #
Description
984
Horizontal (Square) Termination Cap
985
Horiz. (SQ) Term. Cap. High Wind.
982
Snorkel - 14” (356 mm) Rise Term. Cap
981
Snorkel - 36” (914 mm) Rise Term. Cap
940
Wall Thimble - Support Box
941
Cathedral/Ceiling - Support Box
3951
Brass Trim for Wall Thimble/Ceiling Sup.
963
Firestop Spacer
943
Flashing 0/12 - 6/12
943S
Flashing 7/12 - 12/12
953
Storm Collar
950
Vinyl Siding Standoff
988
Wall Strap
942
Wall Thimble
SIMPSON DURA-VENT DIRECT VENT PARTS LIST 6”-5/8” x 4” (168mm x 101mm)
See your Authorized Archgard Dealer for price and availability.