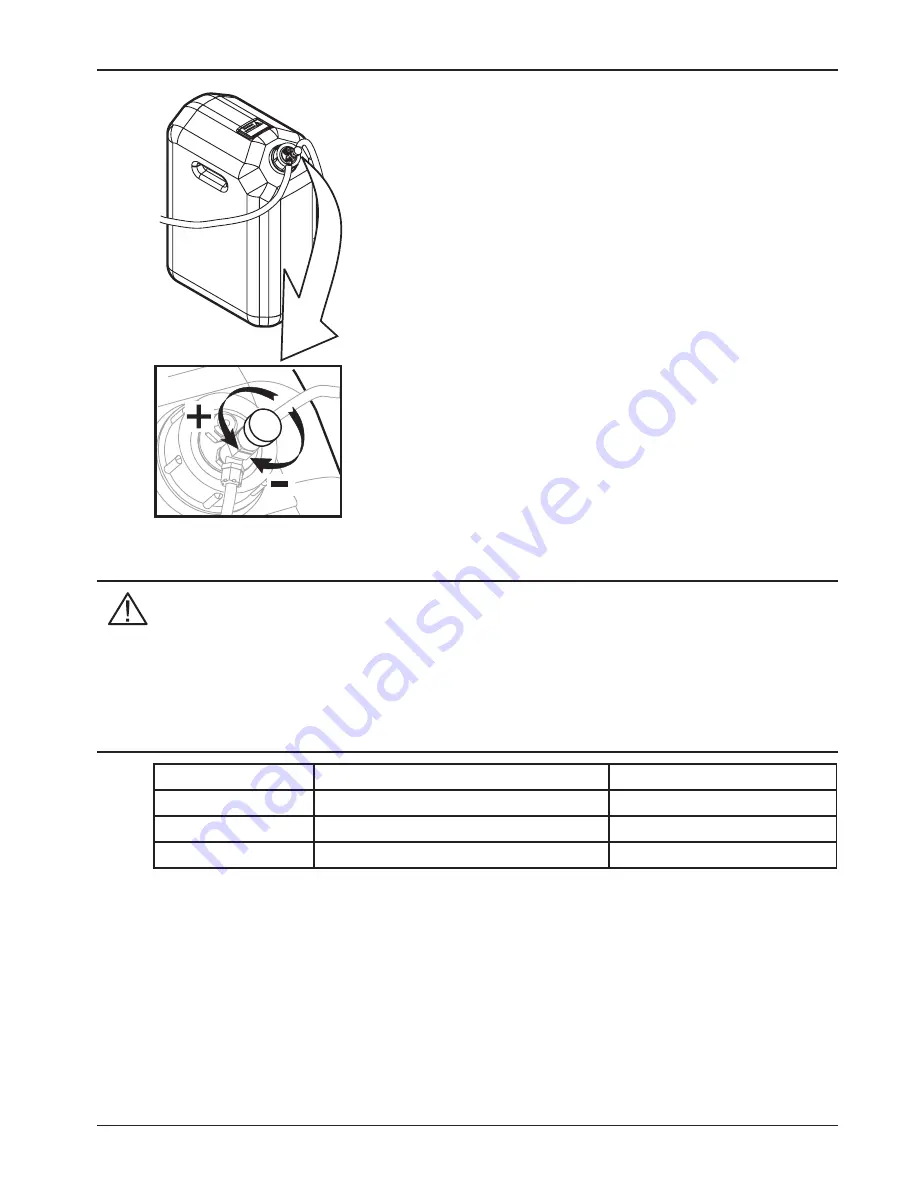
11
6.5
Starting and operating
Fig. 13
6.6
Topping up liquid
•
Depressurize the tank as indicated in par. 6.1 - Discharging remaining pressure.
•
Refill with liquid, observing the procedures described in the par. 6.4 - Preparing foaming
solution.
•
Use only ARAG foaming agents.
•
IN CASE OF DAMAGES TO THE FOAM MARKER CAUSED BY NON AUTHORIZED
FOAMING AGENTS, ALL WARRANTY CLAUSES WILL BECOME NULL AND VOID.
6.6.1 Foaming agents
CODE
CONTENT
PACKAGES
520050
5 lt / 1.32 US gal.
tank
520035
25 lt / 6.6 US gal.
tank
520033
200 Kg / 441 lb
barrel
•
Operate the selector lever (
A
, Fig. 12) onto the control box and
start the compressor.
•
The indicator turns on and the circuit reaches the operating
pressure after a few seconds causing the foam to come out
from the selected foam maker.
•
Adjust the intensity of the foam outlet, using the flow-rate
regulator on the tank cap (Fig. 13).
•
During use it is possible to alternate the right- or left-hand
foam nozzle by moving the selector lever.
•
To interrupt foam marker operation, set the switch to its central
position (OFF).