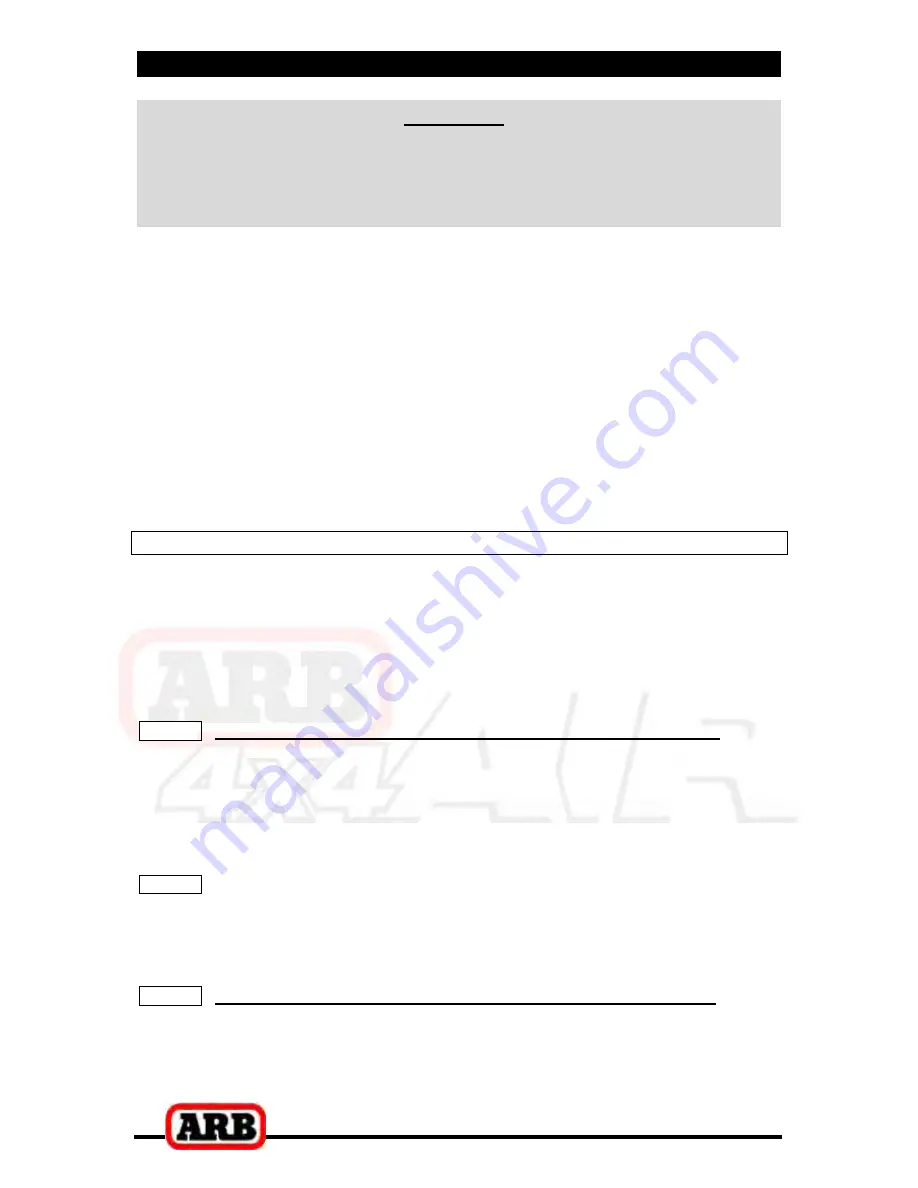
2 Installing the Compressor
6
IMPORTANT :
The installation kit includes 4 hex head bolts, 4 dome head carriage bolts and 4 flat
washers. The hex head bolts and washers are to be used if the tightening is to be
done from the compressor side of the mounting panel. Alternatively, if the nuts are to
be tightened from the backing plate side of the mounting panel then the carriage bolts
can be used as they will not spin in the mounting bracket slots.
F
Assemble the hex bolts and washers OR carriage bolts into the slots of the mounting
bracket.
F
Align the bolts in the mounting bracket with the newly drilled holes in the panel and then
sit the compressor assembly in place.
F
Assemble the backing plate onto the protruding bolts from the opposite side.
F
Rotate the compressor on the mounting bolts to the most desirable position (Ref Fig.4.).
F
Install the locking nuts with the nylon locking flange facing away from the backing plate
and tighten to a torque of approximately 6 Nm [4.4 ft-lb].
F
Rotate the compressor motor in the mount to its most desirable position and tighten the
two mount screws (4mm hex key) to a torque of approximately 3 Nm [2.2 ft-lb].
(Ref Fig.1.)
F
Rotate the grey manifold tube and the black manifold cap into the best position and then
tighten the manifold bolt (10mm socket) to approximately 9 Nm [6.6 ft-lb] (Ref Fig.2.).
2.4 Installing the Solenoid(s)
This step applies to the 12V solenoid that is packed with each ARB
Air Locker
differential. If
the compressor is to be used for an alternate purpose then simply skip this step and plug or
terminate the ports as required by the application.
F
Remove one of the
1
/
8
” BSPT plugs from its port in the compressor manifold using a 5mm
hex key. This plug may be discarded.
F
Apply Teflon paste/tape to one end of the nipple (
1
/
8
” X
1
/
8
” BSPT supplied with the
Air
Locker
), insert into the port and tighten.
NOTE : Pressure fittings do not require high torque to form an air tight seal.
Do not tighten any more than hand tight or damage to the manifold or
fittings may occur.
F
Apply Teflon paste/tape to the free end of the nipple.
F
Assemble the inlet port side of the
Air Locker
solenoid (marked as port ‘
1
’) onto the
nipple and tighten. The solenoid should be rotated into a position that does not obstruct
any other ports on the compressor manifold.
NOTE : The solenoid exhausts compressed air through the center of the black
retaining cap when the Air Locker is disengaged. Make sure this orifice
cannot be obstructed.
F
Assemble the 5mm push-in fitting into the solenoid outlet port (marked as port ‘
2
’) and
tighten using a wrench/spanner. The O-ring of the fitting will form the seal.
NOTE : Pressure fittings do not require high torque to form an air tight seal.
Do not tighten any more than hand tight or damage to the fitting may occur.
F
If two
Air Locker
units are being controlled with this air source then repeat Section 2.4 for
the second solenoid.