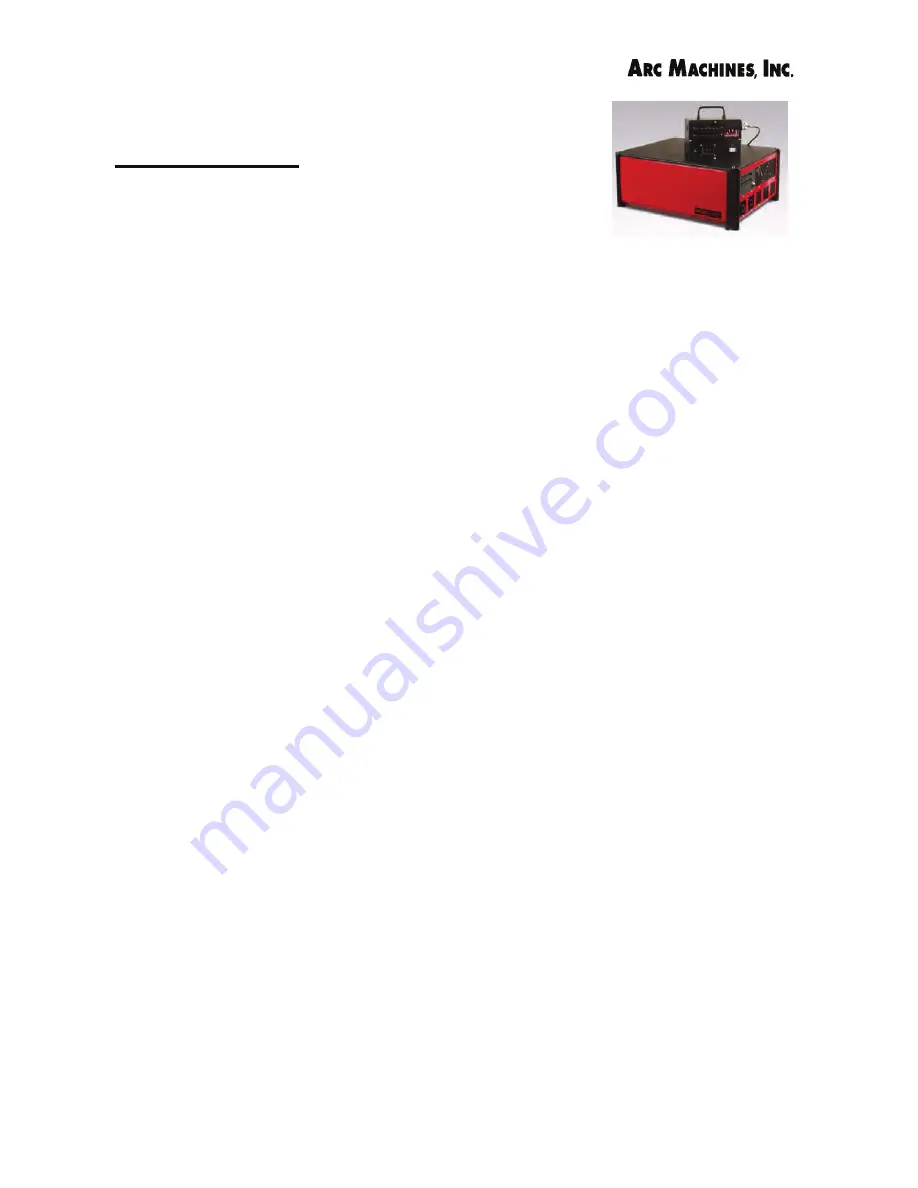
!"#$%&#'()*+,$-)#.$%/0*1$234$5/67("*$8/7*"$9:;;1<
!"#$%&'()*"3)-.//00)))))))))))))))))))))))))))))))D';&G3)H?=&)I
1&23)4
D
';&G
A
AC current
,
1.2
AC voltage
,
1.2
alignment
,
2.4
alignment tools
,
2.4
ANSI-49.1 Safety in Welding and Cutting
,
2.5
Applications
,
1.2
arc blow
,
1.2
arc eye
,
2.3
Arc Starting
,
2.2
Arc Welding Precautions
,
2.1
B
birds nest
,
5.1
bleeder circuit
,
2.2
bypass switch, S2
,
4.3
C
circuit breaker (CB-1)
,
2.4
Circuit Breaker (ON/OFF)
,
4.1
cladding
cladding current
,
5.2
cladding operations
,
6.1
demonstration
,
1.3
cold wire
,
1.1
Connector
,
4.1
constant current mode
,
1.2
Controls
current
,
1.1
voltage
,
1.1
Cooling
water cooling
,
4.1
corrosion resistance
,
1.3
D
deposition rates
,
1.2
,
6.1
digital data acquisition
,
1.4
Don’ts
,
2.4
downhand welding
,
6.1
DO’S
,
2.2
Do’s and Don’ts
,
2.2
drawings
Hotwire Power Supply Basic Assembly
Drawing
,
7.1
Hotwire Power Supply Basic Assembly
Drawing - Page 2.
,
7.2
Hotwire Remote Control Assembly
Drawing
,
7.5
Remote Control Wiring Diagram
,
7.6
501 Hotwire Remote Control Assembly
Draw-
ing
,
7.3
501 Hotwire Wiring Diagram
,
7.4
duplex stainless steels
,
1.3
E
electric shock
,
2.1
external controller
,
4.3
external voltage sensor
,
4.1
external wire feed controller
,
4.2
eye protection
,
2.1
F
facing
,
2.4
fit-up
,
6.1
G
gas cylinders
,
2.4
gas flow rate
,
2.4
ground connection
,
5.1
ground (work) connection
,
2.4
GTAW
GTAW head
,
4.1
GTAW power supply
,
4.2
,
4.3
GTAW process
,
2.2
GTAW torch
,
1.1
,
2.1
GTAW torch cooling
,
4.1
H
HF Arc Start
,
2.2
high amperage
,
4.1
high voltage
,
2.2
high-nickel alloys
,
1.3
hot wire
downhand welding
,
1.3
hot wire AC Current
,
4.1
hot wire current
,
4.3
hot wire GTA welding of pipe
,
6.2
hot wire GTAW
,
1.3
hot wire guide tube
,
5.1
hot wire power
,
5.2
hot wire remote connector pins
,
4.4
hot wire sense
,
5.1
hot wire torch
,
1.3
,
4.1
,
5.1
hot wire tube
,
2.1
hot wire voltage
,
1.2
hot-wire torch
,
1.4
I
Input Power connector
,
4.1
input voltage
,
5.1