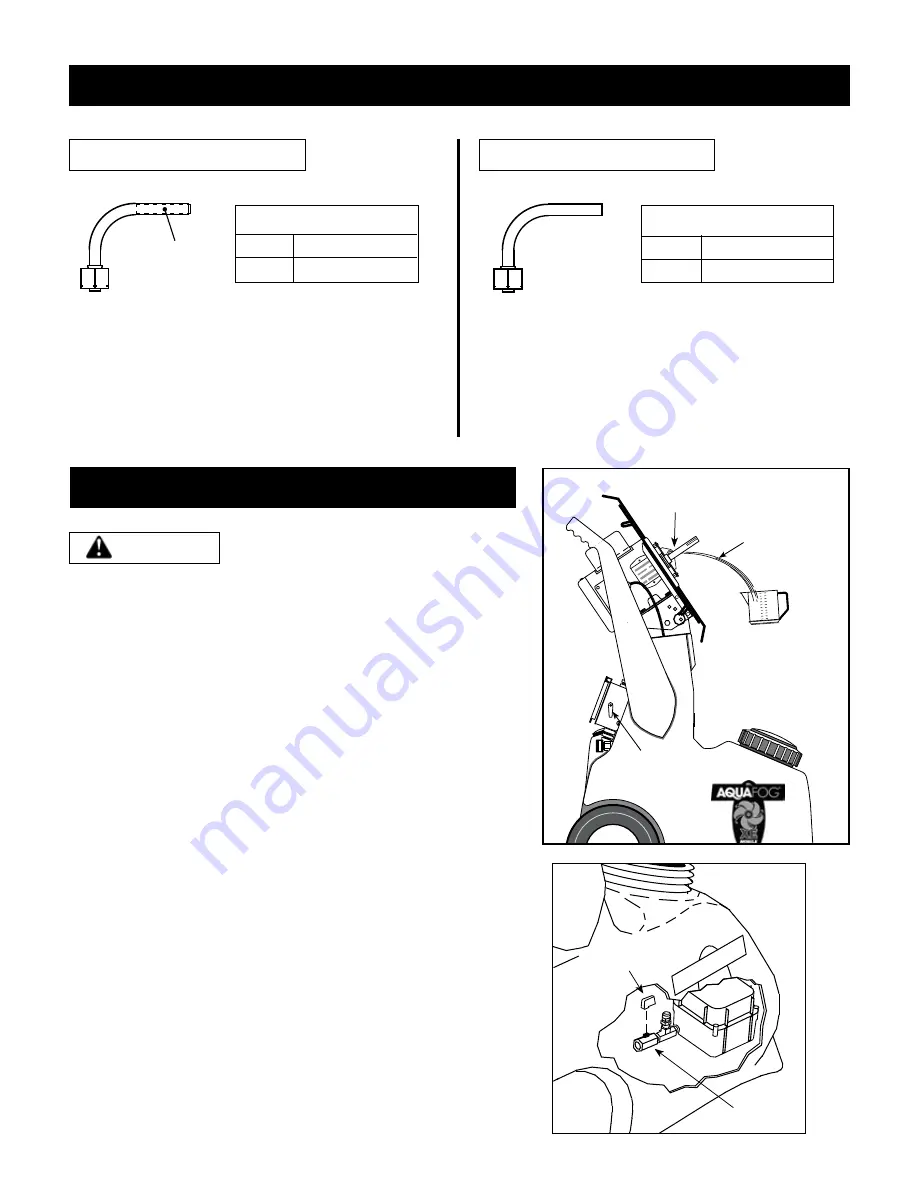
16
14
12
10
8
6
4
2
KEY's Storage
Location
c
alibrate
the
f
low
r
ate
Calibrated Flow Rate
Means having a (set) specific flow rate when the Flow Control Valve is
fully open. This allows for an easy repeat of fogging operations.
Also, the flow rate can be calibrated to match with a chemical's
dilution ratio. An important feature when using a metering pump.
To Calibrate a Flow Rate
(Two Techniques)
Fill the tank with some water.
T1)
Carefully remove the housing's drain tubing from the tank.
Tilting the fogging head temporarily, will ease removal.
[or]
T2)
Remove the Fan Housing and Blade Assembly to expose the
Feed Tube (See
Fig. 3
). This will allow a visual of the
water stream, helpful when making adjustments.
Fully open the Flow Control Valve located on the back of the unit.
Only turn on the feed pump (lower switch). Use a measuring cup
to catch water in 60 second intervals from the Feed Tube or Drain
Tubing. Multiply ounces of water by 60 and then divide by 128. This
will give you your GPH rate. Use the Key on the internal valve to make
adjustments and repeat process as needed (see below).
Math example: 1 minute captures (4.2 ozs. x 60 ÷ 128 = 2 GPH)
The valve KEY is needed to make changes
You will need the KEY located on the side of the electrical control box
to make changes (see
Fig. 3
). Slide this key on top of the flow valve's
stem (see
Fig. 4
) to make your adjustment.
After calibration remove handle to safeguard the flow rate.
Fig. 3
AUTOMATIC PRIMING OF THE SYSTEM
OCCURS THROUGH THE FLOW RATE VALVE.
NOTICE
f
low
r
ates
6
R
S
M
AQU
AFOG
Flow Rate
Valve KEY
Fig. 4
Capture & Measure
Water Output
Feed Tube
LOW FLOW, Feed Tube
Colored
Insert
HIGH FLOW, Feed Tube
Low Flow Tube (factory installed)
The Low Flow tube is more accurate, reliable and easier
to adjust at low flow rates.
It can be identified by its colored insert.
High Flow Tube (provided)
To install the high flow tube, first disconnect power.
Then gain access to the feed tube location by removing
the housing and fan blade assembly (see Fig. 3).
Replace tube, maintaining the same angle of the tube
installed by the factory.
Output Range:
@ 60Hz .75 - 3.75 GPH
@ 50Hz 2.8 - 14.0 LPH
Output Range:
@ 60Hz 3.0 - 11.25 GPH
@ 50Hz 7.6 - 31.2 LPH
Every
2.13 ozs per
minute = 1 GPH
Caibrate
Flow Rate