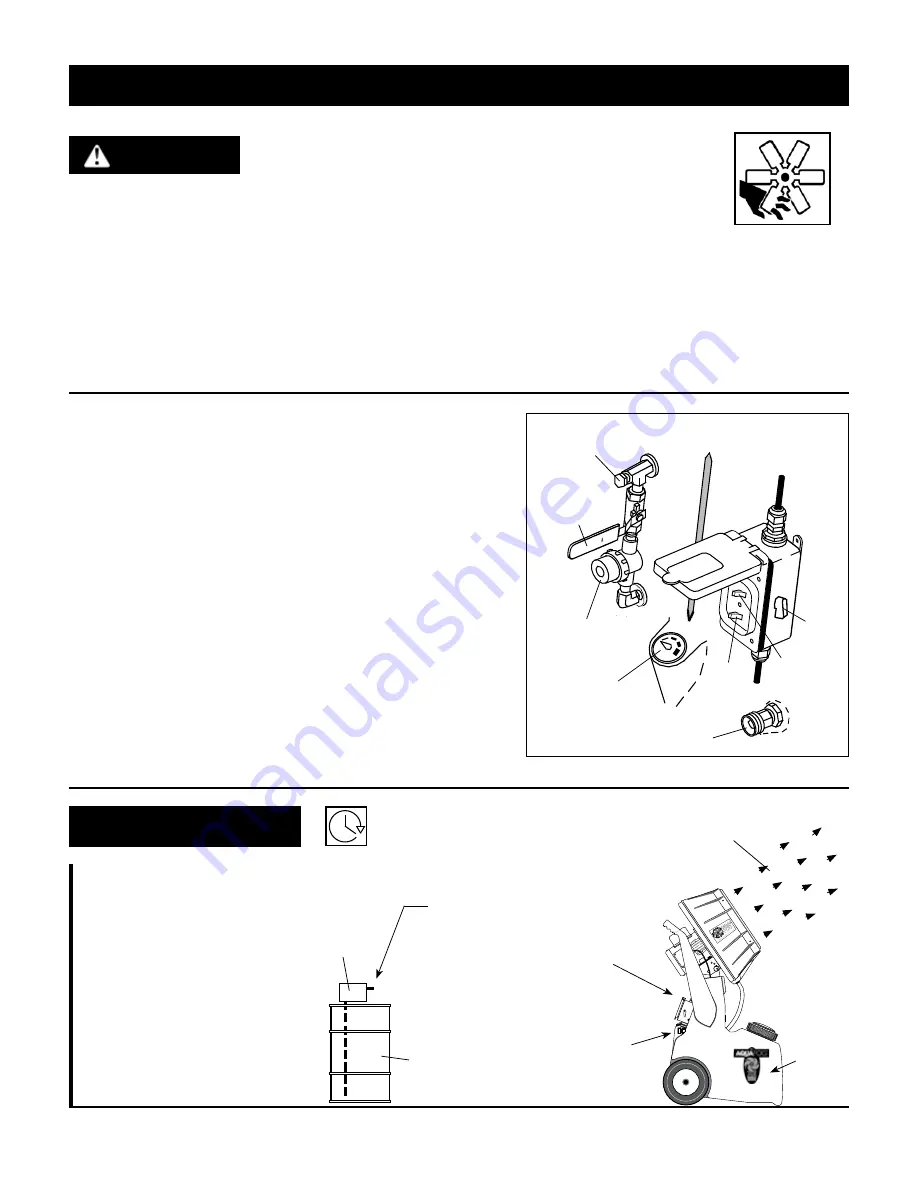
e
valuation
/ c
ontrols
/ i
nstallation
BEFORE TESTING FAN MAKE SURE ALL OBJECTS ARE OUT OF THE
ROTATION PATH OF THE FAN BLADES.HIGH-SPEED WARNING.
KEEP HANDS
CLEAR!
MAKE SURE GUARDS ARE INSTALLED OR UNIT IS OUT OF REACH.
DANGER
►
For first-time evaluation, fill tank (with water only) about quarter full.
►
Connect to power supply.
►
BUMP START ORSM and check for proper fan blade rotation (clockwise if looking at front of unit). If incorrect,
find rotation connection changes on the motor's electrical schematic.
►
Turn on the unit and listen for any possible abnormalities, such as the blades rubbing against the
venturi or any objects. Make re-adjustments if necessary.
►
Evaluate fog quality adjusting the output by using the flow control valve. (See
Fig. 2
).
After starting, it generally takes several seconds for the liquid to reach the atomizing fan.
The volume of fog can be regulated by adjusting the Flow Control
Valve. (See
Fig. 2
)
Particle size is smaller/drier at lower outputs, so it is wise to
operate the unit at a lower output for longer periods of time rather
than high outputs for short periods of time.
At the base of the plumbing is an in-line strainer with a removable
cap. Occasionally check inside and flush any sediment from the
screen.
The Hose Connection is used to supply fresh water to the unit and is
controlled by an internal float valve assembly.
Rain-tight Double-throw On - Off switch box.
Upper Switch - Fan Motor
Lower Switch - Feed Pump
A Fluid Level Gauge to aid in monitoring the tank's 18 gallon capacity.
Back Controls
Fig. 2
*
Connection for metering pump (3/8" fitting provided).
▼
▲
OFF
ON
Fluid Level Gauge
On/Off
Fan Motor
Key
Hose Connector
On/Off
Pump
Inline
Strainer
Flow Control
Valve
*Metering
Pump Inlet
5
A) Mobile Treatments
For short-term use, simply fill
the tank with diluted chemical
product and operate manually.
B) Stationary Treatments
For long-term operation,
connect to a metering pump,
with chemical concentrate
and water hose. Calibrate
water flow-rate to match the
chemical's dilution ratio.
s
etup
A timer can be set-up to control power
to the Metering Pump and ORSM
simultaneously.
Water Connection
Metering
Pump
Chemical
Concentrate
The metering pump connects
directly to the ORSM, dosing
concentrate into the water flow
traveling to the fogging head.
►
18 Gal.
Tank
Atomized
Chemical Mixture